Hallo, Gast |
Du musst dich registrieren bevor du auf unserer Seite Beiträge schreiben kannst.
|
Benutzer Online |
Momentan sind 85 Benutzer online » 1 Mitglieder » 84 Gäste
|
Aktive Themen |
Wo kauft ihr ein?
Forum: Allgemein
Letzter Beitrag: marco91
27.05.2025, 14:49
» Antworten: 1
» Ansichten: 145
|
Streamingzimmer einrichte...
Forum: Allgemein
Letzter Beitrag: marco91
27.05.2025, 14:30
» Antworten: 1
» Ansichten: 113
|
Werbebriefe?
Forum: Allgemein
Letzter Beitrag: fritz500
12.05.2025, 17:56
» Antworten: 1
» Ansichten: 197
|
Auto privat verkaufen?
Forum: Allgemein
Letzter Beitrag: fritz500
12.05.2025, 16:21
» Antworten: 1
» Ansichten: 175
|
Vape welche Sorte?
Forum: Allgemein
Letzter Beitrag: conradme
05.05.2025, 20:52
» Antworten: 1
» Ansichten: 209
|
Was tun in Hamburg?
Forum: Allgemein
Letzter Beitrag: conradme
05.05.2025, 19:32
» Antworten: 1
» Ansichten: 207
|
Automatisierung in der In...
Forum: Allgemein
Letzter Beitrag: maxmeyers
25.03.2025, 13:20
» Antworten: 1
» Ansichten: 618
|
Kurzwaren im Internet?
Forum: Allgemein
Letzter Beitrag: fritz500
25.03.2025, 08:54
» Antworten: 1
» Ansichten: 535
|
Mittel gegen schwitzen?
Forum: Allgemein
Letzter Beitrag: fritz500
25.03.2025, 08:00
» Antworten: 1
» Ansichten: 541
|
Sportbootführerschein onl...
Forum: Allgemein
Letzter Beitrag: marco91
24.03.2025, 22:16
» Antworten: 1
» Ansichten: 517
|
|
|
What is a ground-mounted solar panel? |
Geschrieben von: bop14mo - 21.04.2022, 02:40 - Forum: Allgemein
- Keine Antworten
|
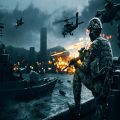 |
What is a ground-mounted solar panel?
Ground-mounted solar panels are solar panels that are installed at the ground level Ground-mounted systems function very similarly to rooftop solar systems – panels are exposed to sunlight which is converted to electricity by solar cells in order to power a single building or, in the case of solar farms, communities.
Here are the top three things that you need to know about ground-mounted solar panels and energy production:
1. In many cases, ground-mounted solar panels can be your best option
While rooftop solar arrays are the most common choice for homeowners, there are many reasons to consider a ground-mounted solar panel system.
Generally, ground mount solar panels cost a bit more than rooftop solar on a per-watt basis because of additional labor and permitting that may be required for the installation. That being said, if your property isn’t ideal for rooftop solar, installing a ground-mounted system can actually save you more money in the long run.
Rooftop solar arrays are restricted by the characteristics of the roof on which they are installed. If your roof isn’t at the right angle, doesn’t face south, or has obstructions like chimneys or skylights, then your solar array will be less productive. On the other hand, ground-mounted solar panels can be located wherever the conditions are best.
In addition, if your home uses a lot of electricity, your roof might not be big enough for a solar energy system that meets your electricity needs. In contrast, ground-mounted solar systems can be sized to match your electricity consumption without the space restrictions of a rooftop system.
2. Not all ground-mounted solar panel systems are created equal
There are two basic types of ground-mounted solar panel systems:
Standard ground-mounts use metal framing driven into the ground to hold your solar panels up at a fixed angle. Some standard ground-mounted solar panel systems can be manually adjusted a few times a year to account for seasonal shifts of the sun.
Pole-mounted solar systems support multiple solar panels on a single pole and elevate panels higher off the ground than a standard ground mount. Pole-mounted solar often incorporates tracking systems, which automatically tilt the solar panels to capture the optimal amount of sunshine.
Tracking systems can increase the production of your solar panels by 25 percent or more. If you decide to add a tracking system to your ground-mounted solar array, you have the option of either a single-axis or a dual-axis system. Single-axis tracking systems move your solar panels over the course of the day to follow the sun as it moves through the sky. Dual-axis tracking systems can also adjust based on seasonal variations in the sun’s position.
Solar Mounting Structures: Racking Matters
Globally, solar installations have been growing at an impressive pace. A large share of growth has been contributed from India, and with 100GW of target by 2022 in its hand, India is on the verge of becoming the world’s biggest solar nation. Continuous reduction in the solar system prices with respect to higher grid rates is resulting in increasing global demand for solar solutions and thus leading to its rapid growth. Solar is undeniable the future and a leading source of renewable energy. Solar panels work best when they receive shade free sunlight for maximum number of hours, mounted at precise tilt angle with face directed towards the south. This is where Solar Panel Mounting Structures comes into the picture. One of the largest areas of innovation within solar panel installation involves the mounting system.
Module Mounting Structures play a vital role in efficient working of a solar power system, both in utility and rooftop. While most of the components of balance of system (BOS) such as inverter, DC cables, junction boxes, transformers, etc. are readily bought from the equipment suppliers, the workmanship of an EPC contractor is reflected mainly through module mounting structures and wiring management.
These structures help panels to rest com-fortably, prevent from being damaged and more importantly position them at precise tilt angle to harness maximum sun’s energy. Mounting structures can be made for rooftops, ground mounting, carports and sun tracker solutions which now have seen a lot of developments in terms of weight, material, adaptability and ease of installation. There have been many technological innovations that have led to reduced cost, faster and better installation, high durability and with enhanced output.
Recent installation of solar project in India has adopted various Solar Mounting Tech-nologies and design which include the structures made of galvanized iron as well as aluminum structures. Some of the projects have adopted a combination of steel structure and aluminum structure where in vertical legs are made off hot dipped galvanized steel and rest of the members are made off extruded aluminum structure. Typically module mount structure comprises of following components.
Moreover, falling cost for module mounting structures has been one of the biggest contributor to the fall in project cost. They have fallen by almost 60% in the past 4-5 years. The manufacturing of structures is a fairly consolidated market with the top five companies in India controlling 80% of the market share. These players have a cumulative capacity of 2,300 MW per year. This might seem like a solid base for future growth. However, the demand in India is cyclical and driven by policies. Timely deliveries for the entire 2,300 MW will already be an issue, leave alone catering to a 4,000-5,000 MW market. The costs for mounting structures can also go up if there is a spike in capacity addition. However, this increase will be short lived as companies can start buying parts of the structure from other steel fabricators.
Any solar system is designed to function for 20 to 25 years thus material plays an important role in the overall solution. The strength of the material is defined by the geography and environment of the location being installed. Hence, there is a growing need for highly durable, rust-free, corrosion-resistant materials in the industry. This is leading to the emergence of evolutionary products like rust-resistant steel that have become highly popular in the solar panel market with its competitive pricing and greater durability. There are several types of steel depending on its weight, strength grade and coating which involves different prices. While selecting the material one should look at the warranty provided by the company for maximum return on investment. Probably, the most competitive solar product market, mounting systems are an important element of solar arrays—they secure solar panels to the roof or the ground. Here, we go over the basic categories of roof-mounted solar systems to help new installers get a grasp on installation.
Types of Solar Mounting Structures
The correct and proper choice of the Mou-nting Structures for solar system projects is very essential in terms of the overall production, efficiency and lifetime of the solar panels. Since it is a costly investment, the choice of mounting systems should not be disregarded as a minor consideration. Solar modules need to be secured, mounted and tightened on a very stable and durable structure, protecting the array against imp-acts from wind, hail, rain, snow and even minor earthquakes. They are either mounted on ground, on roofs or on poles. There are five basic types of mounting structures of which four are fixed-angle types and one variable-angle type:
- Roof Mounted Racks
- Ground Mounted Racks
- Top-of-pole Mounted Racks
- Side-of-pole Mounted Racks
- Tracking System Mounted Racks
Building-integrated Photovoltaics
Building-integrated photovoltaics (BIPV) are solar power generating products or systems that are seamlessly integrated into the building envelope and part of building components such as façades, roofs or windows. Serving a dual purpose, a BIPV system is an integral component of the building skin that simultaneously converts solar energy into electricity and provides building envelope functions such as:
- weather protection (water proofing, sun protection);
- thermal insulation;
- noise protection;
- daylight illumination; and/or
- safety.
Applications
BIPV systems can be installed during the construction phase of a building or deployed in the course of a retrofit of an existing building when one of the envelope components needs to be replaced. The built environment allows for many ways to integrate BIPV.
How are Roof Solar Panels Installed?
Installing solar panels on your roof is a complex project, one that many across the country are starting to explore. While most people know what solar panels are, many aren’t aware of the details involved in setting up a complete rooftop solar power system.
But first things first.
While this article outlines the different elements involved in installing a solar power system (not to mention several steps pertaining to the actual installation of the solar panels themselves) we highly recommend that you hire a certified professional to get the job done right. The purpose of this article is to arm you with more information on the process itself in order to better equip you for a project of this size and undertaking.
Types of Solar Power for the Home
There are a few ways in which you can generate power for your home through installing solar panels. It is important to understand your options in order to correctly set up your system and start benefitting from solar power. If you need more help deciding on the best option for your home, get in touch with a contractor. They will provide the additional information you need.
In general, there are three main types of solar power for the home. These include:
Grid Connected (no batteries)
This type of installation is the cheapest and easiest.
With this type of solar power, the system is connected to the grid without any back-up because you are using the grid in place of the battery. If your house requires more power, it will simply consume what it needs from the grid. When your system generates more electricity than you can consume, that power is given to the grid (local utility).
The credit amount you can receive for this excess power depends on your utility. One thing to keep in mind before you choose this type of solar power is that if the grid goes out, so does the power in your home.
Grid Connected (with batteries)
The main difference with this type of solar power system is that you will have batteries in addition to your connection to the grid. What this means is that the batteries will act as storage for power so that if the grid experiences a power outage, the power from your battery will keep your lights on. If your solar power system generates more energy than you consume, it will continue to go into the grid. This type of system can be quite expensive and are much more complicated to install. It is for this reason that this type of system is often used in hospitals (for example) because they have specific needs that require power at all times.
Off Grid
With this type of system, you are not connected to your utility. The system will generate, store and consume its own power, without any help from external resources. This installation is tricky because the contractor will need to know the exact amount of power you require. This system is more often used in rural areas where the cost of bringing in power from a utility is very high. This option is not really recommended if you live in a major city or populated area.
|
|
|
The Benefits of Back To Wall Toilets |
Geschrieben von: bop14mo - 21.04.2022, 02:38 - Forum: Allgemein
- Keine Antworten
|
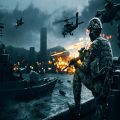 |
The Benefits of Back To Wall Toilets
With so many styles of sanitaryware to choose from, it can be difficult to know where to start. On choosing your preferred style of toilet, you'll want to know if it will entail any additional work. From your single washroom at the back of a restaurant to a multi-site rollout, the devil is in the detail.
What is a back to wall toilet?
A back to wall toilet essentially means that the user's back will sit flush against the wall when seated, as opposed to a cistern. When entering the cubicle, you'll be presented with the toilet pan, but the cistern, which holds the water for flushing, will not be visible.
