Hallo, Gast |
Du musst dich registrieren bevor du auf unserer Seite Beiträge schreiben kannst.
|
Benutzer Online |
Momentan sind 85 Benutzer online » 4 Mitglieder » 81 Gäste
|
Aktive Themen |
Wo kauft ihr ein?
Forum: Allgemein
Letzter Beitrag: marco91
27.05.2025, 14:49
» Antworten: 1
» Ansichten: 140
|
Streamingzimmer einrichte...
Forum: Allgemein
Letzter Beitrag: marco91
27.05.2025, 14:30
» Antworten: 1
» Ansichten: 111
|
Werbebriefe?
Forum: Allgemein
Letzter Beitrag: fritz500
12.05.2025, 17:56
» Antworten: 1
» Ansichten: 191
|
Auto privat verkaufen?
Forum: Allgemein
Letzter Beitrag: fritz500
12.05.2025, 16:21
» Antworten: 1
» Ansichten: 173
|
Vape welche Sorte?
Forum: Allgemein
Letzter Beitrag: conradme
05.05.2025, 20:52
» Antworten: 1
» Ansichten: 205
|
Was tun in Hamburg?
Forum: Allgemein
Letzter Beitrag: conradme
05.05.2025, 19:32
» Antworten: 1
» Ansichten: 199
|
Automatisierung in der In...
Forum: Allgemein
Letzter Beitrag: maxmeyers
25.03.2025, 13:20
» Antworten: 1
» Ansichten: 608
|
Kurzwaren im Internet?
Forum: Allgemein
Letzter Beitrag: fritz500
25.03.2025, 08:54
» Antworten: 1
» Ansichten: 524
|
Mittel gegen schwitzen?
Forum: Allgemein
Letzter Beitrag: fritz500
25.03.2025, 08:00
» Antworten: 1
» Ansichten: 534
|
Sportbootführerschein onl...
Forum: Allgemein
Letzter Beitrag: marco91
24.03.2025, 22:16
» Antworten: 1
» Ansichten: 506
|
|
|
Beglaubigte Urkunden? |
Geschrieben von: fritz500 - 04.05.2022, 05:14 - Forum: Allgemein
- Antworten (3)
|
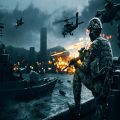 |
Guten morgen Community,
könnt ihr mir sagen, wie lange es ungefähr dauert, bis man mehrere beglaubigte Urkunden
von der Stadt bekommt, wenn man diese beantragt?
|
|
|
xingang-wood.com |
Geschrieben von: bop20mo - 29.04.2022, 02:46 - Forum: News
- Keine Antworten
|
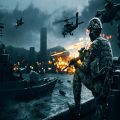 |
Plywood is one of the most widely recognized multi-purpose engineered wood-based panel products used in Canadian construction projects. Plywood binds resin and wood fibre sheets to form a?composite material sold in panels. A typical plywood panel has face veneers of a higher grade than the core veneers. The function of the core layers is to increase the separation between the outer layers where the bending stresses are highest, improving resistance to bending forces.
How is plywood made?
Plywood panels are fabricated from multiple layers or plys of softwood veneer glued together with the grain direction of each layer of veneer perpendicular to that of the adjacent layers. These cross-laminated sheets of wood veneers are fastened together with a waterproof phenol-formaldehyde resin adhesive and cured under heat and pressure. In BC, plywood is made from softwood species, usually Douglas-fir or spruce, pine and fir?(collectively known as?Canadian softwood plywood—or CSP). The most common dimension is 4 feet × 8 feet. Plywood varies in thickness, the most common being ?-inch.
What is plywood used for?
There are a range of plywood products like Film Faced Plywood, Commercial Plywood, Melamine Plywood, Fancy Plywood, PVC Plywood, HPL Plywood, etc. for structure and non-structural uses suitable for both wet and dry service conditions, including subflooring, single-layer flooring, wall, roof and floor sheathing, structural insulated panels, webs of wood I-joists and concrete formwork. As exterior wall and roof sheathing, plywood can provide resistance to lateral forces such as wind and earthquake loads and form an integral component of the building envelope. It may be used as both structural sheathing and finish cladding. For exterior cladding applications, specialty plywoods are available in a broad range of patterns and textures, combining the natural characteristics of wood with the strength and rigidity.
