Hallo, Gast |
Du musst dich registrieren bevor du auf unserer Seite Beiträge schreiben kannst.
|
Benutzer Online |
Momentan sind 79 Benutzer online » 9 Mitglieder » 70 Gäste
|
Aktive Themen |
Wo kauft ihr ein?
Forum: Allgemein
Letzter Beitrag: marco91
27.05.2025, 14:49
» Antworten: 1
» Ansichten: 140
|
Streamingzimmer einrichte...
Forum: Allgemein
Letzter Beitrag: marco91
27.05.2025, 14:30
» Antworten: 1
» Ansichten: 111
|
Werbebriefe?
Forum: Allgemein
Letzter Beitrag: fritz500
12.05.2025, 17:56
» Antworten: 1
» Ansichten: 191
|
Auto privat verkaufen?
Forum: Allgemein
Letzter Beitrag: fritz500
12.05.2025, 16:21
» Antworten: 1
» Ansichten: 173
|
Vape welche Sorte?
Forum: Allgemein
Letzter Beitrag: conradme
05.05.2025, 20:52
» Antworten: 1
» Ansichten: 205
|
Was tun in Hamburg?
Forum: Allgemein
Letzter Beitrag: conradme
05.05.2025, 19:32
» Antworten: 1
» Ansichten: 199
|
Automatisierung in der In...
Forum: Allgemein
Letzter Beitrag: maxmeyers
25.03.2025, 13:20
» Antworten: 1
» Ansichten: 608
|
Kurzwaren im Internet?
Forum: Allgemein
Letzter Beitrag: fritz500
25.03.2025, 08:54
» Antworten: 1
» Ansichten: 524
|
Mittel gegen schwitzen?
Forum: Allgemein
Letzter Beitrag: fritz500
25.03.2025, 08:00
» Antworten: 1
» Ansichten: 534
|
Sportbootführerschein onl...
Forum: Allgemein
Letzter Beitrag: marco91
24.03.2025, 22:16
» Antworten: 1
» Ansichten: 506
|
|
|
Intelligent Injection Molding on Sensing, Optimization, and Control |
Geschrieben von: aop21sd - 29.03.2022, 02:24 - Forum: News
- Keine Antworten
|
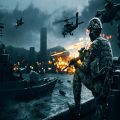 |
Intelligent Injection Molding on Sensing, Optimization, and Control
The term quality has become a “catch all” term used in describing the various characteristics of an object. It is nearly impossible to define the term consistency. The quality is any particular or specific characteristics of a product development design object that contains or relates information about the object. This is primarily a chunk of geometry distinguished by its ability to perform a function with one or more other. In this primary processing conditions are studied from concept development to manufacturing of the product. Effect of different factors studied on the basis of processing parameters. Since quality and productivity are the two important contradictory objectives in any machining process. Some extent of quality has to be compromised while assurance giving for high productivity. Similarly productivity will be decreased while the efforts are channelized to enhance quality. To ensure high quality and productivity, it is necessary to optimize machining parameters. Various responses of quality of injection moulding process has been studied on the basis of performance parameters and methods. This paper aims to present plastic injection moulding process conditions. The processing conditions satisfied quality based product manufacturing.
Temperature control prevents quality issues such as shrinkage, warping and stresses from developing in the injection-molding processes.
From manufacturing personal items like toys and toothbrushes to industrial parts like plastics utilized in automobiles, injection molding is one of the most relevant manufacturing techniques in use today. This article will define what injection molding is, outline the steps involved, and explain the need for temperature control in the process.
Injection molding is a specialized manufacturing technique used for fabricating plastic parts and items. It allows for the mass production of several thousand — or even millions — of identical parts of a specific dimension and quality.
Plastic injection molding involves injecting molten plastic into a mold (or cavity), which defines its molded part’s shape after it solidifies. The basic requirements for the process are the injection-molding machine, raw plastic material and the mold.
The injection-molding machine consists of a hopper, through which pelletized plastics are fed into the machine; a heating barrel with a reciprocating screw; and an injection nozzle. The most common thermoplastics utilized in injection molding are nylon (PA), polycarbonate (PC), polypropylene (PP) and acrylonitrile-butadiene-styrene (ABS). Molds used can be single- or double-cavity type, depending on the application.
Tooling Investment Costs. When a electric car mould part is being manufactured for the first time, the design is first prototyped with a test material to ensure accuracy using techniques such as 3D printing or CNC machining. The mold tool is made of steel or aluminum material and must be designed to precise dimensions.
Prototyping and Testing. With injection molding, manufacturing companies must carry out extensive testing and prototyping of the entire system using replicas. Any subsequent modifications to the final design will require either modifying the tools or scrapping them completely — both of which could add significant costs to the production budget.
Size and Thickness Limitations. Because injection-molding machines and molds typically have limited sizes, injection molding may not be suitable for designing large plastic parts. Also, injection molding tends to create mostly molded parts of a uniform thickness. This characteristic may be undesirable to some manufacturers that require variation in this aspect. This is because injection-molded parts must be created with a sufficient wall thickness (at least 1 mm) to prevent problems with filling the mold.