Why choose a back to wall toilet?
A lot of people go for this option as it can make the space inside the cubicle seem much bigger. However, sometimes it's a move to prevent tampering or accidental damage. When the cistern is exposed like on your traditional domestic toilet, users can remove or damage moving parts. Back to wall toilets can also look very slick and smart, maintaining a simple design aesthetic throughout your wash space.
Things to bear in mind
Although back to wall toilets have no cistern on show, the water for flushing them has to come from somewhere. Most often, it is hidden within a false wall known as a duct set. This conceals all the pipework and the cistern within. This creates what’s known as an integrated plumbing system (IPS). The panels, which conceal the cistern can be removed with a key or special tool, making maintenance simple, but protecting your washroom from vandalism and accidental damage.
Hidden benefits
Because back to wall toilets are partnered with an IPS system, the cubicle has reduced surface areas. This is because you essentially have four flat wall surfaces and a small protruding toilet pan. This makes the washroom easier to clean and when used across large sites like schools, museums, and universities, can bring significant value. With fewer moving parts on display, they often need less maintenance compared to close coupled toilets too.
Wall Hung WC Pans
Cleaning Accessibility
Perhaps the most obvious advantage of the wall-hung toilet pan is down to the fact it hovers several inches off the floor. This allows you to easily clean around and underneath it. Unlike with a more conventional toilet style, there are no nooks and crannies for dust and dirt to get trapped in, no sealant holding it to the floor to discolour over time, and pretty much no hard-to-reach areas.
Many wall-mounted toilets have smooth sides that are easily wiped clean, and a good quality pan such as the Britton Compact Wall Hung Toilet have a special antibacterial coating for easy cleaning.
Superior Use of Space
Wall hung toilets are a great space-saver. Without the extra bulk of a visible cistern sitting on the pan they take up much less space in the bathroom, and can be placed closer to furniture, shower enclosures, or whatever else you are planning for your bathroom.
You do of course have to account for the space needed to conceal the hidden cistern and frame, but clever planning, use of stud walls and the latest compact designs means that overall, wall-mounted toilets are an excellent option for smaller spaces.
And it's not just the physical space they save. The fact that they are not sitting on the floor creates the illusion of a more spacious bathroom, with less clutter taking up floor space.
Wow-Factor & Style
Whilst taste is very much a subjective thing, most people are at the very least intrigued if not impressed by a toilet floating off the wall. They are certainly popular, but not prevalent enough to have become the norm in modern bathrooms, so a stylish wall-mounted toilet combined with a beautiful bathroom design always impresses.
Wall Mounted Toilet Weight Limit
A properly installed frame and wall hung toilet combination should comfortably support 200kg (30 stone) or more. If you're of a stocky build we don't recommend that you 'drop' down on it heavily but in all our years as a bathroom retailer we have never heard of a wall-hung toilet breaking off from the wall, or pulling down the entire stud wall.
Again, it stands to reason that you be selective with your choice of bathroom installer. An experienced plumber will know exactly how to install the toilet so it safely stands the test of time.
What is a Close Coupled Toilet?
There are so many different styles of toilets these days that our customers often get a bit overwhelmed. Sure it's easy for us, because we work with these products every day and it's our job to know them inside out, but that doesn't mean you have to. That's why we've put together this helpful guide that will explain exactly what a close coupled toilet is as well as a Q & A of the style too, to help you make the right choice for you and your new bathroom. Ready? Let's go…
Why is it called a close coupled toilet?
It's called a close coupled toilet because the bowl and cistern are closely coupled together, unlike the old fashioned edition in which the cistern was suspended overhead, often a few feet from the bowl. A close coupled toilet is a modern take on the traditional form and has been adapted to look modern or traditional to suit your style and bathroom theme.
How does a close coupled toilet work?
The toilet bowl and cistern are connected together allowing the water to evacuate from the cistern into the bowl using either a flush button or handle. Most models will have the option of either a 3 litre or 6 litre flush, which puts you in control of your home's water consumption.
How popular is a close coupled toilet?
A close coupled toilet is one of our bestselling styles. They are easy to install, low cost, durable and hard wearing, most come with a dual flush button, they're available in short projections which is ideal in a small bathroom or en-suite and they're immune from water damage.
Is a close coupled toilet old fashioned?
Only if you want it to be. We have a huge range of close coupled toilets to choose from with highly modern designs or classic traditional designs depending on the look you want to achieve.
One Piece vs. Two Piece Toilet: What's The Difference?
It's simple: A two piece toilet has a separate tank and bowl, while a one piece is all connected. But there are other differences, too. One piece toilets are typically heavier and easier to clean, and there's less space for bacteria to grow. Because two piece toilets feature a detachable tank, they're more customizable for preferred styles and heights.
Both styles can include bells and whistles like bidet attachments or low-flow energy saving. Also, either can be shaped in the standard styles: elongated, which is slightly longer, and round.
Because one piece toilets are heavier, they can be more expensive to ship if you order one online.
Pros and Cons
One piece toilets
Pros:
More durable;
Easier to clean;
Higher end look.
Cons:
More expensive;
Heavier.
Two piece toilets
Pros:
Less expensive;
More options for look/height.
Cons:
Less durable (more likely to break);
More complex installation;
Greater chance of a leak;
Lower end look.
What Exactly Do Smart Toilets Do?
Smart Toilets have revolutionized the bowel movement experience. Many people do not have the slightest idea what a smart toilet could offer other than the conventional experience. But the features and functionalities of the modern intelligent toilet might surprise you.
Smart toilets provide a completely touch-free and hygienic bathroom experience. They have automated systems that eliminate the need to ever open or close the lids. The toilet will water-rinse, clean and air dry you afterwards. It will also thorough-clean, sanitize and deodorize itself after use.
We have compiled a list of the most important and interesting functions smart toilets have to offer. If you want to find out more we invite you to keep on reading.
Smart toilets have sensors to detect your movement and will auto lift the lids once you approach them. The automatic lids will open upon anticipating your arrival with preheated seats ready for your descent. After having done your business you can walk away, and the lids will automatically shut.
Being a favorite feature in the industry, this alone might make it worth the money. This will at least avoid any future arguments with your significant other.
A pre-mist will wet the bowl when sitting down which prevents anything from sticking to it. It prevents any matter from adhering when the bowl is dry, and it helps to keep the bowl clean afterward for you to have less cleaning to do. It is 80% more effective than a dry bowl. It keeps everything clean without harsh chemicals.
During the winter months, freezing toilet seats are an unpleasant chill on the butt cheeks when sitting down.
Most smart toilet manufacturers have thought of this and have built-in automatic preheated seats. This feature eliminates the morning unpleasantness.
They also work together with the sensors that detect your movement. After having used the toilet for a few months the system will figure the most effective times to preheat the toilet seats.
Your device will certainly have an energy-saving mode like your smart TV which is only activated when in use. Most manufacturers also have built-in functions to fit your needs.
|
|
|
Bad Ignition Coil Symptoms: 5 Signs You May Need a Replacement |
Geschrieben von: bop14mo - 21.04.2022, 02:35 - Forum: Allgemein
- Keine Antworten
|
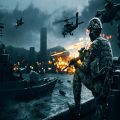 |
Bad Ignition Coil Symptoms: 5 Signs You May Need a Replacement
All cars have an ignition system with one or more ignition coils. Ignition coils are designed to convert the low-voltage from the battery into the high-voltage needed to fire the spark plugs.
Because ignition coils are such an integral part of the ignition system, they almost always cause noticeable symptoms when they fail.
Signs of a Bad Ignition Coil
Do you think your car might have a bad ignition coil? If you’re experiencing one or more of the following symptoms, you may be right.
Engine Misfire
Since ignition coils play a role in igniting the engine’s air-fuel mixture, a faulty coil can easily cause a misfire. A misfire happens when there’s incomplete combustion (or zero combustion) inside one or more of the engine’s cylinders.
The phenomenon will feel like a hesitation or shaking when the car is running. You may notice the problem intensifies when the engine is under a heavy load (e.g., accelerating).
Illuminated Check Engine Light
On modern cars, a computer (often referred to as the powertrain control module), looks for problems that could potentially lead to an increase in vehicle emissions. One such problem is an engine misfire caused by a faulty coil. The PCM will usually detect the misfire—and possibly an issue with the coil’s electrical circuit—and turn on the check engine light.
Car Won’t Start
While most modern engines have one ignition coil per cylinder, older vehicles use a single coil to supply voltage to all of the spark plugs. If that lone coil fails, none of the cylinders will receive spark, resulting in a car that cranks but doesn’t start.
The Engine Stalls
Like most electrical devices, ignition coils can experience intermittent problems. When this happens, the engine may stall unexpectedly. Stalling mostly happens to engines with just one ignition coil.
Reduced Fuel Economy
A faulty ignition coil usually results in an engine that misfires and runs poorly, leading to a reduction in fuel economy.
What Does an Ignition Coil Do?
An ignition coil is a transformer that converts battery voltage into the tens of thousands of volts needed to fire the spark plugs. Ignition coil operation is based on a phenomenon called electromagnetic induction—a process that uses a magnetic field to generate electrical current.
Inside the coil, there are two sets of windings. The so-called primary windings contain a hundred or so coils of wire, whereas the secondary windings have thousands of coils of wire.
When the ignition coil is energized, battery voltage flows through the primary windings, creating a magnetic field. Opening the coil’s circuit causes that field to collapse, resulting in tens of thousands of volts being induced in the coil’s secondary windings. The high voltage from the secondary windings then travels from the coil to the rest of the ignition system.
It’s important to note that there are different types of ignition coils. Older vehicles have a single ignition coil that’s connected to a distributor via an ignition wire. High-voltage travels from the coil to the distributor, which, in turn, distributes that voltage to the individual spark plugs and wires.
Newer vehicles use either coil-on-plug (COP) ignition coils or coil packs. Engines with a COP ignition system have one ignition coil per cylinder. Each coil sits directly on top of a spark plug.
Meanwhile, a coil pack is a group of ignition coils combined together in a single molded block. With this design, each cylinder gets its own ignition tower but shares its coil with a companion cylinder.
How to Test a Two-Stroke Engine's Ignition Module and Coil
The ignition coil or module for a two-stroke engine regulates the ignition power, and converts it to charging electricity for the battery system. When the module and coil begin to fail, it's typically because the units have been burned out. The result will be an engine that performs badly, if it starts at all. Testing such units involves using a few electrical tools to gauge if the part still works, since most modules and coils are sealed with no serviceable parts.
Step 1
Disconnect the spark plug cap from the spark plug. Carefully remove the plug wire to the ignition coil from its hooks that keep it in place on the engine. Pull the plug wire out of the coil where it inserts: It's typically just pushed-in onto a spike in the coil.
Step 2
Use a screwdriver to disconnect the coil unit from its harness, or bracket on the engine. Put the securing screws aside. Carefully pull the coil off the bracket, and then carefully disconnect the engine and vehicle wires from the coil itself.
Step 3
Attach the ends of a multimeter to the coil connections for input and to ground, testing electrical resistance in the unit. Replace the coil unit with a new one, if the reading shows as infinity or zero. This means that there is no resistance the unit is burned out.
Take the good unit, or a new coil and reconnect it to the engine bracket. Insert a new length of spark plug wire, after connecting the spark plug cap to one end. Insert the other end into the coil receptacle for the wire. Reconnect the spark plug cap to the spark plug.