Sometimes we face the challenge of choosing between various materials for the same task or furniture. There are so many things that you have to consider, like the cost, durability, aesthetics, and so on. Plywood and particle board are similar types of materials that can be used alternatively, or maybe not. The usage or application of either of these materials depends on a lot of factors. While both materials are available in similar sheets and varying thicknesses, you might not know how each of them can be used at home.
Simply put, particle board is a waste-wood product made by heat pressing wood chips, sawmill shavings, or even sawdust and resin together. To make the end product water resistant, fireproof, and/or insect-proof chemicals are used including wax, dyes, wetting agents, and release agents. After the resin, chemicals, and wood scraps have been mixed together, the liquid mixture is made into a sheet. The weight of the wood chips is evenly distributed to make sure the finished board is not top heavy. Compression is applied to the particle board sheet multiple times to create the tightest possible bond between the resin and the wood bits. A popular type of particle board that you may see is oriented strand board (OSB). This wood composite is very important to home and commercial engineers for structural purposes. Oriented strand board is easily identifiable by its manufacturing process that layers strands of wood in specific orientations. Most home and commercial builders use OSB particle board for floor and wall bases. And also, there are many different kinds of particle board, such as Melamine Particle Board, Ordinary Particle Board and so on.
Now that you know what particle board means, it is important to differentiate clearly between the advantages of particle board vs plywood. Particle board has plenty of advantages in its kitty that can make it the ideal choice for a lot of things.
The surfaces of particleboard is usually smoother than that of plywood.
Particle boards are created using scraps of other lumber products, which makes it environment-friendly.
Particle boards are very light in weight. Furniture made from these boards is relatively easy to transport and move around.
Particle board is definitely more cost effective than plywood.
|
|
|
sjmoulds.com |
Geschrieben von: bop20mo - 29.04.2022, 02:43 - Forum: News
- Keine Antworten
|
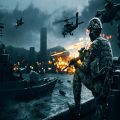 |
Manufacturers used several injection moulding techniques to create medical device parts suited to a range of different uses. Much like consumer products, medical Mold device technology is becoming smaller as manufacturing processes become more advanced, and injection moulding has allowed the size of parts to keep pace with this demand for smaller devices. According to a recent report from market insight firm 360 Research Reports, the global market for plastic injection moulding for medical devices is projected to reach over $42bn by 2026, up from $31.6bn in 2020. But there are several techniques used by companies that produce these parts for medical devices, as well as specific materials better suited to some methods than others, like metals and composites.
From thin wall moulding with liquid crystal polymers (LCP) to the more commonly known 3D printing technique, we look at five types of injection moulding technology used to manufacture medical devices.
Five types of injection moulding used in medical devices
1. Thin wall moulding
Thin walls can be both a functional benefit and improve patient comfort when it comes to certain medical devices. The term itself simply means creating the walls of a device in a way that makes them thin relative to the whole piece, but in practice this tends to mean walls thinner than 1mm. The technique requires regular injection moulding equipment, but in order for walls to retain their structural integrity as they are created thinner, the base material used tends to be plastics like LCP, polypropylene and nylon – although silicone and metal can also be moulded this way.
Material selection will depend on the device being produced and will have undergone testing at different levels of physical pressures and temperatures to ensure they can do the job. Thin walls are often found in wearable devices and micro surgical tools, but can also be used in invasive equipment like catheter ablation tools and endoscopes.
2. Gas-assisted injection moulding
When parts are created with regular injection moulding there’s a risk that sink marks can occur, making the final product look unsightly and potentially structurally weaker than it needs to be. The reason this happens is because thick areas of a mould cool more slowly than thin ones when the resin is injected, and without enough pressure to pack these areas tightly against the walls, the uneven distribution can cause a sunken appearance.
Gas-assisted injection moulding is used to solve this issue by running gas (usually nitrogen) through channels built into the mould. The gas carves a hollow path through the middle of these thicker sections and creates the pressure needed to force the resin tightly against the walls of the mould, creating a smooth part that is structurally sound with no sink marks. This method is used to create complex parts without any visual blemishes, but because the pressure exerted by the gas lessens if it doesn't flow in a relatively straight line, it isn't recommended for parts with sharp corners in their design.
3. 3D printing
The most recognisable technique on this list, 3D printing is not technically a form of injection moulding, but it does tend to be used to create prototypes to test a design before it goes into production using injection moulding. The 3D printing method can also be used to print actual injection moulds, using plastic or metal, but currently available technology is not advanced enough to print with the narrow part tolerances required in an injection mould – although many expect this will change in the future.