Many manufacturers use cooling tower water to cool the small channels within the mold with a temperature regulator attached to the injection-molding machine, regulating its temperature. While this technique is effective and incurs a lower operating cost, the mold will be prone to contamination. Cooling towers are open-loop systems. By contrast, an industrial chiller can be used to regulate the temperature via closed-loop cooling, ensuring a higher degree of product purity.
When plastics for the injection-molding process are being heated and mixed inside a machine, a specific temperature limit must be maintained as the temperature of the process will directly impact the quality of the final mixture.
If the temperature is too low, the components may not mix properly. Alternately, when the temperature is too high, the mixture might become burned. Thus, there is typically an ideal point, or a prescribed temperature at which the process must be maintained.
Mold Temperature. The temperature of the precision mold is another essential consideration that affects the quality of the injection-molded part. Getting the best quality mold is a balance between heating the mixture sufficiently to create a homogeneous mixture and cooling it down at an ideal rate. Anything else would be undercooling or overcooling.
Undercooling and Overcooling Issues. Improper polymer flow is a direct consequence of under- or overcooling issues in plastic injection mould. When the mixture is not cooled sufficiently, it may not solidify completely before being ejected. This may leave residual plastic in the mold.
Conversely, excessive cooling causes a lack of uniformity in the plastic material. This may cause further problems down the line such as shearing, cracking and cavities that do not fill up completely. Maintaining the mold temperature at a set temperature will yield the most optimum results.
Temperature Control with an Industrial Chiller System
Close tolerance temperature control units can be used with industrial chiller systems to provide close temperature tolerances for process water. When combined with a compatible and suitably sized industrial chiller, the temperature control unit can maintain the process temperatures at ±0.5°F of the set 33°F value, ensuring a stable injection-molding process without catastrophic freezing failures.
The close tolerance temperature control units come in varying flow variations and configurations and standard models have a pump and heat exchanger with a jacketed tank or a heat exchanger.
Plastic moulding is the process of pouring liquid plastic into a certain container or mould so that it hardens in that customized shape. These plastic moulds can then be used for a wide range of purposed. There are 5 types of plastic moulding that is considered to be the most effective and most popular.
These 5 types are extrusion moulding, compression moulding, blow moulding, injection moulding and rotational moulding. We will look at the details pertaining to each of these methods so that you can decide which one will be the most effective for you to use.
1. Extrusion Moulding
With extrusion moulding, hot melted plastic is pressed through a shaped hole to create a lengthy shaped plastic part. This customizable shape that the liquid plastic gets pressed through is called a die. This die is custom made for the particular outcome that is desired. It is almost like pressing dough through a press to make shaped cookies.
The other forms of plastic moulding also use extrusion so get the raw liquid into the commodity mould, the difference here is that other methods use the moulds to make the desired shape and here the extrusion itself is making the shape with the use of the die’s shape.
When using this method your outcome product will continuously have the same shape along the length of it. These can be things like straws or PVC pipes. These types of parts can be made at very high volumes because it can just keep producing the same shape without end.
In comparison, this type of moulding is low cost because the equipment is fairly simple and can have high productivity. The downside to this method is that you are very boxed in when it comes to the variety of parts you can make.
Injection molding is one of the most significant material processing methods for mass production of plastic products. It is widely used in various industry sectors, and its products are ubiquitous in our daily life. The settings and optimization of the injection molding process dictate the geometric precision and mechanical properties of the final products. Therefore, sensing, optimization, and control of the injection molding process have a crucial influence on product quality and have become an active research field with abundant literature. This paper defines the concept of intelligent injection molding as the integral application of these three procedures—sensing, optimization, and control. This paper reviews recent studies on methods for the detection of relevant physical variables, optimization of process parameters, and control strategies of machine variables in the molding process. Finally, conclusions are drawn to discuss future research directions and technologies, as well as algorithms worthy of being explored and developed.
The Society of the Plastics Industry (SPI) has reported that, in the United States, the plastics industry is the third largest manufacturing industry. In 2017, the US plastics industry accounted for $432.32 billion in annual shipments and directly employed nearly one million people [1]. Hence, the plastics industry has a large contribution to the nation’s economy. Plastics are now among the most widely used materials and their use covers the entire spectrum of industries worldwide [2]. Injection molding is regarded as the most important and efficient process used to manufacture plastic products. It accounts for approximately 80% of the plastic merchandise in the modern plastics industry [2], and as such, it is one of the important pillars of the manufacturing industry. As a highly complicated process, plastic injection molding can be divided into three stages: filling, packing, and cooling. During the entire process, the polymer is subject to large and dynamic changes in pressure and temperature. The whole process is complicated because the process variables are strongly coupled and hard to analyze accurately. For now, manufacturing of qualified products by injection molding still mainly relies on manual operation and trial-and-error methods [3–5]. Obviously, this traditional approach has disadvantages of low production efficiency, poor reliability and repeatability, and dependence on prior experience. Therefore, it is imperative and crucial to develop an advanced injection molding method that is science based and technology oriented.
Recently, much attention has been focused on intelligent (smart) manufacturing, which represents an in-depth integration of next-generation artificial intelligence (AI) technology and advanced manufacturing technology. It runs through every link in the full life cycle of design, production, product, and service [6]. Intelligent injection molding refers to the production process that employs AI technology—such as extracting information from production, computer optimization methods, and control strategies—to develop an online production optimization system. Through the comprehensive use of sensing, optimization, and control methods, the intelligent injection molding production process can increase production efficiency and product quality.