Ignition Coil: Basic Principles
The design of a conventional ignition coil is basically similar to that of a transformer. The ignition coil's task is to induce a high voltage from a low voltage. Alongside the iron core, the main components are the primary winding, the secondary winding, and the electrical connections.
The laminated iron core has the task of amplifying the magnetic field. A thin secondary winding is placed around this iron core. This is made of insulated copper wire about 0.05-0.1 mm thick, wound around up to 50,000 times. The primary winding is made of coated copper wire about 0.6-0.9 mm thick, and is wound over the secondary winding. The ohmic resistance of the coil is around 0.2–3.0 Ω on the primary side and around 5–20 kΩ on the secondary side. The winding ratio of primary to secondary winding is 1:100. The technical structure may vary depending on the ignition coil's area of application. In the case of a conventional cylinder ignition coil, the electrical connections are designated as terminal 15 (voltage supply), terminal 1 (contact breaker), and terminal 4 (high-voltage connection).
The primary winding is connected to the secondary winding via a common winding connection to terminal 1. This common connection is known as the "economy circuit," and is used to simplify coil production. The primary current flowing through the primary winding is switched on and off via the contact breaker. The amount of current flowing is determined by the coil's resistance and the voltage applied at terminal 15. The very fast current direction caused by the contact breaker changes the magnetic field in the coil and induces a voltage pulse, which is transformed into a high-voltage pulse by the secondary winding. This passes through the ignition cable to the spark plug's spark gap and ignites the fuel-air mixture in a gasoline engine.
The amount of high voltage induced depends on the speed of change in the magnetic field, the number of windings on the secondary coil, and the strength of the magnetic field. The opening induction voltage of the primary winding is between 300 and 400 V. The high voltage on the secondary coil can be up to 40 kV, depending on the ignition coil.
How to Tell if You Have a Faulty Coil Pack
On newer vehicles, a coil pack replaces the distributor. It is an electronically controlled pack of ignition coils regulated by the car's computer and is used to create the spark for each engine cylinder's spark plug. Generally speaking, coil packs are much more reliable than distributors, because there are no moving parts and because they fire much less often than a distributor. Coil packs usually create a better spark, which in turn produces better combustion and horsepower in a car's engine.
How a Coil Pack Works
When creating a spark at the spark plug, the fire must initiate from a high voltage supply, so as much fuel as possible burns in the cylinder. Whenever the combustion process is started, the coil pack builds up the energy, as much as 50,000 to 75,000 Volts. When the electronic control module (the car computer) sends the signal to the ignition control, the voltage is released from the coil pack through the spark plug cables to the spark plug.
When the spark travels to the spark plug, it jumps from the spark plug gap to the ground, causing an explosion of the fuel air mixture inside the cylinder chamber.
Coil Pack Problems
Usually, if a coil pack is bad, there will be a loss of fire or spark in one or more cylinders. This causes what's commonly referred to as misfiring. Misfiring can cause drag on the crankshaft, and usually results in a very poor performing engine.
Common Symptoms of a Faulty Coil Pack
A faulty coil pack will generally have symptoms similar to a faulty spark plug. Some of the most common tell tale signs that a coil may be defective include:
A rough idle
An unexplainably louder-than-usual engine
A noticeable lack of power
A significant drop in RPMs while accelerating for no apparent reason
A blinking or intermittently activating check engine light
An active gas warning light when the vehicle has plenty of gasoline
Smoke from the exhaust emitting intermittently, instead of in a steady stream
What Coil Pack Works with a Rotary Engine?
Most rotary engines require a different type of ignition coil pack. Below are two, one for a standard replacement, and one that is a higher voltage performance type coil pack.
Original Equipment Replacement
Beck Arnley is a well known name in the automotive ignition parts industry. They are favored by many mechanics, especially those that work mostly on import cars. The Beck Arnley 178-8025 rotary engine coil pack is a direct replacement for original equipment parts on older Mazda cars with a rotary engine. You can expect to pay about $55 for one.
Performance Replacement
M&W Ignition Systems is a fairly well known name in the import performance market. Their part number PAK005 is a high performance ignition coil pack for the performance enthusiast who isn't afraid to spend a little more on a high quality high performance part. With prices running around $245 for a double coil pack for direct fire ignitions, these coil packs will deliver years of excellent performance.
When ordering a coil pack for your rotary engine equipped car, you need to know the year and model as well as the engine displacement to ensure you are given the correct parts.
|
|
|
What's the Difference between a Start and a Run Capacitor? |
Geschrieben von: bop14mo - 21.04.2022, 02:31 - Forum: Allgemein
- Keine Antworten
|
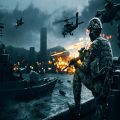 |
What's the Difference between a Start and a Run Capacitor?
Capacitors in General
A capacitor is an energy storing device. It is a medium by which energy is stored to either be released suddenly or over a period of time. The energy or capacitance of an electric capacitor is measured in the form of micro-farads. Essentially, two plates are separated by a material known as a dielectric or insulator. These insulators can be mica, ceramic, porcelain, Mylar, Teflon, glass, or rubber. Capacitors will also limit the current. They can be used to store voltage or build it up until the call for it to be released is present.
Start Capacitors
A start capacitor is found in the circuit of start windings when the motor is starting. This capacitor contains a higher capacitance than a run capacitor. It varies, but a start capacitor will measure between 70 and 120 micro Farads. The start capacitor provides an immediate electrical push to get the motor rotation started. Without a start capacitor when the voltage is applied, the motor would just hum. The start capacitor creates a current to voltage lag in the separate start windings of the motor. The current builds up slowly, and the armature has an opportunity to begin rotating with the field of current.
Run Capacitors
A run capacitor uses the charge in the dielectric to boost the current which provides power to the motor. It is used to maintain a charge. In AC units, there are dual run capacitors. One capacitor provides power to the fan motor. The other sends power to the compressor. Run capacitors measure in at approximately 7-9 micro-Farads. The value or rating of the run capacitor must be accurate. If the value is too high, the phase shift will be less than perfect and the winding current will be too high. If the capacitor value/rating is too low, the phase shift will be higher and the winding current will be too low. If run capacitors are not ideal, then the motor could overheat and the true torque will not be enough to drive current.
What is Equivalent Series Resistance?
The equivalent series resistance of a capacitor is the internal resistance that appears in series with the capacitance of the device. Almost all capacitors exhibit this property at varying degrees depending on the construction, dielectric materials, quality, and reliability of the capacitor. The equivalent series resistance (ESR) values range from a few milliohms to several ohms, and results into power losses, reduced efficiency, and instability of power supplies and regulators circuits.
Image source
The aluminum electrolytic capacitors and tantalum ones, have higher ESRs than ceramic capacitors of the same capacitance and voltage rating. The polypropylene and polyester capacitors fall in between, but are not commonly used in the SMPSs due to their large physical sizes.
Main parts of an ESR
Metallic resistance
Electrolytic and paper resistance which is dependent on frequency and temperature
Dielectric which depends on frequency
Factors that increase the ESR value
Bad electrical connections; – The connection between the copper leads and the aluminum plates in the capacitor are usually welded or made using mechanical crimps. This type of connections introduces some series resistance, and is used because the aluminum cannot be soldered.
The drying of capacitor electrolyte solution. As the liquid component of the electrolyte dries out due to elevated temperatures, the electrical resistance increases.
ESR increases with increase in temperature and frequency. In power supplies with high currents, the power dissipation associated with the ESR may further increase the temperature and lead to capacitor failure.
Minimizing ESR in circuits
High performance applications use the low ESR capacitors such as the low ESR solid polymer capacitors, tantalum capacitors and the multilayer ceramic capacitors (MLCC).
Capacitors are connected in parallel in places such as the power supply smoothing circuits. Small value capacitors are connected in parallel as opposed to connecting a single large capacitor. This reduces the effective ESR in addition to reducing the ripple volatge, and allows the circuit to handle higher currents with less losses.
What is the Start Capacitor for a Bore Pump Motor?
A capacitor is a an electronic device that stores energy. In a single phase bore pump a start capacitor increases the starting torque for a short while and then brings the motor rotation up to a rate approaching the speed at which it will run the pump constantly. The bore start capacitor then drops out and a run capacitor takes over for energy efficient running of the pump.
In most submersible pumps the capacitor is a dual start/run capacitor that does both. A capacitor used with a bore pump motor is normally perfectly cylindrical and about half the diameter of a soft drink can. It should not have black marks or be ruptured.
With a typical Perth submersible bore pump the capacitor, or condenser as it is sometimes referred to, is normally in a bore start box often mounted near the homes meter box. Remember bore start boxes are 240 volt and should only be accessed by a licensed electrician. We provide a fast mobile service all over Perth to replace burnt or blown bore pump capacitors.
The submersible pumps with start boxes are known as “3 wire” motors (the wiring to the surface is 3 core and earth). Some submersible motors known as “2 wire” have the electronics and capacitor in the actual pump motor below ground and have 2 wires and an earth running up to the surface. 2 wire pump motors therefore do not have start boxes or easily replaceable start capacitors “3 wire” submersible motors are more common in Perth bores.
Why Are Capacitor Discharge Resistors Now Mandated As Essential Safety Device
In Electronics, Capacitor discharge resistors or Bleeder resistors are resistors connected in parallel with the output of a high voltage power supply circuit with the express purpose of discharging the residual electric charge stored in the filter capacitors of the power supply.
As an example, a switch mode power supply uses a bridge rectifier to convert AC Mains Power into DC at 320V (where the mains voltage is 220/240V) or 160V (where the mains voltage is 110/120V), before the voltage is reduced by the chopper. One or more Filter capacitors are incorporated to smooth the pulsating output voltage from the rectifier. Now these capacitors must necessarily store enough energy at this high voltage to power the load during the Zero crossings of the AC input.
Further, the capacitors chosen in many power supplies are designed to be large enough to supply the load during Power breakdowns lasting for a second or so.
This stored charge is often enough to deliver a lethal shock in devices such as Lasers, X-Ray machines, Radio transmitters and also the old style CRT screens.
It is most important that it must be recognized that this stored charge can remain in the capacitors for a significant period of time even after the unit has been turned off, and therefore poses a life threatening hazard for the user or maintenance personnel who may believe that because the device is turned off it is safe.
To meet the challenge of this safety hazard, it is necessary to discharge the capacitors after the power has been turned off and typically a large or high resistance value resistor is connected across the terminals of the capacitor.
So after the device is switched off, the charge on the capacitor will drain off through this Capacitor Discharge or Bleeder Resistor, thus rendering the device safe for servicing etc.
It is pertinent to note that when the device is ‘ON’ a small current flows through Capacitor Discharge/Bleeder resistor which results in the wastage of a small amount of power.
In order to reduce this power wastage it is necessary for the designer to select, an optimum resistance value due to the fact that there is a trade off between the speed at which the capacitor can be drained off and the wastage of power during normal operation.
The lower the resistance value of the Capacitor Discharge /Bleeder Resistor, the faster the bleed down rate but wastage of more power during normal operations and vice verse for a higher resistance value.
To meet this need, HTR provides a Capacitor Discharge/Bleeder Resistor which is so designed that the resistor can be mounted directly to the capacitors terminals and not through any connectors, thus eliminating the risk of the Bleeder resistor being disconnected accidentally.