For certain medical device parts, metal isn't necessary to create a mould for the injection moulding process, so 3D printing is commonly used to create moulds out of plastic instead.
4. Metal injection moulding
Although traditional injection moulding and even gas injection moulding have numerous uses in medical device manufacturing – sometimes the small size coupled with both manoeuvrability and strong mechanical properties necessitates the use of metal over plastic.
In metal injection moulding, a powder made from the desired mix of metals is created using atomisation technology, and this powder is made into a pellet-like form called feedstock, which includes a plastic binding agent to make the substance easier to mould during the injection process. Once the mixture is injected, the binder is removed using solvent, thermal furnaces, a catalytic process, or a combination of methods, leaving only the metal and resulting in close to 100% density.
5. Liquid silicone injection moulding
While surface-borne infection is a general concern in hospitals, some medical devices have a greater need to remain hygienic than others, like tubes and respiratory masks. Liquid silicone injection moulding is used for devices like these because of the chemical resistance of the rubber-like substance produced using this method, as well as the use of a clean production room so that no ambient air makes contact with the mould and lets dust and moisture into the mixture as it sets.
Another benefit is that silicone is biologically inert, meaning it doesn't react with biological tissue and can be implanted safely in the body. The basic raw material for silicone rubber is sand, or silicon dioxide, which is processed into pure silicon and reacted with methyl chloride, after which a range of processing steps are used depending on the properties desired for the silicone.
In short, medical mold has become famous and widely used. Many products like IV Set Mold, Syringe Mold, Hypodermic Needle Mold, Blood Collection Mold, Blood Tubing Set Mold, Lab Equipment Mold, etc. become commonly used.
|
|
|
shelfmanufacturer.com |
Geschrieben von: bop20mo - 29.04.2022, 02:40 - Forum: News
- Keine Antworten
|
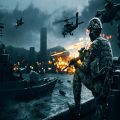 |
In the minds of many people, storage shelves have no functions except for some goods. In fact, shelves play an irreplaceable role in the entire Storage System. In order to realize modern storage and efficient storage and retrieval, warehouse managers are not only There are requirements for the quality and precision of the shelf, as well as higher requirements for its automation and mechanization. So what functions does such a charming shelf have?
1. The upper space can be fully utilized
The height of the shelves can be set to the unused space in the upper storey of the warehouse, and the goods can be placed in a high place without stacking up as before. At this time, forklifts are needed.
2. can make the goods safer
The goods are placed on the Shelves, which not only prevents the goods from contacting the warehouse floor and is damp, but also ensures that the packaging of the goods will not be broken, etc.
3. reduce time cost
The goods of the same variety can be put together to facilitate positioning and access, which can reduce time cost and labor cost.
4. anti-theft
Because the goods are clearly placed and positioned accurately, it is convenient to count the goods, and the shelves are neatly arranged and can be seen at a glance, so there is no fear of someone stealing.
5. improve the efficiency of warehouse access
Storage racks can be used together with forklifts and elevators, so that the efficiency of entry and exit is higher.
In short, it is precisely because the Storage Shelves can make full use of the upper three-dimensional space of the warehouse, ensure that the goods are safer, facilitate inventory and positioning, protect quality from dust and theft, and help mechanization improve efficiency. In addition, there are also many types pf selves for different usages, such as Supermarket Metal Shelves, Wood Shelves, Display Shelf including Tool Display Shelf, Cosmetic Display Shelf, Oil Display Shelf, Custom Display Shelf, etc.
Another item pretty similar to selves is called rack. One can store many things in a storage rack. It can either be used for industrial or for personal use. Modern day homes do not require a cellar to store the things; they can now depend on a good-looking, functional storage rack that fulfils its role by storing whatever is desired.
Storage racks are now available as shelf units. They do not require any kind of attachments. All you need to do is to purchase a rack and you are ready to store all your things. Storage racks offer sophisticated storage design and can provide you with much needed space. If you choose these racks, then you will be able to observe the efficiency of these storage racks and how they can have a positive effect on your day to day activities. If you have many CD's and DVD's, then by storing them in these types of racks you can create your own entertainment zone.