During the production process, when material and mold are preselected, an intelligent injection molding method is required to obtain high quality and stable production. As shown in Figure 1, intelligent injection molding contains three phases—sensing, optimization, and control—all of which are interrelated. Process sensing is first needed to realize real-time detection of variables from the injection-molding process and further on to diagnose and guide the manufacturing process. Moreover, optimal process parameters should be determined by process optimization since it is the key to obtaining high-quality injection molded products with high precision. Finally, sufficient machine control accuracy and repeatability—which means robust control over machine parameters—are required. Furthermore, advanced control strategies will help to conserve energy in manufacturing [7]. Integrating these three phases into an effective online quality control model, which is the section in the dotted-line frame in Figure 1, is one of the major goals of intelligent injection molding. It has attracted extensive attentions from many researchers in the field of injection molding.
In a 2005 review article, injection molding control [8] after process setup was classified into three levels—machine control, process control, and quality control. Due to the lack of quality sensors and the process and quality relationship model, there is a potential opportunity for advancement in the optimization and control of the product quality in injection molding. Moreover, with further development of science and technology in injection molding, and the fact that there has been very little review of process sensing, this paper aims to review and summarize the research on intelligent injection molding in recent years. It will focus on sensing, optimization, and control so that readers will be able to obtain useful information and an overview of the intelligent injection molding process. This paper is outlined as follows. Section 1 provides a brief introduction of intelligent injection molding. Sections 2, 3, and 4 discuss sensing, optimization, and control methods for the injection molding process and present up-to-date developments in these fields. The last section provides a summary of and future directions for intelligent injection molding.
The sensing of the injection molding process is focused on the temperature, pressure, position, speed, etc., which reflect the physical state of the process. Temperature and pressure are the two fundamental physical variables that are the most important in the injection molding process. Furthermore, among various sensing technologies, temperature and pressure sensors are the most well developed and the most widely utilized. By means of sensing the temperature and pressure, one can obtain abundant information about the mold and polymer melt. With continuing technology development, some new methods have emerged in the field of injection molding. Some of them are capable of characterizing more variables besides temperature, pressure, position, and speed. This section will briefly introduce the conventional and emerging methods used in injection molding processes and the up-to-date research progress. Finally, a conclusion and analysis will be put forward and discussed.
|
|
|
The science of street lights: what makes people feel safe at night |
Geschrieben von: aop21sd - 29.03.2022, 02:23 - Forum: News
- Keine Antworten
|
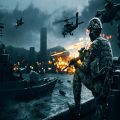 |
The science of street lights: what makes people feel safe at night
Winter is coming: the nights are drawing in and in the Northern Hemisphere the hours of darkness already outnumber the hours of daylight. Research has shown that darkness produces a big fall in the number of people out walking – and a major reason for this is that people feel less safe walking in the dark.
There may be an evolutionary explanation for why people feel less safe at night – we can’t see as well, and this may have exposed our ancestors to greater threat from predators. Nowadays, it’s not so much the prospect of being eaten by a savage beast that concerns would-be pedestrians, but the fear of being mugged or victimised.
Some studies suggest that new outdoor lighting can reduce crime rates in an area, but there is conflicting evidence on this. A large review of research found a link between new lighting and reduced crime rates, but improvements were seen in daylight as well as darkness, suggesting that solar led street light is not the only factor. This review has also been criticised by other researchers, and a large statistical analysis found no link between crime rates and switching off or dimming street lighting at night.
Street lights may or may not have an effect on crime, but one thing’s for sure – brighter levels of light do make people feel safer when walking at night. This can lead to a significant increase in the number of minutes people spend walking each week. It can also reduce the number of people who avoid leaving their homes at night, reduce social isolation, improve physical and mental well-being and increase community pride.
Street lighting can improve the quality of neighbourhood life by making people feel safer – but, even so, it would be unwise to flood our streets with light at night. Street lighting costs money: the UK’s annual bill is estimated at around £220m. Artificial light at night may also have a negative impact on wildlife and the natural world, for example by stunting the growth of frogs and toads and preventing them from laying their eggs.
The skyglow from street lights also means we rarely get to see the true wonder of the night sky, frustrating astronomers and limiting our appreciation of the natural environment. For these reasons, lighting should be used selectively and efficiently – and this requires good guidance to help those responsible for installing and maintaining our street lighting.
The guidelines for street lighting in the UK and many other countries are currently based on questionable evidence. That’s why our lighting research group at the University of Sheffield undertook a programme of research to find out how lighting relates to feelings of reassurance after dark, and improve the evidence on which lighting guidelines are based.
Illuminating evidence
In one recent experiment, we asked people to walk along a number of streets in the city of Sheffield at night and rate how safe they felt. We also asked these people to walk and rate the streets in the day, to create a baseline measure of safety and to account for biases that may occur if safety ratings were taken only after dark.
The difference in safety ratings between the day and night walks told us something about the lighting on that street – the smaller the difference between day and dark ratings, the safer people felt due to the lighting. We compared our participants’ different ratings against measures of the lighting on each street, including the average illuminance (amount of light falling on the street surface) and uniformity (how evenly spread out the lighting was).