Reactive power of capacitors
The current flowing through capacitors is leading the voltage by 90°. The corresponding current vector is then in opposition to the current vector of inductive loads. This why capacitors are commonly used in the electrical systems, in order to compensate the reactive power absorbed by inductive loads such as motors.
Inductive-reactive power is conventionally positive (absorbed by an inductive load), while capacitive-reactive power is negative (supplied by a capacitive load).
As reactive-inductive loads and line reactance are responsible for voltage drops, reactive-capacitive currents have the reverse effect on voltage levels and produce voltage-rises in power systems.
|
|
|
A Guide to Bone China |
Geschrieben von: bop14mo - 21.04.2022, 02:29 - Forum: Allgemein
- Keine Antworten
|
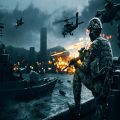 |
A Guide to Bone China
Bone china is considered to be the most refined and luxurious of tableware materials, adding sophisticated classical and contemporary design to any table - whether during breakfast, lunch or dinner.
If you're in the market for purchasing bone china tableware, the Wedgwood Guide to Bone China will answer some common questions regarding this beautiful material, as well as providing guidance on how to choose and care for your bone china tableware.
Bone china is a durable, lightweight and elegant material that is most commonly used for the creation of tableware and teaware such as plates, bowls, mugs and teacups. Bone china is made from china clay, china stone and bone ash (made from animal bones).
To create bone china, either china clay, china stone, bone ash, or a combination of the three is combined with porcelain clay and fired at a slightly lower temperature than porcelain. This produces a light, delicate material with a milky, almost translucent appearance.
Investing in bone china tableware comes with many benefits for your at-home eating experience. Bone china is the strongest material of the porcelain and china ceramics, meaning that it is likely to last through everyday use and the usual accidental slips of the hand or knocks off the table. Bone china is a luxurious and precious material, so will last for decades and can have amazing sentimental value when passed down through generations. It brings a perception of elegance and sophisticated taste to dining at home, making every day a special occasion!
Bone china is considered to be the highest quality ceramic used for tableware, and is perfect for both everyday use and special occasions due to the fact that it’s strong, durable, mostly chip-resistant, and stunningly beautiful.
For an interesting fact, the durability of bone china is actually based on the percentage of bone ash content present within the product. The traditional formulation for bone china is about 25% kaolin, 25% Cornish stone and 50% bone ash. The industry minimum for bone content is 30% or higher.
Is bone china microwave safe? Yes! In fact, it’s microwave safe, dishwasher safe and oven safe.
Here are some tips for washing your tableware set:
Wash dishes straight away to remove any acidic or sticky food residue.
When handwashing, wash each dish individually using a mild liquid detergent and a non-abrasive cloth. Having a plastic tuc in the sink is also a good idea, as it will protect the china from the harsh stainless steel of the sink.
If using a dishwasher, take care not to overload the rack, and keep metal items away from your fine bone china - even light contact can scratch, chip or crack your dishes.
Here are some tips for keeping your Wedgwood china in stunning condition:
Soak your pieces in white vinegar for three minutes before rinsing and towel drying them to remove hard water spots.
Remove coffee stains from mugs (as well as fork marks from plates) by rubbing a paste of baking soda and water over the tableware before rinsing and drying.
To prevent scratching and chipping your fine bone china tableware set, put it in a fabric storage case, or put segments of fabric, tissue paper or napkins between each piece when stacking.
What Exactly is Bone China?
There's something quite elegant and magical about drinking a cup of tea from real bone china.
This popular British belief is apparently true, bone china does make the tea taste better and there are many reasons for this. Bone china doesn’t absorb any of the tea aromas and flavours like other ceramics do and therefore providing a full-on tea tasting experience. The thinner and lighter bone china material adds a very dainty and classy feel. While the creamy-white translucent colour of the china perfectly compliments the hue of tea liquor.
However, because of the possible unethical practices of using bone ash in bone china, some companies are choosing to add jade as an alternative.
Real bone china should not contain any lead, is non toxic and is safe to use. Bone china is made from porcelain, bone ash and kaolin (a type of clay).
Bone china is usually made from cow bones. Just as the name suggests, bone china contains animals parts and is not for everyone. It’s rare, however, some china has been found to contain human bone ash! In the past, a loved one’s ashes could be added to china for a keepsake.
What is a Promotional Bone China Mug?
In the ceramic family, there are quite a number of categories. Each as important, if not better than the last creation. Some of the popular categories include stoneware, pottery, earthenware as well as bone china. Presently, bone china mugs are part of the most sought after collectables. Although still manufactured in bulk and available for daily use, bone china can be beautiful and fragile, befitting use as a decorative piece. Bone china creations are readily available in an array of versatile, befitting designs that are ready for consumer selection.
Since bone china mugs are dishwasher and microwave safe, they are an excellent for hosting and home use. They can actually be used in bulk and stocked on top of each other to be washed or used at a later date, without the fear of breaking. This feature makes the bone mug wonderfully practical and a joy to have in the home.
Since bone china mugs are dishwasher and microwave safe, they are an excellent for hosting and home use. They can actually be used in bulk and stocked on top of each other to be washed or used at a later date, without the fear of breaking. This feature makes the bone mug wonderfully practical and a joy to have in the home.
In the market, there is a wide selection to pick and choose from. There are contemporary and classic bone china designs that come with every imaginable design from wavy patterns to abstract art. Made out of a soft combination of kaolin (25%), bone ash, (50%) and feldspathic material (25%), bone china is a soft-paste kind of porcelain. Given that is contains calculated calcium phosphate as well as a significant percentage of animal bone in the form of phosphate, bone china is one of the strongest porcelains ever invented. Similar to stoneware, bone china is made up of different mineral items. Hence it tends to be vitrified as a result of these highly different mineral properties. Bone china is produced in the same likeness as porcelain. One of the unique qualities behind bone china mugs is the fact that bone ash is actually taken from cattle bones that are vetoed for the lowest quantities of iron. Prior to undergoing de-gelatinisation, the cattle bones are crushed and then calcined at temperatures of up to 1250°C. Such high temperatures burn everything and result in bone ash.
The benefits of using porcelain tableware
For millions of years, porcelains have been used to create decorative kitchenware.
In the ceramics family, porcelain is the supreme material. Porcelain was first invented in China and has informally come to be known as “china” or “fine china”.
The finer the china, the more expensive the product becomes. The properties of porcelain such as strength, elasticity, permeability and translucency has made porcelain a very durable kitchenware and a complete value of money. Other than these, they are also popular and a good choice to make because of the following reasons:
Related: Differences Between Stoneware, Earthenware, And Porcelain
1. Heat Resistant
Porcelain is an excellent and very practical material for microwave or oven dishes because it distributes the heat through the elements evenly. The heat resistant nature of porcelain can be proven by it being fired at very high temperature during its creation. Porcelain is suitable for use in ovens, microwaves and freezers.
2. Durable
Despite its fragile appearance, Porcelain is one of the strongest and most durable dinnerwares you should consider getting. Dinnerware made of Porcelain is durable and nonporous due to it being fired at a very high temperature during its creation.
3. Non-Stick & Easy To Clean
Due to its fine smooth glassy texture, porcelain provides users with ease during plating and cleaning after dinner. With just water and dish soap you can get grease stains off instantly.
4. Versatile
Porcelain tableware come in different colours, shapes and sizes. Making it suitable for any events and occasions. You can experiment and play around with different colours and see how it matches the theme of the meal.
5. Huge Selection Options & Affordable
Porcelain tableware is a great buy as comes in different variations of colours, shapes and sizes. Porcelain allows you to get a bang for your buck with the ability to explore different dining styles with a limited budget. You can aim for a classy style or maybe get some colours on your dining table.
Give your kitchen a makeover by using porcelain kitchen wares that not only give you a visually pleasing appearance but also these numerous benefits that we have talked about.
What are the differences between porcelain and stoneware?
When it comes to choosing the best material for your dinnerware, bakeware and cookware, the choices offered in the market are multiple. There is all the family of ceramics (earthenware, stoneware, porcelain and bone china) but also glass, melamine or plastic.
To answer the question, we will focus on only the ceramic made dinnerware. To understand the pros and cons of each material, we will study each one of them and gather key things to know about each material so we can understand the differences between porcelain and stoneware and bone china.When it comes to choosing the best material for your dinnerware, bakeware and cookware, the choices offered in the market are multiple. There is all the family of ceramics (earthenware, stoneware, porcelain and bone china) but also glass, melamine or plastic.
To answer the question, we will focus on only the ceramic made dinnerware. To understand the pros and cons of each material, we will study each one of them and gather key things to know about each material so we can understand the differences between porcelain and stoneware and bone china.
Stoneware vs Porcelain when it comes to baking
Avoid using bone chine for warming: when it comes to heating and baking, the choice is really only between Stoneware and Porcelain.
A few facts:
Heating and cooking: as a general rule, avoid the sudden temperature changes (from the fridge, to the oven, to the dishwasher). Both stoneware and porcelain should not be placed on direct heat EXCEPT the range of cookware by REVOL: REVOLUTION (also compatible on induction and electric heat). Both stoneware and porcelain can be used in the microwave.
Cleaning: usually both materials are dishwasher safe
Baking: porcelain being non porous – porcelain dishes are a great options to bake! The heat distributes evenly and the baking will be perfect. Also, glazed porcelain is naturally non stick. So you will enjoy baking with a baker made of porcelain. Like for the Belle cuisine collection: these bakers will bake anything evenly and will make every recipe delicious and easy to make.
|
|
|
Factors to Consider When Buying a Money Counting Machine |
Geschrieben von: bop14mo - 21.04.2022, 02:24 - Forum: Allgemein
- Keine Antworten
|
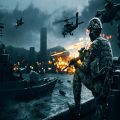 |
Factors to Consider When Buying a Money Counting Machine
A money counting machine is one of the most useful tools you can have. They can drastically reduce counting errors and help to ensure that your accounts are accurate. They can save you time. because they count money much faster than a flesh-and-blood money counter. But counting isn't all they do.
Money counting machines can also detect counterfeit bills, and they can do so much more accurately than we can. They can incorporate technology that makes the counterfeit detection process much more reliable and quicker.
When shopping for a money counting machine, there are a few things to look for. Price and functionality are among the most important factors to consider. You need a money counter that does all the things you need it to do, and nothing more. So, you're looking to avoid both over and under functionality, all without spending too much money.
Since a cash counter is supposed to make your life easier, it should be easy to use. You'll need to choose between manual and automatic, and you'll want to consider hopper capacity, as well. Not all money counters have counterfeit detection capabilities, so you'll have to decide if that's a feature you want. Finally, you'll need to consider whether or not you want to have mixed-denomination value detection.
Price and Functionality
We'll start with functionality. As with any other gadget you can buy, there are all kinds of features that can be included in a money counter, but the actual need for many of these features is questionable, to say the least.
Instead of being wowed by features, focus on just what you need. A large supermarket has need of more features than a small business. If you run a small business or any business in which all of the cash will be placed in a register, a basic bill counter may be all you need.
These bill counters do not sense denomination value, they just count the number of bills and scan them with counterfeit detection technology. Since the money is coming out of cash registers, it is already sorted by denomination, which makes a basic cash counting machine perfectly suited to your needs. Bill counting can be time consuming, and this machine will save you a lot of time.