The system components for storage racks are diverse and varied. However they all have an elegant and modern look. Any number of combinations can be arranged to suit your operational requirements. Different customers have different needs and requirements so these racks like Fruit and Vegetable Racks, Wine Racks, Warehouse Rack and so on can be tailored according to the client's specifications. Storage racks provide space efficiency. This can help you keep your home neat and tidy.
|
|
|
sheerherb-bio.com |
Geschrieben von: bop20mo - 29.04.2022, 02:37 - Forum: News
- Keine Antworten
|
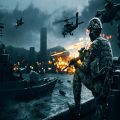 |
Men's Health Month was this past June and was recognized with screenings, health fairs, and other health education activities. The goal was to heighten awareness of preventable health problems and encourage early detection and treatment of diseases among men and boys.
The top causes of death among adult men in the United States are heart disease, stroke, cancer, and chronic lower respiratory disease, according to the Mayo Clinic and the Centers for Disease Control (CDC). In addition, men die at higher rates than women from the top 10 causes of death. According to the CDC, in 1920, women lived, on average, one year longer than men. Now men, on average, die almost five years earlier than women.
Some of today's health concerns for males include heart health and prostate cancer as well as body composition and recovery in the sports nutrition area. Some of the Men's Health Products and ingredients that can play a role in men's nutrition include omega-3 fatty acids, lycopene, and lean protein. Here's a look at some of the health concerns that men have and the nutrients that may play beneficial roles in addressing these concerns.
Heart disease is the leading cause of death for men in the United States, resulting in approximately one in every four male deaths, according to the CDC. In addition, the 2013 overall rate of death attributable to cardiovascular disease was 222.9 per 100,000 Americans. The death rates were 269.8 males and 184.8 for females (Mozaffarian et al. 2016).
High blood pressure, high low-density lipoprotein (LDL) cholesterol, and smoking are key risk factors for heart disease. Nutraceutical ingredients like antioxidants, omega-3 fatty acids, and plant sterols can help with these factors. Nutritional ingredients, including soluble fiber, soy protein, and plant sterols, have FDA-approved health claims linking them to a potential reduced risk of coronary heart disease. In a review of different types of fiber, Viuda-Martos et al. (2010) reiterated that evidence suggests that the increased consumption of insoluble as well as soluble dietary fibers can directly impact the risk of developing cardiovascular disease by targeting risk factors such as elevated serum LDL cholesterol levels.
Plant sterols also have an effect on cholesterol. They are substances that occur in small amounts in plant-based foods, which have structures similar to cholesterol and can prevent cholesterol from being absorbed into the bloodstream. Cargill, Minneapolis, Minn. (cargill.com), offers CoroWise plant sterols. A daily intake of 2 g of plant sterols as part of a diet low in saturated fat and cholesterol is recognized to provide significant cholesterol-lowering benefits.
Grape seed extract has been shown to have benefits on hypertension and cholesterol. Polyphenolics, Madera, Calif. (polyphenolics.com), offers MegaNatural BP, a patented grape seed extract made from a special seed blend from unfermented varietal wine and juice grapes. Polyphenols are extracted from grape seeds using hot water. The extract is then purified, concentrated, and spray dried into powder. Robinson et al. (2012) demonstrated that both the systolic and diastolic blood pressures of the prehypertensive subjects in the study were significantly lower after treatment with 300 mg of grape seed extract.
A patented tomato seed extract, Fruitflow, from DSM, Parsippany, N.J. (dsm.com), has been shown to contribute to healthy blood flow. According to the company, 8 human trials showed that the consumption of Fruitflow helped maintain healthy platelet aggregation and improved blood flow. This happens within 1.5 hours and lasts for 12 to 18 hours.
Finally, omega-3 fatty acids are also recognized for their heart health benefits. Reported mechanisms of action include improved heart rhythms, improved heart rates, improved blood lipids, reduced blood clotting, and less inflammation.
Without doubt, men also need other products to care about other issues they may be easy to get, like Weight Loss Ingredients, Medicine and Health Raw Materials, Vitamins and Amino Acids, Peptides, Organic Protein, Plant Extracts, Nutrition Fortification and may other Cosmetic Raw Materials.
|
|
|
purestchem.com |
Geschrieben von: bop20mo - 29.04.2022, 02:34 - Forum: News
- Keine Antworten
|
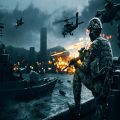 |
What are Pharmaceutical Intermediates?