Today, average illuminance is the main measure used when installing and evaluating led street light. But we found that, while increasing average illuminance was linked with improved feelings of safety, uniformity was more important for making people feel safe. So it might be more important to have evenly distributed lighting, rather than bright lighting, to make people feel safer.
Local authorities are undergoing major changes to their lighting, as they replace the traditional orange sodium lamps with new LED lighting. These new LEDs are more energy efficient, which saves taxpayers’ money. They also give councils greater control over the lighting they provide, for example by dimming and switching off when there are no pedestrians about.
Used properly, street lights can improve people’s lives and help neighbourhoods come alive at night. But there’s still a lot to discover about how people respond to street lighting and the impacts it has on society and the environment – experiments such as these can help to light the way.
Financial and carbon reduction incentives have prompted many local authorities to reduce AIO Solar LED Street Light at night. Debate on the public health implications has centred on road accidents, fear of crime and putative health gains from reduced exposure to artificial light. However, little is known about public views of the relationship between reduced street lighting and health. We undertook a rapid appraisal in eight areas of England and Wales using ethnographic data, a household survey and documentary sources. Public concern focused on road safety, fear of crime, mobility and seeing the night sky but, for the majority in areas with interventions, reductions went unnoticed. However, more private concerns tapped into deep-seated anxieties about darkness, modernity ‘going backwards’, and local governance. Pathways linking lighting reductions and health are mediated by place, expectations of how localities should be lit, and trust in local authorities to act in the best interests of local communities.
Electric street lighting has been a feature of urban and suburban settlement since the end of the nineteenth century. Indeed, the electrification of lighting has in many ways defined the modern city, in extending the visibility of its public spaces, inhabitants and itinerants beyond the hours of natural daylight (Martland, 2002, Otter, 2002) and changing the meanings of the night for city dwellers (Schlör, 1998). However, in many areas of England and Wales, as in other countries, the taken-for-granted assumption that streets and public spaces will be lit at night has been disrupted in recent years. Many local authorities responsible for LED Street Lighting Solar have reduced street lighting at night, a policy primarily driven by requirements to reduce costs and carbon emissions under the Climate Change Act 2008 (Department for Environment Food and Rural Affairs (DeFRA), 2011), but also with considerations of contributing to reductions in environmental light pollution (The Royal Commission of Environmental Light Pollution, 2009). A rapid growth of technological innovations over the last 20 years has enabled greater control over the colour, intensity and switching on schedules of public lighting stock (Shaw, 2014a), and local lighting authorities across England and Wales have adopted a wide range of interventions. These include: removing, or switching off lanterns in street light columns (‘switch off’); reducing the number of hours that they are switched on (‘part-night lighting’); replacing sodium lanterns by ‘white’ LED light; and ‘dimming’ lanterns through centrally managed systems. Some of these interventions reduce the amount, or duration of, artificial light at night. Switch off and part-night lighting result in dark streets which were once lit, at least for some of the night time hours.
Changes which reduce lighting, particularly ‘switch off’ and part-night lighting in urban areas, have attracted considerable public and media concern, centring on crime, fear of crime, perceptions of safety, and road safety. These are all important determinants of health and wellbeing: directly in the case of road safety; and indirectly, in that fear of crime, for instance, has multiple pathways that impact on mental health (Lorenc et al., 2012). To date, empirical research on fear of crime and perceptions of safety have focused largely on improvements to lighting, with the assumption that more lighting will improve security, and reduce fear of crime (Lorenc et al., 2013). However, empirical findings on the impact of improved lighting on perceptions of crime, personal security and road injury have been mixed, with no clear conclusions on how increased lighting does improve these health outcomes (Atkins et al., 1991, Painter and Farrington, 1997; Pain et al., 2006). A systematic review of the effects of increased street lighting on crime (Welsh and Farrington, 2008), including 13 controlled before and after studies, concluded that improved street lighting in public spaces did not reduce crimes at night any more than was observed during the day. The authors suggest that the protective mechanism of street lighting may therefore act more through increasing pride in the locality or social control, rather than directly increasing surveillance to deter crime. As Koskela and Pain (2000), suggest, ‘fear of crime’ is a complex outcome of the political and social meanings of space, including gendered meanings, and is unlikely to be deterministically tied to isolated environmental conditions such as public lighting. On road traffic injuries, Beyer and Ker’s (2009) systematic review also noted the poor methodological quality of research to date, and suggested more high quality evaluations were needed to adequately determine the effectiveness of street lighting for reducing the incidence of road traffic injury.
If research on how improved lighting impacts on health outcomes is inconclusive, that on reduced lighting is almost non-existent. There are no good grounds for assuming that the removal of a public good will have the reverse effects to those of providing or improving it. In addition, there are some rather different health outcomes that become the focus of reductions in artificial lighting. These relate to how reductions might mitigate the negative health impacts some have claimed from a growth in, and changing frequencies of, artificial light in the environment (Hölker et al., 2010, Falchi et al., 2011). Although the evidence base to date is weak (Vohra, 2013), a growing concern with light pollution as a potential hazard to health draws on studies of animals (Shuboni and Yan, 2010) and shift workers to identify disruptions in circadian rhythms and endocrine processes, which can affect sleep (Navara and Nelson, 2007) and, theoretically, health outcomes such anxiety, depression, obesity and even cancer incidence (Pauley, 2004, Fonken et al., 2009, McFadden et al., 2014). Broader public health concerns also include the more existential wellbeing effects of being able to see the night sky, and longer term environmental impacts of reduced carbon emissions (Claudio, 2009). The amount, and quality, of light at night has thus become a public health as well as political issue.