Ease of Use
A money counting machine should be as easy as possible to use. As with price, the difficulty increases with each additional feature. A simple bill counter can be as easy as putting the bills in the hopper and turning the counter on.
Even though the difficulty of use increases with each added feature, more complex money counters can and should be easy to use. In fact, the only additional steps there should be are, at most, a few buttons to push before the machine starts to count. This should amount to telling the machine which currency is being used or how you want the bills sorted.
How Do Counterfeit Detectors Work?
A counterfeit money detector can come in many forms, but in its essence, it’s a machine that detects the security features of bank notes in order to determine whether any given bill is counterfeit or genuine. It uses one or several different methods of detection to verify bank notes through their security features. Some of these methods include UV, watermark, and metal thread detection. The more methods of detection that are used, the more accurate the machine will be as it is able to verify more security features.
UV Counterfeit Detection
UV is the most commonly used counterfeit detection method—it is seen in most of the lower-end devices with the lowest price points. A UV detector verifies the UV marks on authentic notes by shining ultraviolet light onto the bills. These UV marks are created through the use of non-visible dyes that are only visible under UV light. If the UV printed images glow when subjected to the UV light, then the bank note is expected to be authentic.
Magnetic Counterfeit Detection
Some counterfeit money detectors also use magnetic detection to identify the magnetic ink and metal threads placed on strategic areas of bank notes. This is also a common type of counterfeit detection.
Watermark Counterfeit Detection
In addition, some detectors will also use light to view watermarks that are built into authentic bank notes. These watermarks cannot be seen by the naked eye.
Benefits of a Coin Counter
A coin counter could revolutionize the way you handle cash in your business, and free up your valuable time. Here are the top five benefits you'll get to look forward to when you invest in a coin counter.
1. Save Time for the Things That Matter
You may still need to sort your nickels and your dimes, but once you've done so, it's time to let the coin counter spring into action. The machine effortlessly counts coins of the same denomination, and it will finish the tallying before anyone else on your team can do it.
Simply set a target amount and let the counter get to work. The machine will stop when it hits the target, and you can add more coins to keep the process rolling. The counter will also give you a running total as it counts up your coins.
While you leave the machine to do its sums, you and your team can tend to other tasks in the business. Maybe that means those to-do list tasks that keep hanging around and hanging around finally get crossed off the list. It might mean you can spend more time helping that one last customer or tidying up so you're ready for opening tomorrow.
2. Improve Your Accuracy
To err is human, or so the old saying goes. If you're still letting your team count up coins manually, you know this to be all too true. It may not happen every day, but the more time you spend counting coins, the more likely a mistake is.
The bigger problem is that it takes time to sort out those mistakes. One small error can multiply into much more wasted time as you try to spot the error and correct it.
A coin counter can solve this problem. The machine is more accurate than your human team can ever be, which means fewer mistakes and less wasted time.
3. Decrease Costs and Losses
Coin counting mistakes cost you more than time. They cost you money too. All that change adds up to a bigger problem in your books. Now multiply that loss over a week or a year.
Your new coin counter is far superior to anything humans can do, so you don't have to worry about losing out on your hard-earned cash.
4. Keep Your Hands Clean
It's no secret that cash is dirty. Coins are passed from hand to hand, and they've likely touched a lot of filthy surfaces before dropping into your till. Keep your employees' hands clean and germ-free by letting the machine handle the coins.
Shortchanged: How accurate are automatic coin counting machines?
Loose change can be all over the house and a nuisance. But at Coinstar machines, you dump your coins in and they give you cash back, charging a 10.9 percent processing fee on your total.
You expect 100 percent accuracy for what you put in and we wanted to hold them to it. So, we took coins of all denominations to ten coin counting machines. Our first stop was to the Coinstar machine inside the Kroger on Jackman Road. We brought in $25 in coins and counted it twice for accuracy. The cash used included 70 quarters, 50 dimes, 40 nickels, and 50 pennies. As it counted our coins, our cash back kept going up. The processing fee took out $2.72, so we should have received a cash voucher for $22.28. That's exactly what we received.
Next was the Coinstar in the Kroger at Monroe and Secor. It was also accurate.
But at the Coinstar in the Walmart on West Central Avenue in Sylvania Township, what happened there was very surprising. As the coins went in, we noticed something was wrong. We didn't get back what we put in, even with that processing fee already taken out.
After leaving the store and the Coinstar machine, we took a look at what we got back. It was only $20.05. We were definitely shortchanged by that machine, losing credit for several of our quarters.
We put in 70 quarters. One was rightfully rejected because it was a Canadian quarter. But instead of getting credit for 69 quarters, we only got credit for 59. We were shortchanged $2.50.
But the errors didn't end there. We got credit for 51 dimes, when we only put in 50, and 43 nickels when we put in only 40. We gained some back, but in the end, were shortchanged by the machine by $2.25.
Mike Klear is an inspector and the manager of Lucas County's Department of Weights and Measures. He told us the state does not give counties the authority to regulate Coinstar machines.
"Do I think they should be tested? Yes, I do believe they should be tested. Currently, they are tested by the company themselves, but they should have an entity watching how they test," Klear said.
When we put coins in the Coinstar in the Walmart in Perrysburg, the machine got backed up. It ended our transaction, with coins left on the tray. We combined the total with a second transaction and got credit for 49 pennies instead of 50. This was not a big deal at all, but we were still shortchanged.
We wanted Coinstar's response. A spokesperson told us:
"Our goal at Coinstar is to provide consumers with a convenient, reliable and accurate coin counting solution. With 25 years in business, processing more than 1 billion transactions, we have a zero tolerance policy on our accuracy tests; if a kiosk doesn't meet our standards, it's shut down and fixed."
Benefits Of A Massage Gun
A massage gun is known to offer the same results as a deep tissue massage. The beauty of this is that you can get all the benefits within minutes in your most convenient time while following your schedule. It makes it easier for most people to manage their health, whether they are in sports or they are just fitness lovers.
These massage guns have been in high demand in recent years, which can only be traced to the many benefits they have to offer, from relieving aches and pain to increased blood circulation among others. Worthy of note is that it also helps shorten recovery time while it does all of these.
1. Sports Performance, Injury Prevention, and Recovery
Percussive massage provided by a massage gun helps improve the muscle contraction, which results in the lengthening and strengthening of the muscles and fascial tissues. Making massage therapy part of your lifestyle and post-workout routine is a great way to relieve stress. The main purpose of a massage is to help relax the muscles and relieve tension in the body, which would help shorten the muscle recovery time between workouts, as toxic debris are constantly being eliminated to allow the muscles bounce back within the shortest possible time.
For every deep tissue massage with the massage guns, fluids and tension are released within the deep muscles and this results in improved circulation, as the blood and tissue cells exchange substances which help boost tissue metabolism. The supply of nutrients and oxygen is also improved due to the massage, therefore increasing blood circulation throughout the body. It also helps prevent overtraining due to the sedating effect it has on the nervous system. It heals and prevents injuries, as the improved circulation helps break down adhesions and the increased production of nutrients and fluids could help with quick tissue repair.
Sports performance is also improved, as the massage guns help increase power and performance, which makes the muscles more flexible and efficient.
2. Advanced Vibrational Healing & Powerful Pain Relief
Vibrational healing is a form of healing that is based on vibrations and subtle energies, without any dependence on other systems of healing. It is based on each person’s unique energy field and is known to be efficient. Interestingly, a massage gun provides this same benefit, as it delivers vibrations deep into the muscle by using the “percussive therapy” technique. The vibrations from the massage help improve blood and lymph circulation around the body, which helps produce more oxygen and nutrients into the muscles. The result of this is speedy recovery, improved range of motion, pain relief and relieving muscle fatigue and soreness. Pain in the neck, shoulders and lower back can easily be relieved with the advanced vibrating effect from massage guns.
3. Rehabilitation
Massage is known to be one of the most effective forms of injury rehabilitation therapy, as it not only speeds up the recovery process but also prevents re-injury. Massage guns work as a supplement to the standard injury rehabilitation process and encourage healing and recovery of atrophied muscles due to trauma or disease. Improved circulation into the muscles and fascial tissues helps the injured areas to become more flexible and heal within a short time.
|
|
|
Rotational Moulding: The Process & Advantages |
Geschrieben von: bop14mo - 21.04.2022, 02:21 - Forum: Allgemein
- Keine Antworten
|
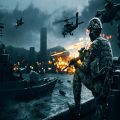 |
Rotational Moulding: The Process & Advantages
Rotational moulding, also known as rotomoulding, is a plastics moulding technology which is ideal for making hollow articles. It is a casting technic but unlike most other plastics processes there is no pressure involved. Moulds for the process are relatively inexpensive as they do not have to withstand pressure and therefore relatively short production runs can be made very economically.
Rotomoulding is used to make a very diverse range of products. The process offers the product designer exceptional freedom as just about any shape can be produced. There is almost no limit to the size of mouldings and there are literally thousands of applications.
The Process
The concept of rotational moulding is very simple. A plastic material, normally in powder form is placed into a hollow mould, usually made from cast aluminium or fabricated from sheet steel. The mould is closed and rotated slowly on two axis. The mould is then heated in an oven whilst rotating and the polymer gradually melts and ‘lays-up’ on the inside of the mould. Once the polymer powder has fully melted the mould is moved to a cooling station and cooled usually with air and sometimes a fine mist of water. As the mould cools the part solidifies. When the material has finally cooled sufficiently to release away from the mould surface the process is stopped and the product is taken out of the mould (de-moulded).
Whilst the concept of rotational moulding is extremely simple anyone who has ever been involved in the process will tell you that it is in fact extremely complicated. It is a casting process and there is normally no pressure involved which means that the material cannot be controlled in the same way as high pressure processes such as injection moulding. There are many variables that can affect production and the end product such as ambient temperature and humidity, type of mould, material specification and powder quality.
Materials
Today the industry is heavily dependent on Polyethylene (PE) and 97% of rotomoulded products are made from this material. Polyethylene is a versatile, easily mouldable and readily available polymer which has come to dominate the process. Rotomoulding is a casting technique in which powder is nearly always used rather than granules, meaning the material must be ground. Polyethylene is relatively easy to grind at ambient temperatures.
The development of other polymers has been hindered by the fact that the process is relatively long and therefore aggressive on polymers, however there is some usage of PVC (usually in liquid plastisol form), Polypropylene and Polyamide (PA6, PA11 & PA12). Many of these non-Polyethylene materials are difficult to grind and most need to be made into powder using cryogenic grinding – that is freeze grinding, which is a more costly process. There is a welcome increase in R&D to expand the range of materials available to the industry.
Uses And Advantages Of High-Quality Plastic Pulverizer Machine
When deliberating on high-quality pulverizer machines, take a look at the plastic pulverizer machine.
The plastic pulverizer is a piece of magnificent equipment used in crushing plastic into small and tiny sizes.
Former plastic pulverizers are highly difficult and complex and the results it produced are inaccurate sometimes.
To solve this problem customized powder pulverizer machines are introduced, and they generate colorful masterbatch.
All thanks to the manufacturer of the high-quality pulverizer. With this machine, you have the chance to achieve standard quality and colorful powder used in the manufacturing and compounding of masterbatch.
Also, the plastic pulverizer machines give the perfect and equal size of particles which ensures an adequate blending and mixing of additives.
Furthermore, plastic compounds such as Polycarbonate (PC), Polyamide (PA), and Polyethylene terephthalate (PET) are processed in an ambient heat through this processor.