Pharmaceutical intermediates are chemical compounds that form the building blocks of active pharmaceutical ingredients (APIs). Pharmaceutical intermediates are produced as by-products during the production of APIs. Each reaction in the API production process produces a variety of different pharmaceutical intermediates. It can only be turned into API by further molecular change or refinement. Intermediates can be separated or not separated. Pharmaceutical intermediates are used in the production of bulk drugs and are also used by various pharmaceutical and biopharmaceutical companies for research and development purposes.
What is API?
API (active pharmaceutical ingredient) refers to the active ingredient contained in a drug. Any substance or mixture of substances intended for use in the manufacture of a drug (drug), when used in the manufacture of a drug, will become the active ingredient of the drug product. Such substances are intended to provide pharmacological activity or other direct effects in the diagnosis, cure, mitigation, treatment or prevention of a disease, or to affect the structure or function of the body.
If you consider an example-in a Tamiflu brand tablet, oseltamivir 30 mg is actually API (a powder responsible for the tablet's ability to treat influenza). But in fact, the tablet contains more than 30 mg of oseltamivir. In addition to oseltamivir, the tablet may also contain some colorants, binders, fillers, preservatives, etc. All these materials are collectively referred to as "excipients". Therefore, the combination of API (oseltamivir) and excipients (binders, fillers, colorants, etc.) constitutes any finished medicine (tablets, capsules, syrups, etc.)
What is the Difference Between API and Intermediate?
From the perspective of new drug development, an API is a compound that can be safely used in the human body for therapeutic diagnosis after sufficient pharmaceutical research. The pharmaceutical intermediate is a compound in the process of synthesizing the API, which may not have a therapeutic effect or be toxic. Please note that this is not necessarily the case, some intermediates in the synthesis of APIs are also APIs.
From the perspective of pharmaceutical management, APIs must be registered with the drug regulatory authority (FDA in the US and EMEA in Europe) according to law and synthesized in a GMP-compliant plant after obtaining the approval number. The intermediate is only a byproduct in the process of synthesizing the API and does not need to obtain an approval number. It should be noted that although some compounds are the same as APIs, if they have not obtained the approval number or are not produced in the GMP factory, they are not APIs.
Traditionally, APIs and intermediates are produced by pharmaceutical companies in their home countries. But in recent years, many companies have chosen to shift manufacturing overseas to reduce costs. As a result, many pharmaceutical companies are located in the United States and the United Kingdom, but most API and intermediate manufacturers are overseas. The largest regions are in Asia, especially India and China. Some researches indicate that compared with North America and Europe, the production costs associated with pharmaceutical intermediates, APIs, and final drug formulations are about 50-60% lower in emerging Asian markets. This has caused significant changes to how these drugs are regulated, with more rigorous guidelines and inspections put into place.
Except for Pharmaceutical Intermediates, lots of Pesticides and Pesticides Intermediates are widely used in agriculture and production.
|
|
|
jtl-diecasting.com |
Geschrieben von: bop20mo - 29.04.2022, 02:30 - Forum: News
- Keine Antworten
|
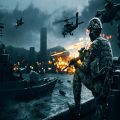 |
Aluminum Alloy Parts are a composition consisting mainly of aluminum to which other elements have been added. The alloy is made by mixing together the elements when aluminum is molten (liquid), which cools to form a homogeneous solid solution. The other elements may make up as much as 15 percent of the alloy by mass. Added elements include iron, copper, magnesium, silicon, and zinc. The addition of elements to the Aluminum Parts gives the alloy improved strength, workability, corrosion resistance, electrical conductivity, and/or density, compared with the pure metallic element. Aluminum alloys tend to be lightweight and corrosion resistant.
And the Die Casting Aluminum Alloy Parts can be used for Aluminium Die Casting, Permanet Mold Casting and so on. These Aluminum Alloys will become the best High Pressure Die Casting Parts and Pressure Die Casting Parts.
Identifying Aluminum Alloys
Alloys have common names, but they may be identified using a four-digit number. The first digit of the number identifies the class or series of alloy.
1xxx - Commercially pure aluminum also has a four-digit numerical identifier. Series 1xxx alloys are made of 99 percent or higher purity aluminum.
2xxx - The principal alloying element in the 2xxx series is copper. Heat treating these alloys improves their strength. These alloys are strong and tough, but not as corrosion resistant as other aluminum alloys, so they are usually painted or coated for use. The most common aircraft alloy is 2024. Alloy 2024-T351 is among the hardest of the aluminum alloys.