There have been some qualitative studies of public views of street lighting, identifying mixed and reflective views on the relationship between light and fear of crime, for instance (Pain et al., 2006). To date, though, there has been little research that directly addresses public views on the possible relationships between street lighting reductions and health more generally. To address this gap, this study therefore aimed to explore public views of the potential health and wellbeing impacts of reduced street lighting. We aimed to explore public understanding of the possible pathways through which street lighting might impact on health and wellbeing, and how reductions in street lighting were understood as impacting on health and wellbeing outcomes.
|
|
|
What is your welding torch power? |
Geschrieben von: aop21sd - 29.03.2022, 02:21 - Forum: News
- Keine Antworten
|
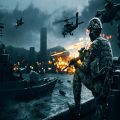 |
What is your welding torch power?
When choosing a mig welding torch for our equipment, one of the most important factors is the power of the gun, or what is the same, the maximum intensity of use that it can endure.
Most manufacturers use the maximum intensity of use as a reference when selecting the right torch, but this reference should be understood only as that, a reference. The intensity in real circumstances will be notably lower for the following reasons.
When you think of the dangers of welding, the usual suspects immediately come to mind: In addition to obvious things like harmful UV radiation during arc welding, sparks and welding spatter, or even hazards from electrical current, there are also the invisible dangers of welding, for example, by inhaling harmful welding fumes.
There are multiple ways to protect the welder from all these hazards: Wearing personal protective equipment (PPE) when welding is considered a matter of course and protects the skin and, above all, the eyes from radiation and injuries caused by welding spatter and flying sparks. Fume extraction torches, ventilated welding helmets or fume extraction systems can filter toxic welding fumes from the air and thus protect the welder's respiratory organs.
But how can welders protect themselves in the long term against damage to their musculoskeletal system? What helps against permanently tense muscles, signs of fatigue and back pain?
An often underestimated aspect of welding is the tig welding torch itself!
Unhandy, heavy torches, which are not ergonomically adapted to the work processes, make the daily work for welders more difficult. Often long seams have to be welded without stopping and the heavy hose assembly is dragged behind or has to be lifted into the correct position.
Or when welding is done in an overhead position. Every welder knows what we are talking about: The welding material drips, the muscles are aching, the back hurts and the weight of the welding torch including the hose assembly quickly becomes a burden.
The hose assembly in particular is an important factor when it comes to weight reduction. Lightweight hose assemblies can weigh 30-50% less than a regular hose assembly, which has a significant effect. Of course, you shouldn't skimp on the material inside, because the plasma welding torch still has to be just as powerful as before.
Using light metal components for current-carrying cables in the hose assembly instead of the usual copper ensures a significantly lower weight, makes welding more comfortable and maintains performance - that of the welding torch and that of the welder.
The position of the trigger on the welding torch also has a decisive influence, because during a long working day this trigger has to be pressed countless times. If the welding torch lies comfortably in the hand and the distance and angle between the finger and the trigger are optimally selected, less energy is needed to reach the trigger and apply the required pressure.
A ball joint at the transition between the handle and the hose assembly specifically relieves the welder's wrist: the hose assembly is flexibly guided downwards directly behind the handle, thus reducing the leverage effect on the wrist. In addition, a ball joint facilitates oscillation during welding.
This study investigated the effects of welding current and torch position parameters, including torch-aiming position, travel angle, and work angle, on bead geometry in single-lap joint gas metal arc (GMA) welding. High-speed filming and macrographs of weld cross section were used to observe the effect of each welding parameter on the properties of the bead geometry, including penetration, leg length, and toe angle. Response surface methodology was used to establish the relationship between the welding parameters and properties of bead geometry and to estimate regression models for predicting bead geometry. Both welding current and torch-aiming position were found to have significant effects on bead geometry, with strong linearity between them and bead geometry. The coefficient of determination (R2) of the estimated response surface models was 0.7226 for penetration, 0.8802 for leg length, and 0.8706 for toe angle. Further, experimental results indicate that the estimated models are very effective.
This paper aims to develop a novel tungsten inner gas (TIG) wp-26v tig torch in order to join thin sheets efficiently. Using a narrowing nozzle (constricted nozzle) inside a conventional TIG torch can critically improve the position accuracy of the tungsten electrode and also the arc plasma characteristics and heat input density. In order to evaluate the efficiency of this new torch, weld bead appearance and cross-section images were examined by an optical microscope, scanning electron microscope (SEM), and electron back scatter diffraction patterns (EBSD). The results showed that in all cases, the weld bead profile was stable without undercut and burn-through. Full penetration weld was seen. The width of weld bead on the bottom surface was increased much in comparison to conventional TIG welding. However, the results from SEM and EBSD images indicated that in the case of low welding current, the blowholes were found out on the side of the thinner material (SS400). The penetration of SUS430 material to SS400 material was not good. It seems that no fusion of SUS430 material to SS400 at the bottom surface can be seen. Meanwhile, no blowholes were seen in the case of high welding current. The penetration was better, and the fusion was reached on the bottom surface.