Once this is ongoing, the downstream fan will transfer the end product into a cyclone from the disc mill.
One notable thing is that this whole process is totally mechanical but the control cabinet will maintain and regulate all the activities.
However, for advanced and latest high-quality pulverizer to smash your plastic materials, buy PVC pulverizer from a reliable manufacturer.
Obviously, this is the most recommended option for your best processing services.
Materials That Can Be Ground Using Plastic Pulverizer Machine
PVC pulverizer machine can be used to grind many items such as buckets, bottles, pipes, and jugs.
After grinding, these materials are converted into granules which are afterward ready to be remolded into different other products.
A plastic granulator is normally large which allows it to grind much plastic at once.
More so, you can also buy PVC pulverizer which is smaller in size for home use.
High quality plastic pulverizer machine can be used to grind thermoplastic materials such as Low-density polyethylene (LDPE) and ethylene vinyl alcohol (EVA).
Other materials include Polyvinyl Chloride (PVC), Polyester, cross-link, ABS, High-Density Polyethylene (HDPE), polyethylene terephthalate (PET), and Nylon.
When you buy PVC pulverizer, you can also use it to pulverize film waste, sheets, and tubes of soft and hard, impact, and brittle resistant materials.
High-quality pulverizer is easy to clean and maintain and has an economic option. It doesn't consume power and it has a robust design. In fact, time and effort are saved by its ease of operation.
Why You Should Go for an Air Cooler Over an Air Conditioner?
In the ongoing debate of air conditioners vs air coolers, we list down few important pointers that will offer a clear idea of why you should opt for an air cooler.
But first things first, should you buy an air cooler?
A cooler can be used by everyone, especially people living around hot and dry weather. One can choose from a dessert cooler, a window cooler or even a personal cooler, depending on the requirements.
Read on to know more about why to choose an air cooler over an air conditioner.
Have you ever wondered about how an AC or an air cooler functions and how does it affect the quality of air in your home?
An air conditioner circulates the internal air of the room over and over again, whereas an air cooler pulls fresh air from outside and then cools it down. Also, air cooler doesn’t make the air overly dry like an air conditioner. Because of the way it operates, an air cooler offers better quality of air for your room. So much so, that the air circulated from an air cooler is preferable for people with asthma or dust allergy.
Economical Alternative
When it comes to value for money, an air cooler definitely scores high over an AC. Even though both end up cooling the room, an AC can cost anything ranging from ₹30,000 to ₹60,000, whereas a cooler will be available from ₹5000 to ₹15,000. Also, apart from the initial cost of purchasing, even the operating cost of an air cooler is less than an AC. You can approximately expect 80% less electricity bill from a cooler as compared to an AC, making it economical in the long run.
Going green is something that concerns all of us, and air coolers trumps the card here as well. Air conditioners use CFC (Chlorofluorocarbon) and HFC (hydro-chlorofluorocarbons) as their refrigerant, which is quite harmful to the environment. On the other hand, air coolers are eco-friendlier, since they use water as the refrigerant.
Industrial Cooling Fans: Overview, Benefits, and Applications
It is quite common to see various types of fans in industrial facilities. They are used to regularize the airflow to various structures or parts of the building. There are several types of industrial fans, which are categorized based on their designs, applications, and so on. Industrial cooling fans and industrial cooling blowers are two types of industrial fans used across the industrial facility for cooling purposes. Do you want to know how these fans differ from other types?
This post gives an overview of industrial cooling fan, their beneficiary features, and industrial applications.
What are Industrial Cooling Fans?
Industrial fans are the mechanical devices that create fluid flow for industrial purposes. The industrial fans often considered as fluid displacers since the air or gas is displaced from one point to another due to the rotational motion of blades. The primary purpose of the industrial cooling fans is to blow cold air and drive hot air out of the environment. Therefore these industrial fans are also called industrial cooling blowers. However, cold air intake or hot air exhaust depends on the design and construction of the specific fan. Unlike other industrial fans, the cooling fans have large diameters, which help them produce large volumes of air and low pressures, as required in several environments. Regardless of the fan design, the fundamental components of industrial fan remain the same. They are discussed in detail in the next section.
Fundamental Components of an Industrial Cooling Fan Assembly
Industrial cooling fans comprise a motor, a rotor shaft, and the blades or impellers. These are the fundamental components of the assembly. Check out on the function of these fundamental components and other important features in a fan assembly.
Motor:
An electrical motor is the primary input source in an industrial cooling fan assembly. The motor can be AC or DC as per the design and performance requirements. The motor transfers’ electric power to the hub of the rotor shaft as the energy input.
Rotor Shaft:
The rotor shaft is connected to an electric motor with an intermediate hub. The hub transfers electrical energy to the rotor shaft. The shaft rotates on receiving this electrical energy. This all suggests the conversion of electrical energy into mechanical to get the desired output.
Impellers/Blades:
The blades or impellers are the components that cut through the surrounding air to form a fluid drag. The blades are mounted on the rotary shaft at a specific distance. The blades rotate to push or exhaust air drag. These blades can be designed in multiple shapes according to aerodynamic standards.
Fan Casing:
The fan casing is a metal casing that houses the whole assembly. The main purpose of fan casing is to protect the assembly from dust, external damage, as well as the environmental impact such as corrosion, moisture, dust, etc.
Fan Mountings:
The mountings are bearing on which the fans are fixed on. The industrial cooling fan assembly can be mounted by using a ball or sleeve bearings. The bearings are the foundation of the fan assembly therefore, the quality and function are very important.
These components of the industrial fan assembly remain constant irrespective of the types of industrial cooling fans.
|
|
|
Wpc Vs. Spc: What You Need To Know About Water-Resistant Vinyl Plank Flooring |
Geschrieben von: bop14mo - 21.04.2022, 02:16 - Forum: Allgemein
- Keine Antworten
|
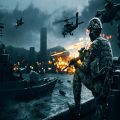 |
Wpc Vs. Spc: What You Need To Know About Water-Resistant Vinyl Plank Flooring
What Is Rigid Core Flooring?
Rigid core flooring is the innovative vinyl flooring for today's demanding consumers. Available in both plank and tile shapes, it's a luxury material that can stand up to a lot of abuse, including water.
To understand rigid core, you have to move beyond the vinyl flooring you're familiar with. Standard vinyl flooring is a fairly thin, flexible material that is glued down to the sub floor. Rigid core is stiffer, thicker and sturdier, which gives it some unique advantages. One of its most-hyped pluses is its ability to handle water, but that's not the only check in the “pro” column. It can also handle sub floor imperfections, offer excellent sound insulation and superior comfort underfoot.
Here's where we get to the technical jargon: The assorted positives of vinyl plank flooring (or vinyl tile) depend on whether you go with a WPC or SPC construction.
How WPC and SPC Come into Play
Like engineered hardwood, luxury vinyl plank flooring is constructed from layers of material—typically four, though that can vary between manufacturers. Let's look at the different layers, starting with the surface:
Layer #1 is the wear layer. It's clear, durable and scratch-resistant.
Layer #2 is the vinyl layer, composed of multiple, compressed layers of vinyl. This layer facilitates the authentic embossing technology applied to the printed decorative film that lies between the wear layer and this vinyl layer.
Layer #3 is the rigid core layer. It's made from either wood plastic composite (WPC) or stone plastic composite, also referred to as a solid polymer core (SPC).
Layer #4 is the base layer. This is the bottom of your plank or tile, and it's usually made from foam or cork.
Many WPC and SPC options also feature an attached pad (underlayment) that provides sound absorption and allows for under floor heating systems.
What Is WPC?
Wood plastic composite flooring, or WPC flooring, is a vinyl plank or vinyl tile flooring with a rigid core that's made from either recycled wood pulp and plastic or polymer composites that are expanded with air. It's sometimes called “wood polymer composite flooring.” It is a light weight, low density construction that is warm and soft underfoot with greater comfort.
What Is SPC?
Stone plastic composite, solid polymer core, or SPC flooring, is a vinyl flooring material that has a rigid core made from powdered limestone, polyvinyl chloride and stabilizers. Sometimes, you might see it referred to as “stone polymer composite flooring.” It is dense, dimensionally stable, quiet and strong. Pure from Beauflor are great options in this category and both include an attached pad.
SPC and WPC – Key Differences to Know
Similar to dryback luxury vinyl flooring (which is the traditional type of luxury vinyl that requires an adhesive to install), SPC and WPC flooring are comprised of multiple layers of backing that are fused together. However, unlike dryback flooring, both flooring options feature a rigid core and are a harder product all around.
Because SPC’s core layer is comprised of limestone, it has a higher density in comparison to WPC, though is thinner overall. This makes it more durable compared to WPC. Its high density offers better resistance from scratches or dents from heavy items or furniture being placed on top of it and makes it less susceptible to expansion in cases of extreme temperature change.
One important thing to note is that although SPC and WPC are often marketed as being waterproof, they are actually water resistant. Though neither product is entirely waterproof if submerged underwater, topical spills or moisture should not be an issue if properly cleaned in a reasonable amount of time.
Applications
Rigid core products including WPC and SPC were originally created for commercial markets because of their durability. However, homeowners have started using rigid core as well because of its ease of installation, design options and durability. It is important to note that some SPC and WPC products vary from commercial to light commercial use, so it is best to always consult your manufacturer to know which warranty applies.
Another highlight for both SPC and WPC, aside from their easy-to-install click locking system, is that they do not require extensive subfloor prep prior to installation. Though installing over a flat surface is always a good practice to be in, floor imperfections like cracks or divots are more easily hidden with SPC or WPC flooring due to their rigid core composition.
And, when it comes to comfort, WPC is generally more comfortable underfoot and less dense than SPC due to the foaming agent it is typically comprised of. Because of this, WPC is especially well suited for environments where employees or patrons are constantly on their feet.
In addition to offering more cushion when walking, the foaming agent in WPC provides more sound absorption than SPC flooring does, although many manufacturers offer an acoustic backing that can be added to SPC. WPC or SPC with acoustic backing are ideal for settings where noise reduction is key such as classrooms or office spaces.
What's the Difference Between Lvt Vs. Lvp?
LVT (Luxury Vinyl Tile) and LVP (Luxury Vinyl Plank) are two different types of luxury vinyl flooring. LVT is vinyl flooring designed in a tile shape, whereas LVP is vinyl flooring designed in planks to resemble traditional hardwood floor planks.
Here are some more details on these two wonderful luxury vinyl flooring choices…
What's Luxury Vinyl?
Luxury vinyl is a specific type of vinyl flooring. Old-school vinyl flooring used to be offered in sheet form only, and therefore wasn't able to mimic the realistic natural materials that luxury vinyl floors now can. Modern LVT and LVP floors are now offered in countless patterns and colors, and designed so that they appear to look almost exactly like natural materials such as wood, stone, and tile. Some LVT and LVP flooring options are even textured to appear like these materials as well. Many LVT and LVP floors even have seams for grout, and the planks can come in narrow or wide styles, as can the tiles.
Are LVT and LVP floors waterproof?
Yes! Both LVT and LVP floors constructed from layers of plastic, so they're waterproof, making them an ideal flooring choice for any room in your house, especially kitchens, bathrooms, and basements. LVT and LVP floors are designed to withstand moisture, heavy foot traffic, and plenty of scratches and spills.
What's VCT flooring then?