3xxx - The main alloying element in this series is manganese, usually with a smaller amount of magnesium. The most popular alloy from this series is 3003, which is workable and moderately strong. 3003 is used to make cooking utensils. Alloy 3004 is one of the alloys used to make aluminum cans for beverages.
4xxx - Silicon is added to aluminum to make 4xxx alloys. This lowers the melting point of the metal without making it brittle. This series is used to make welding wire. Alloy 4043 is used to make filler alloys for welding cars and structural elements.
5xxx - The principal alloying element in the 5xxx series is magnesium. These alloys are strong, weldable, and resist marine corrosion. The 5xxx alloys are used to make pressure vessels and storage tanks and for various marine applications. Alloy 5182 is used to make the lid of aluminum beverage cans. So, aluminum cans actually consist of at least two alloys!
6xxx - Silicon and magnesium are present in 6xxx alloys. The elements combine to form magnesium silicide. These alloys are formable, weldable, and heat treatable. They have good corrosion resistance and moderate strength. The most common alloy in this series is 6061, which is used to make truck and boat frames. Extrusion products from the 6xxx series are used in architecture and to make the iPhone 6.
7xxx - Zinc is the principal alloying element in the series starting with the number 7. The resulting alloy is heat-treatable and very strong. Important alloys are 7050 and 7075, both used to construct aircraft.
8xxx - These are aluminum alloys made with other elements. Examples include 8500, 8510, and 8520.
9xxx - Presently, the series starting with the number 9 is unused.
What Is the Strongest Aluminum Alloy?
Manganese added to aluminum increases its strength and yields an alloy with excellent workability and corrosion resistance. The highest strength alloy in the non-heat-treatable grade is alloy 5052.
Aluminum Alloy Classification
In general, the two broad categories of aluminum alloys are wrought alloys and casting alloys. Both of these groups are subdivided into heat-treatable and non-heat-treatable types. Around 85% of aluminum is used in wrought alloys. Cast alloys are relatively inexpensive to produce because of their low melting point, but they tend to have lower tensile strengths than their wrought counterparts.
|
|
|
forefrontnail.com |
Geschrieben von: bop20mo - 29.04.2022, 02:27 - Forum: News
- Keine Antworten
|
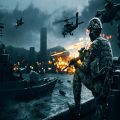 |
Remember when painting all 10 fingers and toes in black nail polish was the hot thing? Trends in nail fashions have come a long way, baby. The expected reds, pinks and taupes have been replaced by all shades of blue, green and yellow, sometimes even worn all at once on alternating fingers. And then there are the designs -- intricate works of art created on a tiny nail scale to add pattern and color. But getting this done at a nail salon can be costly and there's no guarantee it will last very long. Fortunately, manufacturers of nail products have figured out a way to get the same results at home.
Nail Sticker Pros and Cons
Nail stickers mainly function as nail art. You typically buy them in pre-cut sizes that cover your entire nail, or as decals or appliqués that add pattern and design to your existing nail look. One of the great things about nail stickers is that you can achieve intricate and artful details on your nails without paying a nail artist a lot of money to create them. This savings also means that you can afford to change it up more often. Unlike polish strips, some nail stickers have a little dimension to them so the patterns often look like they've been painted on. The decals usually come on clear sheets that let you look at different placements on your nails before peeling them off. The stickers are supposed to be easy to remove, usually just by soaking in warm water and peeling them off -- and the big bonus is they don't damage your nails. They're water resistant and if you use clear polish over them, they'll last a lot longer. And there are many different Nail Sticker for diferent design or functions like 3D Nail Sticker, Water Transfer Nail Sticker, Nail Foil Transfer Sticker and so on.
One of the big cons is the sizing and application process. The stickers come in one size fits most and the proportions don't always match up with your nail dimensions, so you may have gaps on the sides. Decals can be tricky to get on just right, especially when working with your non-dominant hand. If you apply stickers near the tips of your nails, they'll chip along with your nail polish, so it's best to keep them on the nail bed. One of the biggest pros is that they're quick and easy, but if you want to add shine that nail polish typically provides, at minimum you'll still have to apply a clear base coat. And while the stickers do come with an adhesive back, it's not meant to be permanent, so if you want them to stay on for a while, you'll also need to add a clear top coat. Neither of these are deal breakers, but they do add a little more time and effort.