This work is about the influence rule of inclination of gas cooled tig torch on the formation and characteristics of weld bead during the pulsed-gas metal arc welding (GMAW) process based on the robotic operation. The inclination of welding torch was an important operation condition during the pulsed-GMAW process, because it can affect the formation and quality of weld bead, which was the output of the process. In this work, the different inclination modes and values were employed to conduct actual welding experiments, and some influence rules can be obtained according to examine the surface topography and cross section. Then, to obtain further rules, serious measurements for the geometry characteristic parameters were conducted and corresponding curve fitting equations between inclination angles and the bead width, penetration and bead height were obtained, and the largest error of these curve fitting equations was 0.117 mm, whose corresponding mean squared error (MSE) was 0.0103. Corresponding verification experiments validated the effectiveness of the curve fittings and showed the second order polynomials were proper, and the largest errors between measurements and curve fitting equations for inclination angle under backward mode were larger than those under forward mode, and were 0.10 mm and 0.15 mm, respectively, which corresponded to the penetration and were below 10%, therefore the equations can be used to predict the geometry of the weld bead. This work can benefit the process and operation optimization of the pulsed-GMAW process, both in the academic researches and actual industrial production.
Pulsed-gas metal arc welding (GMAW) is a commonly employed arc welding process which was employed in industrial metal joining process and other relative areas [1,2,3]. In this process, the pulsed welding current generated from the welding power source is used to control the metal droplet included in the electrical arc. Using this process, stable electrical arc can be induced even various welding parameters are so small. Because the process can accurately control the heat energy of the electrical arc, the pulsed-GMAW process is more and more commonly employed for joining types of base metals [4]. Compared to the conventional GMAW process, the pulsed-GMAW process has various advantages, such as high productivity and process robustness, and obtains the products with fine grain size [5]. It can not only adjust the value and duration of base current to decrease the heat delivery, so as to avoid very large deformation and burn-off the base metals, but can also utilize the high peak current to realize the desired one-droplet-per-pulse (ODPP) metal transfer mode. The metal transfer mode can directly affect the formation and the surface of the weld bead [6]. The various merits of this technology make it being increasingly used for joining a wide variety of industrial occasions, due to its inherit advantages such as deep penetration, smooth weld bead, high welding speed, large metal deposition rate, lower spatter, lower distortion and shrinkage, lesser probability of porosity and fusion defects, and controllable heat input and all-position welding [7,8,9]. It is an advanced spray transfer process with low mean current, and the welding current is pulsed between high and low levels of short or long time intervals so that it brings the weld zone to the melting point during the pulse current period and allows the molten weld pool to cool and solidify during the background current period [7]. Hence, this process can realize a stable and controllable metal transfer process, and obtain weld beads with desired surface topography.
The evaluation of the welding quality is so important for process improvement and product optimization. Different welding processes had different evaluation criteria. For example, the nugget size or tensile-shear strength can be used to evaluate the quality of resistance spot welding [10,11]. During the GMAW process, the formation and characteristic of weld bead is the most commonly employed criterion to evaluate the quality of the operation, and this criterion involves more elements, such as crack, appearance, geometry characteristics, microstructure, and so on [12].
To meet the huge requirements of the actual industrial applications, many scholars and experts took efforts to explore the influences of the different operational conditions on the formation and characteristic of weld bead. Some relative contributions have been reported in the past decades. Rodrigues et al. [13] investigated the influences of three kinds of shielding gases and two activating fluxes on the geometry of welds produced by the tungsten inert gas (TIG) welding processes, which was other commonly used arc welding process. Shoeb et al. [14] studied the effects of some process parameters, such as welding speed, voltage and gas flow rate on the weld bead geometry, such as penetration, width and height, and in the work, mathematical equations were developed to describe the relations between the parameters and geometry parameters using factorial technique. In addition, to explore the weld bead forming rule during the double-pulsed GMAW process, our research group [15] employed the grey relational analysis method to quantitative establish the relations between some key operational parameters and the geometry characteristic parameters of the weld bead. The results showed that the average welding current and welding speed were the key elements which affected the characteristic parameters of the weld bead. Additionally, the same group [16] studied the effects of the operational parameters on the ripples of the weld bead; corresponding analyses showed that the most influential element on the distances of ripples was the welding speed, and the following was the twin pulse frequency. Moreover, recently, to increase the productivity during the actual production, the GMAW process usually collaborated with the industrial robot operation, which can significantly improve the accuracy of the real time control and make the operations more and more convenient. Aviles-Viñas et al. [17] proposed a real time computer vision algorithm to extract training patterns in order to acquire knowledge for predicting specific geometries, and the proposal was implemented and tested by an industrial KUKA robot and a GMAW type machine within a manufacturing cell. Chen et al. [18] employed a welding robot to acquire and optimize the weld trajectory and pose information, based on a laser sensor, charge-coupled device and other auxiliary instrument. Yang et al. [19] used an arc welding robot to detect the welding quality based on three-dimensional reconstruction using a special algorithm, and the results showed the system can quickly and efficiently fulfill the detection task of welding quality. These works denoted that using an industrial robot combined other technologies, many tasks which cannot be accomplished by traditional operations can be realized.