VCT stands for Vinyl Composite or Vinyl Composition Tile flooring. Though VCT floors are also made with some vinyl in them, unlike LVT floors, they contain less plastic and more natural materials such as limestone. Because of this, VCT floors are more porous than LVT floors, and thus they are not as waterproof and require more maintenance.
What about Engineered Vinyl flooring?
Engineered Vinyl flooring, or Engineered Vinyl Plank (EVP), is a subset of LVPs. EVPs are simply even more durable than many LVP options, as they're built with the strongest high-density fiberboard core, and have a rigid stone-based core. EVPs are often considered the luxury vinyl planks on the market that most closely resemble real hardwood floors, but personal preference will often determine this for you!
What Is The Most Durable Garage Floor Covering?
Whether you use your garage as a car parking area, laundry area, or home gym, you want a floor that sustains your uses. A durable garage floor is an asset because it saves costs on floor repairs. It also gives you the freedom to maximize garage usage. A floor that sustains high traffic, resists damage and offers easy cleaning is crucial. While most garage floor finishes are durable, not all may match your needs. With this list of garage floor coverings, you can find the perfect floor finish. The right floor covering transforms your boring garage into a modern, inviting space.
Epoxy is one of the most durable garage coatings. You can lay it on your concrete subfloor to liven up your garage. It provides unique colorful hues, metallic and natural stone finishes. Once dry, the epoxy forms a hardened and thick coating. This layer protects your floors from scratches, dents, chemical spills and cracks. No matter what you drop on your garage floor, the epoxy will resist damage.
The installation process may take 3-5 days or longer, depending on the floor size. You need to find alternative parking, but it's worth the wait. A professionally installed epoxy floor serves you for 5-10 years. However, it may last longer, depending on usage. For instance, commercial garage flooring wears faster than a private garage at home.
An epoxy floor expert prepares your floor before applying at least three coats. The preparation and layers provide the best durability. The primer is the first layer, followed by the base coat and, finally, the topcoat. As you can imagine, the finished coat is thick and hard enough to resist impact and chemicals. The base coat lets you play around with colors and designs. Lastly, the final coat gives you a smooth glossy finish.
Epoxy is also great for commercial garage flooring because it resists wear. You can park cars and walk over the years. With a non-slip additive, the floors resist slipping to prevent injuries. The thick coating also seals cracks and imperfections. You can enjoy a durable and smooth floor finish
Purpose of Skirting
Skirting in some projects is an aspect of beautification and for some, it’s a method to hide the unwanted features in the interior walls. These skirting boards were known as mop boards as they protect the wall from water when the floor was mopped. Different purposes for which skirting are installed are mentioned below:
- Hide exposed electrical wiring: Skirting can be used to cover up the exposed electrical wires and connection that cannot be removed. Hiding these wiring under the skirting board is found more economical and practical compared to hiding under the ceiling board.
- Cover the gap between the walls and floors: Some construction flops may result in unwanted gaps between the wall and the floor. Redoing such works is time-consuming and costly. One alternative is to install skirting so that the poor work is covered and cleared economically.
- Avoids marks from furniture: The skirting board installed has a projection that always keeps a gap between the nearby furniture and the interior wall. This way rubbing and scratching from the furniture are avoided letting the wall free of scratches.
- Improve Interior: A matched and good colored skirting gives the room a finished and cleaner look. Skirting throws a professional touch to the room it is installed.
|
|
|
Linear Bearings: What You Need to Know |
Geschrieben von: bop13mo - 20.04.2022, 02:55 - Forum: News
- Keine Antworten
|
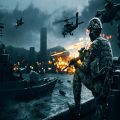 |
Linear Bearings: What You Need to Know
Linear bearings are rolling-element and fluid-film devices that reduce friction in motion systems where the motion acts along a straight — or sometimes curved — pathway. They are distinguished from radial bearings in which motion is rotary. Linear bearings are used in machine tool applications such as sliding doors, 3D printers, and automation settings where reducing friction and guiding linear motion is needed. They can be loosely grouped as ball and roller types that use the rolling motion of rolling elements and sliding types that rely on lubricant and low-friction surfaces. This article will discuss the distinct forms that linear bearings take and highlight some general applications.
SLIDE-TYPE BEARINGS
Sometimes called linear bushings, linear bearings are manufactured in sintered aluminum bronze, metal/polymer composites, carbon insert styles, polymer-lined sleeves, etc. and rely on a lubricating film to form between the bearing and the shaft while the two are in relative motion. Powdered-metal bronze bushings have been used for many years as die-post bushings. Their porous constructions, often with carbon plug inserts, are vacuum impregnated with oil that flows to and from the bearing under the frictional heat developed as the shaft moves and stops, providing a film of oil between the bearing and the shaft.
Polymer, self-lubricating linear bushings have captured some of the market that had been dominated by sintered metal bushings. The polymer itself — typically PTFE — provides slipperiness for the running shaft. These are popular in food packaging for their ability to run without lubricants and their ability to withstand washdown chemicals. They can run on unhardened shafts having high corrosion resistance. Because polymers are subject to cold flow at high loads and do not dissipate heat well, polymer is often bonded in thin sections to metal backers in the construction of these bearings.
Linear bushings can be crowned slightly to permit some angular adjustment of the bushing relative to the housing to adapt to shaft deflection. In more extreme cases, the bushing is supported in the housing by O-rings. Linear bushings are available as naked units or housed in pillow blocks and flanged units.
Bushings can be arranged as tandem installations in common housings to provide higher axial spread for the bearing surfaces. They are available as open and closed varieties, with the selection depending on how the shaft is supported. Shafts supported continuously over their lengths require open bushings that can clear the rod rails. Shafts supported on their ends can use closed bushings. Linear bushings are tolerant of dirt as a result of having no moving elements.
What Is a Rod End Bearing?
A rod end bearing is a common type of mechanical joint used on the ends of control rods. The steering columns in most cars, trucks and other vehicles, for example, feature tie rods with a rod end bearing. Of course, tie rods are designed to connect a vehicle’s steering rack to its steering knuckle. As a result, tie rods must be able to rotate according to the direction in which the wheel is turned. Rod end bearings allow tie rods to perform this rotation in a precise and controlled manner. To learn more about rod end bearings and how they work, keep reading. If you’re looking to purchase Rod Ends, Monroe has you covered.
Rod End Bearings Explained
Also known as a heim joint in the United States or a rose joint in the United Kingdom, a rod end bearing is a mechanical joint that features a rounded ball-like swiveling tip. They were invented in Germany during the 1930s to 40s for use in aircraft control systems. This promoted a company called H.G. Heim Company to patent and produce its own rod end bearings in North America, which is why the mechanical joint now has the moniker “heim joint.”
H.G. Heim Company has since closed its doors for business, but rod end bearings are still produced and used throughout the world. Automotive tie rods are just way in which rod end bearings are used. They are used in countless other applications in which an articulating joint is needed, including aircraft control systems, steering links, track rollers and more.
Rod end bearings are typically made using the following materials:
Steel
Stainless steel
High-carbon steel
Aluminum
Male vs Female Rod End Bearing: What’s the Difference?
A rod end bearing can be classified as either male or female depending on the way in which the threading is designed. Male rod end bearings are designed with external threading. In comparison, female rod end bearings are designed with internal threading. With interior threading, female rod end bearings can handle unique applications that aren’t possible with male rod ends bearings. Helicopters, for instance, often use female rod end bearings to adjust the direction of the blade. They allow pilots and aviation technicians to fine tune their blade adjustments.
You can see an example of both male and female rod end bearings in the photo above. The red rod end bearing is male because the threading is located on the exterior, whereas the black rod end bearing is female because the threading is concealed inside it.
Lead Screw
A lead screw is a kind of mechanical linear actuator that converts rotational motion into linear motion. Its operation relies on the sliding of the screw shaft and the nut threads with no ball bearings between them. The screw shaft and the nut are directly moving against each other on a large contact area, so higher energy losses due to friction are produced. However, the designs of lead screw threads have evolved to minimize friction.
The lead screws are a cost-effective alternative to ball screws in low power and light to medium-duty applications. Since they have poor efficiency, their use is not advisable for continuous power transmission. Unlike ball screws, they operate silently with no vibration and have a more compact size. They are typically used as a kinematic pair (linkage) and actuation and positioning in equipment such as lathe machines, scanners, recorders, wire bonders, and disk drive testers. They are used to transmit forces in testing machines, presses, and screw jacks.
The components of a lead screw are the following:
Screw Shaft
The screw shaft is a cylindrical rod that has a single or series of grooves running helically around its length; this is referred to as the external thread.
Thread
The thread is the structure responsible for converting rotational motion into linear motion as the screw shaft and the nut slide with each other.
Nut
The lead screw nut is a cylindrical section that has an internal thread that matches the external thread of the screw shaft.Lead screws may be operated in two possible ways. One mode of operation is either the screw shaft or the nut rotates and moves linearly while the other component is fixed. This mode is commonly seen in printers and helical pairs. The other mode of operation is either the screw shaft or the nut rotates but does not move linearly. This mode is commonly seen in presses and lathes.
The design aspects of lead screws are the following:
Major Diameter
The major diameter is the largest diameter of the thread. The major diameter of the screw shaft is the distance between two opposite crests, while the major diameter of the nut is the distance between two opposite roots.
Minor Diameter
The minor diameter is the smallest diameter of the thread. The minor diameter of the screw shaft is the distance between two opposite roots, while the minor diameter of the nut is the distance between two opposite crests.
Crest
A crest is the raised helical structure in an external thread (screw shaft) and the recessed helical structure in an internal thread (nut).
Root
A root is the recessed helical structure in an external thread (screw shaft) and the raised helical structure in an internal thread.
Thread Depth
The thread depth is the distance from the root to the crest, measured radially.
Flank
The flank is the surface that connects the root to the crest.
Pitch Diameter
The pitch diameter, or the effective diameter, lies concentrically and approximately halfway between the major and minor diameters. It is the diameter of the imaginary cylinder whose circumference intersects half of the thread pitch.
Pitch
The pitch is the axial distance between two adjacent threads measured parallel to the axis. It is equivalent to 1/number of threads per inch.
Lead
The lead is the linear distance traveled by the screw shaft or nut along its axis in one complete revolution (3600 rotation). As the lead increases, the linear speed also increases, but the load capacity of the lead screw decreases, etc.
Ball Bearings - A Complete Buying Guide
Ball bearings are rolling-element bearings which use balls to maintain the separation and distance between the bearing races. They are designed to reduce rotational friction while supporting both radial and axial loads.
The types of ball bearings that we think of today were initially manufactured at the end of the 19th century. The Welsh inventor Phillip Vaughan was given the first patent for ball bearings and his was the earliest design to feature a ball running along the groove in the axle assembly. Another major development came in 1869 when the Paris-based bicycle mechanic Jules Suirray created the first ball bearing of the radial variety. This radial bearing was included in the manufacture of the bicycle that French racer James Moore rode to victory in the first Paris-Rouen race of 1869.
The use of ball bearings for manufacturing purposes has become widespread since the turn of the 20th century. They are integrated into the production of various mechanical instruments and devices due to the associated ease of movement and friction reduction. Ball bearings allow for the injection of motion between different parts and transmit energy for mechanical operation.