Nail Polish Strip Pros and Cons
Polish strips are revolutionary products that are designed to make DIY manicures fast and easy. These products boast that they offer a base coat, a color coat and a top coat in one fell swoop. They're made of actual nail polish, so they have the look and shine that we're used to, but they don't have the drying time, chance of smudges and smears, or Q-tip clean up that wet polish requires, and they're just as easy to remove with nail polish remover. Polish strips come in nail shaped appliqués that are different sizes on each end to accommodate different sized nails. Unlike nail stickers, which are fixed widths, polish strips stretch length and width-wise to achieve a better fit. And if you don't get it on the first time, you can remove and reapply them without messing them up. They come in solids as well as patterns so you have lots of color options and are supposed to be durable enough to last up to 10 days.
But what goes up must come down, so as expected, there are some cons to these exciting products, which is mainly the price. They're only about 10 dollars a set, but this is considerably more costly than a bottle of nail polish and you get a lot more than a single application out of that. And just like nail polish, if they're not stored properly, they'll dry out. While they have more give in size than nail stickers, if you have oddly shaped or overly large nails, you may still have a tough time making them fit perfectly. And while they're easy to remove, they may leave your nails feeling a little brittle and rough, much like after you've had polish on for a while. The quality of the product varies among different manufacturers, so you may have to try a few different kinds to find the ones you like best. And beware -- because of their stretchy nature, the patterned designs may not remain consistent within a single nail or from nail to nail.
Except for the two mention above, there are other Nail Tools for Nail Art Decoration such as Nail Glitter and Nail Powder, Nail Rhinestone, Nail Sequins, etc.
|
|
|
cnshangde.com |
Geschrieben von: bop20mo - 29.04.2022, 02:24 - Forum: News
- Keine Antworten
|
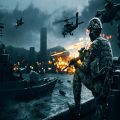 |
Trampoline, an elevated resilient webbed bed or canvas sheet supported by springs in a metal frame and used as a springboard for tumbling. Trampolining, or rebound tumbling, is an individual sport of acrobatic movements performed after rebounding into the air from the trampoline.
Although rebound tumbling has existed for centuries, it did not achieve wide popularity until the 20th century, when it became a featured attraction performed by circus acrobats. The modern sport was born in 1936 with the development of the present-day trampoline by American gymnast George Nissen.
The first unofficial American trampolining competition took place in 1947, followed by the first official American championships in 1954. The sport was included in the Pan-American Games for the first time in 1955. In 1962 the first open international trampolining event took place in West Germany, after which the first world championship was held in England in 1964. Immediately after the 1964 competition, officials from participating countries met to form the International Trampoline Association, the sport's worldwide governing body. Trampoline gymnastics debuted as an Olympic sport in 2000.
A competition consists of one compulsory and one optional routine, with the winners of those events performing another optional routine. Each routine is limited to 10 contacts with the trampoline, with competitors scored on difficulty, execution, and form. But for most of time, trampoline is used as an entertainment for children and family.
Finding ways to keep children occupied during the long days of summer can be a challenge! There is so much daylight and only so many activities you can come up with when your children need some outdoor play encouragement. But, if you have a trampoline (or know someone who does) your options for outdoor family fun are almost endless! And there are many types of trampoline with different shpaes or functions to choose from, such as Rectangular Trampoline, Oval Trampoline, Inground Trampoline, Fitness Trampoline, Big Trampoline, External Trampoline, Internal Trampoline, Luxury Trampoline, Children Trampoline, etc.
Trampoline newbies
Our family got our first trampoline this summer. I was a little nervous about it but I soon realized there is SO much fun be had and so many new trampoline games to play. My boys have already spent many hours on the trampoline this summer. Now that we have it I can’t imagine our yard or a summer evening without it. The trampolines of today, with their padded spring covers and fall-proof nets, are so much safer than the trampolines I grew up on. It's a lot more fun for us parents knowing the kiddos are safe.
Trampoline safety tips
Even though trampolines are designed to be safer than they used to be doesn't mean you still shouldn't take some precautions. Here are a few trampoline safety tips for kids. Go over these rules with your little ones before they play and remind them of the importance of being safe on the trampoline.
Adult supervision on a trampoline is always required.
Always use a safety net around your trampoline.
No gymnastic exercises or stunts, such as somersaults or flips.
Never allow children to bounce off the trampoline.
To prevent young children from getting on without supervision, do not leave a ladder or chair near the trampoline.
Make sure your trampoline is on a clear, flat area free from potential hazards, such as fences, hedges, trees, washing lines or other equipment.
Always carefully review the safety materials included with your trampoline.
|
|
|
|