Despite that many reported contributions concerned that the influences of different operational parameters on the quality of weld bead, the relative works were mainly about the welding current, robot welding speed, and other common real-time control parameters. However, as a special and important operational condition, the inclination of the welding torch can also affect the formation and surface topography of the weld bead, because the welding torch is an executive component which is directly related to the energy delivery from the power source to the objective base metal. In general, the inclination of the welding torch was difficult to accurately adjust in the conventional GMAW operation because relative reported contributions were so few. Recently, as there has been fast improvement of the welding process based on robotic operation, online controlling of the inclination can achieve a high accuracy. Hence, in this work, an industrial robot was employed to accurately control the inclination and detailed influence rule of the different modes and values on the formation and characteristics of the weld bead during the pulsed-GMAW process can be seriously examined, in order to improve the GMAW process and obtain weld bead with high quality. To obtain the detailed influence rule, corresponding curve fittings between inclination angles and geometry characteristic parameters were also conducted. Corresponding verification experiments validated the accuracy of the curve fittings. The work is supposed to serve the academic researches of this type of metal joining technology, and promote the process improvement in actual industrial production.
|
|
|
Is It Safe to Use Aluminum Foil in Cooking? |
Geschrieben von: aop21sd - 29.03.2022, 02:20 - Forum: News
- Keine Antworten
|
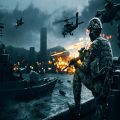 |
Is It Safe to Use Aluminum Foil in Cooking?
The aim of the work was to estimate the degree of aluminum leakage from aluminum foil roll during baking process of selected food/meals. The experiment included 11 different types of food (Atlantic salmon Salmo salar, mackerel Scomber scombrus, duck breasts, cheese Hermelín, tomato, paprika, Carlsbad dumplings, pork roast, pork neck, chicken breasts, and chicken thighs) baked both marinated and not marinated. The aluminum content was measured by AAS and ICP/MS methods. The highest aluminum increase was observed in the samples of marinated Salmo salar (41.86 ± 0.56 mg/kg), Scomber scombrus (49.34 ± 0.44 mg/kg), and duck breast (117.26 ± 1.37 g/kg). The research was also supported by the survey that consisted of 784 respondents with different sociodemographic characteristics. The study clearly showed the occurrence of aluminum contamination of food when it is prepared by baking in aluminum foil. It cannot be concluded that aluminum leakage will occur with each type of food. The aluminum contents found among investigated samples are not alarming, though the increase was measured up to 40 times. On the other hand, revealed aluminum contents can represent a risk for younger/smaller children and for individuals with diagnosed certain ailments.
If you’re baking fish, roasting vegetables or preparing a piece of meat for dinner tonight, chances are that you’ll wrap your food in aluminium foil. What you may not realise is that some of the foil will leach into your meal – and this could be bad for your health.
Research that I conducted with a group of colleagues has explored the use of aluminium for cooking and preparing food. Aluminium doesn’t just appear in foil: it is the most popular cookware material used by people in developing countries. Pots and pans are lined with it and it is found in some kitchen utensils like large serving spoons. Copper used to fulfil this role, but over time it’s been replaced by aluminium because it is cheaper to mass produce and easier to clean.
But while cooking your food in aluminium pots or pans isn’t a bad thing, placing it in foil and putting it in the oven is problematic. This is especially true with acidic or spicy food that’s prepared at high temperatures.
Aluminium and health
Human bodies can excrete small amounts of aluminium very efficiently. This means that minimal exposure to aluminium is not a problem: the World Health Organisation has established a safe daily intake of 40mg per kilogram of body weight per day. So for a person who weighs 60kg the allowable intake would be 2400 mg.
But most people are exposed to and ingest far more than this suggested safe daily intake. Aluminium is present in corn, yellow cheese, salt, herbs, spices and tea. It’s used in cooking utensils, as described above, as well as in pharmacological agents like antacids and antiperspirants. Aluminium sulfate, which is derived from aluminium, is used as a coagulant during the purification process of drinking water.
Scientists are exploring whether over-exposure to aluminium may be posing threats to human health. For instance, high concentrations of aluminium have been detected in the brain tissue of patients with Alzheimer’s disease. Scientists have examined the community of old people with Alzheimer’s and concluded that it is a modern disease that’s developed from altered living conditions associated with society’s industrialisation. These conditions may include high levels of aluminium in daily life.
Aluminium poses other health risks, too. Studies have suggested that high aluminium intake may be harmful to some patients with bone diseases or renal impairment. It also reduces the growth rate of human brain cells.
Avoid foil when cooking
Given all of these proven risks, it’s important to determine the aluminium concentration when cooking. Pots and other cookware tend to be oxidised, providing an inert layer that prevents the aluminium from leaching into food. The problem is that when you scrub your pots after cooking, that layer is worn away and the aluminium can seep into your food. This is easily avoided: when you get new aluminium pots, boil water in them several times until the base becomes matt. This creates a natural oxidation that prevents leaching. They may look nicer when they’re scrubbed and shiny, but a matt base is better for your food and your health.
But cooking your food in foil is a different story. Aluminium foil is disposable and you will not be able to create that inert layer prior to using it. My research found that the migration of aluminium into food during the cooking process of food wrapped in aluminium foil is above the permissible limit set by the World Health Organisation.