Open-style ball bearings are the most common variety. However, there are also shielded-style bearings, which feature metal shields on either one or both sides. The shield prevents dirt and debris from contacting and affecting the operation of the bearing. However, it also allows for the free flow of oil through the bearing for smooth operation. The use of ball bearings featuring seals has become increasingly common during recent times. These bearings also function effectively and are particularly unlikely to fail. The more balls featured within the ball bearing, the greater the load that the bearing will be able to take.
What Are the Uses of the Claw Hammer?
There are several types of hammers used for different construction processes; however, the claw hammer is the most common type used. The hammer contains a steel head and a handle made from various different types of materials. It is used primarily for pounding or extracting nails from wood.
Specifications
Claw hammers are commonly used for everyday purposes and for construction projects. These types of hammers weigh anywhere from 7 to 32 oz. The weight is derived from the head of the hammer only. The handle of a claw hammer is made from either wood, fiberglass or steel. If a claw hammer is laid down, it resembles the letter "T." The handle is the long part of the "T," while the top line of the "T" is the hammer's head.
Uses
The main purposes of a claw hammer are to pound nails into wood or extract nails. One side of the hammer head is flat and is used for pounding. The other side of the hammer head contains a claw and is used for extracting nails out of surfaces such as wood. The claw side of the hammer head resembles the letter "V" which allows a nail to fit into it. The person using the hammer places the claw hammer with the claw around the nail and pulls up or down with the handle to extract the nail.
Considerations
Higher priced hammers typically are built stronger with sturdier handles. Claw hammers are built using two pieces: the handle and the head. The two pieces are then attached. Other claw hammers are built and forged using only one piece. These types tend to be harder to break when using them.
Details
Claw hammers are designed to be used with wood working projects. They are not built for metal projects. One type of claw hammer is called a framing hammer. This type is designed to reduce the number of strikes it takes to pound a nail into wood and contains a larger, heavier head.
|
|
|
What is Hook and Loop? |
Geschrieben von: bop13mo - 20.04.2022, 02:52 - Forum: News
- Keine Antworten
|
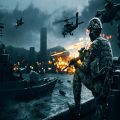 |
What is Hook and Loop?
Hook and loop fasteners are constructed from of two different pieces of nylon, one side acts as the "loop" (softer to the touch) the other side is the "hook" together these create a strong closure, whilst pulling the strips apart directly is easy, trying to separate them any other way is very difficult. Hook & Loop fasteners can be so strong that a two inch square piece is enough to support a 79 kg person. The strength of the bond however depends on how well the hooks are embedded in the loops & how much surface area is in contact with the hooks, along with the force pulling the two pieces apart.
If Hook & Loop is used to connect two rigid items together for example and picture frame to a wall the bond is very strong as any downward force is spread across the entire surface of the Hook and Loop sections, this only enforces it's strength by engaging more hooks into the loop, but by peeling the frame away from the wall, removal is relatively easy.
On garments and footwear, where hook and loop is used as a strap or pocket closure, opening is easy as a peeling action is used, this pulls each hook from the loop in smaller sections.
The Actual Definition of Textile & Its Surprising Difference from Fabric
If you work in the fashion industry, chances are you work with textiles almost constantly. Whether you're shopping for, printing on, or working with textiles, they never seem to differ much from any fabric you've worked with. Ever wonder why this is? And if they're truly the same thing, what's the definition of a textile and how is it different from fabric?
As it turns out, textiles have many uses outside of the fashion world. Aside from the obvious— clothing, bags, home decor, and so on— textiles are an important part of the medical field, toy manufacturing, weaponry, agriculture, and other unexpected fields. If you're wondering what's the difference between textiles and fabric, the answer is a lot more specific than you'd think.
To discern the vital differences between textiles and fabric, the term ‘textile’ must be clearly defined. The definition of textile is any material made of interlacing fibers, including carpet and geotextiles. Any woven or knitted fabric is a textile. What every textile has in common is that it’s made from textile fiber.
Products of textile fiber include yarn, thread, natural silk, rayon, chemical fiber short-hair silk, elastic silk, and metal wire. Textiles are created by processing, weaving or knitting these materials. These can create typically manufactured goods, such as clothing, accessories, gloves, hats, and blankets, or any type of plastic, industrial, natural fur, agricultural or medical fabric. This means that beyond the world of fashion, textiles comprise of any woven or knitted material for any use.
One example of specialized use of textiles are geotextiles, a permeable fabric that separates, filters, reinforces, protects or drains soil. Geotextiles are commonly used to improve the soil where structures, roads, or pipelines are built. These textiles have various types of material like open-mesh, warp-knitted, and non-woven textiles.
Another example is medical dressings and bandages, which are classified as medical textiles, or healthcare textiles. These textiles are more specifically used in the medical field for first aid, clinical or hygienic purposes and rehabilitation. Medical textiles must have specific qualities to be useful in the field such as biocompatible, good resistance to alkalis, absorption, and repellence, among others.
You can categorize agrotextiles, automotive textiles and other specialized textiles by their industry-specific usage. While they may consist of similar components, their use is vastly different. For this reason, you categorize textiles by industry, not components.
Textile fibers can be classified using 3 different methods: by structure, utility, and production of the textiles.
The first classification of textile fibers is according to the structure, the materials, processing technology, texture, appearance and main use of textiles which can be divided further into 14 different categories.
The second classification method is by the use of textiles, divided into clothing textiles, decorative textiles, and industrial textiles.
Lastly, textiles can be classified according to its production, into line, belt, chenille, woven fabric, textile cloth, and more. These various methods help to distinguish the specific fibers needed for a certain product.
A guide to cable ties
What are cable ties used for?
They're fasteners that bundle your cables and wires together to keep them organized and prevent damage. They come in different sizes, lengths, materials and even colors. The different uses of cable ties vary across industries, but what they all have in common is that they're the most effective way to manage your cables.
First, let's get a picture of the type of cable ties available. The table below is by no means exhaustive, as there are subsets of cable ties within this table. For example, standard cable ties can be weather resistant, which gives them different applications than their cousins'.
Standard cable ties are a fantastic all-rounder, but when you need specialized cable ties, you can get those too.
The most common material for cable ties, nylon is a tough material with good thermal, and abrasion resistance. It also resists fuels and most chemicals. Nylon 6/6, the grade most often used for cable ties, meets UL94 V-2 flammability ratings and has a working temperature range from -40°F to 185°F.
Nylon cable ties can be heat stabilized for continuous or extended exposure to high temperatures of up to 250°F. The cable tie manufacturing process can also produce UV stabilized ties for outdoor use. For example, you can have the same cable tie, but manufactured for different applications.The average passenger airplane wields 124 miles of cables, so excellent cable management is absolutely critical. The types of cable ties needed vary. For small, tight spaces, miniature heat-stabilized cable ties are a must. For hoses and larger cables, heavy duty heat stabilized cable ties are needed. Push mount cable ties also work well for aerospace and it's best to go with a heat-stabilized option for thermal endurance.
The inspiration behind hook-and-loop fastening
Hook-and-loop fastening (also known as ‘touch-and-close’) has been used by footwear designers for many years. The system is commonly used where ease and speed of fastening is desirable – for instance on young children’s shoes (where the wearer has not yet mastered the skill to properly tie laces), and some items of sportswear. It has even been utilised in certain styles of fashion footwear.
What is hook-and-loop? Two components are involved, typically consisting of a pair of lineal fabric strips (or shaped items) which are attached – normally by stitching or adhesive – to the opposing surfaces to be fastened. The first face features tiny hooks, and the second has even smaller loops. When the two components come into contact, the hooks catch in the loops and the two pieces bind together. When separated, by pulling or peeling the two surfaces apart, hook-and-loop strips make a distinctive ‘ripping’ sound.
Birth of an idea
It is a common misconception that the first hook-and-loop fastening was designed by the USA’s National Aeronautics and Space Administration (NASA) for its space programme. While it is true that the organisation made good use of this product (each space shuttle reportedly flew equipped with ten thousand inches of a special fastening made of Teflon loops, polyester hooks and glass backing, used in the astronauts’ suits and to anchor equipment), the idea for hook-and-loop fastening actually dates back to the early 1940s.
The hook-and-loop fastening system was conceived in 1941 by Swiss engineer, George de Mestral. The idea reportedly came to him after returning from a hunting trip with his dog in the Alps. He took a close look at the burrs (seeds with hooks) that kept sticking to his clothes and his dog’s fur. On examining them under a microscope, he observed hundreds of ‘hooks’ that caught on anything with a loop, such as clothing, animal fur, or hair. He soon saw the possibility of binding two materials together in a way that they could be easily parted – if he could work out how to reproduce the hooks and loops. This is a classic example of the copying of nature's mechanisms, called ‘Biomimicry’.
With the help of a weaver, two hook-and-loop strips based on cotton were made. However, the cotton wore out quickly, so Mr de Mestral turned to synthetic fibres. He finally selected the recently developed nylon and, through trial and error, eventually discovered that, when sewn under hot infrared light, nylon forms hooks that worked well for the hook side of the fastening. Although he now knew how to make the hooks, he had yet to work out a way to mechanise the process, as well as making the looped side of the fastening.
At this point, Mr de Mestral found that when nylon thread was woven in loops and heat-treated, it retained its shape and was sufficiently resilient. Nevertheless, the loops had to be cut in exactly the right place so that they could be repeatedly fastened and unfastened. He bought a pair of shears and trimmed the tops off the loops, which worked well. It took another eight years to mechanise the process of weaving the hooks and a further 12 months to create the loom that trimmed the loops after weaving them. In total, a decade passed before an efficient mechanised process was created.
Mr de Mestral submitted his idea for patent in Switzerland in 1951, and this was granted four years later. The original product – ‘Velcro’ – was born, a name taken from the French words ‘velours’ (velvet), and crochet (hook). Within a few years, patents were also obtained in Belgium, Canada, Germany, Italy, Sweden, Switzerland, the Netherlands and the UK.
Mechanisms: Hook And Loop Fasteners
If you're going to be inspired by natural mechanisms, it pays to be out in nature. During a hike in the Alps with his dog in 1941, George de Mestral, a Swiss electrical engineer, found his inspiration. He and the animal had picked up a multitude of burrs during their walk, and as George picked them out of the fur and off his clothes, he wondered how they managed to attach themselves so tenaciously.
For anyone unfamiliar with these unwelcome travelers, burrs are the spiky ripe fruit of any of a number of plants, most commonly the Burdock. The burrs are a dispersal strategy used by the plant to send its seeds far and wide by hitching a ride on the coat of a passing animal.
George put a burr under a microscope and was fascinated by what he saw. Each spike on the burr ended in a sharp point that looped back into a hook shape. Mixed in with the spikes were strands of the dog's hair, knotted and tangled around the multitude of hooks. What's more, the wool of his trousers and socks, standing out from the surface of his clothing as tiny loops, were the perfect medium to catch the burr's hook.
In that moment, George found inspiration for a new kind of fastener, and he would labor for the better part of a decade perfecting his invention. Early prototypes using natural fibers worked, but not for long as the shape of the mechanism quickly wore out. George found that the new miracle fiber Nylon was perfect for hooks and the loops that would stand up to repeated use, and was soon able to create small amounts of working fasteners. But perfecting a mechanized process for creating the stuff proved difficult. He finally hit upon weaving stiff Nylon threads into loops while heating the thread, causing it to stick out from the backer. A clip with shears then formed the hooks, and loops came from thinner threads similarly woven but left unsnipped.
|
|
|
|