Aluminium is significantly more likely to leach into food, and at higher levels, in acidic and liquid food solutions like lemon and tomato juice than in those containing alcohol or salt. Leaching levels climb even more when spice is added to food that’s cooked in aluminium foil. Anything acidic sparks a particularly aggressive process that dissolves layers of aluminium into food.
This research suggests that aluminium foil should not be used for cooking. Instead, we’d recommend using glassware or porcelain when preparing baked dishes. It’s safe to wrap cold food in foil, though not for long stretches of time because food has a shelf life and because aluminium in the foil will begin to leach into the food depending on ingredients like spices.
Americans have been using non-stick aluminum foil roll for over 100 years, since it was first used to wrap Life Savers, candy bars, and gum. For many years up to today, we’ve mostly used it in our kitchens, to bake fish or roast vegetables on the barbecue, to line baking pans, and to trap steam when cooking.
And experts have expressed concern about just how much of it we’re using, with studies even warning that it could have some seriously harmful health effects. Do those warnings have any merit? For more facts about household aluminum foil, here’s why it has a shiny and a dull side.
Potential dangers of aluminum foil
According to research, some of the foil used in cooking, baking, and grilling leaches into your food, which can pose health problems over time. Scientists have been looking at the potential threat that overexposure to aluminum may have on human health for years. For example, researchers have found high concentrations of aluminum in the brain tissue of patients with Alzheimer’s disease. Studies have also found that high aluminum intake may be linked to a reduction in the growth rate of human cells, and may be potentially harmful for patients with bone diseases or renal impairment.
It depends on the food and the temperature
Research has generally found that a couple of factors make aluminum more likely to leach into your food. One of these is the temperature: The higher the temperature you’re cooking at, the more conducive the environment is for aluminum to enter your food, an Electrochem. Sci. study found.
Aluminum foil is a thin-rolled sheet of alloyed aluminum varying in thickness from about 4–150 μm. It was first produced commercially in the US in 1913 where it was used for wrapping Life Savers™, candy bars and chewing gum. In 1921, it was laminated on paperboard to produce coated folding cartons. Household foil was marketed in the late 1920s, and the first heat-sealable foil was developed in 1938. Formed or semirigid containers appeared on the market in 1949. Today foil has been replaced in many applications by metalized films.
Aluminium foil is widely used to seal yoghurt containers (e.g. plastic cups) and owing to the acidic nature of yoghurt and the necessity of heat sealing, the aluminium foil is normally coated with a layer of plastic. If the preformed type of plastic cup is used, the aluminium foil lids are usually precut and around 2500–3000 lids are packed into a special magazine to minimise mechanical damage. The diameter of these lids is <100 mm, and they usually have a pull-tab for easy opening.
The gauge of the foil is around 40 μm, and each lid is normally embossed. The embossing pattern can be varied to suit the customer's requirements and the impression can be up to 100 μm in depth. The embossing is essential to facilitate easy pickup of single lids from the magazine assembly prior to placing over the filled cup and heat sealing.
For yoghurt packaged using the form-fill-seal technique, the aluminium foil is delivered to the dairy as a reel, with the width of the reel being varied in relation to the number of filling heads (abreast) on the packaging machine. The aluminium foil (gauge around 40 μm) is similar to that of the precut type, but the embossing process is omitted since it would serve no function.
Shielding is achieved by incorporating restaurant aluminum foil (typically 0.02–0.03 mm thick), as part of the container. For example, for a frozen meal in a multicompartment tray, it is possible to place ice cream in a totally shielded compartment of the tray—surrounded by aluminum foil—and keep it frozen while the rest of the frozen meal is heated by microwaves. It is also possible to place aluminum foil around portions of the tray to prevent overheating of the corners, sides, or edges of the food.
While the use of shields was originally accomplished by adhering aluminum patches to the surface of trays, a company in the Netherlands, Shieltronics, B.V., has developed a patented procedure that embeds the aluminum within the polyethylene or other plastic tray. In this way, the amount of microwave energy applied to a food component or components will be optimized to provide the optimal temperature for that component. For example, it would be possible to heat a protein, such as fish, with a vegetable, such as potato, and a salad at the same time, with the salad surrounded by the aluminum so it remains cold, while the microwaves are heating the other components.
Overlaying the packages means use of aluminium foil to plastic film or paper to enhance obstruction properties. The application is encouraged by thin checks. Even if plastic covers empower warm sealability, it does not mean that the seal will totally bar dampness and air. Because aluminum packages are more expensive, they are frequently used to package high esteem foods, like: dried soups, herbs, or flavors. A less expensive option to overlaid packaging is metallized film. Metallized films are made of plastic, covered with a thin layer of aluminum metal (Fellows and Axtell, 2002). These films have improved hindrance properties to dampness, oils, scents, and air, the intelligent surface of the aluminum being appreciated by customers. More adaptable than overlaid films, metallized films are basically used to package snacks. Taking into account that the individual components of covers and metallized films are recyclable, from the financial point of view, the worry lies in arranging and isolating the material blocks for reuse.
Meat can be wrapped tightly in professional foil to retain steam as effectively as a covered pan. Bramblett et al., (1959) compared two oven temperatures, 63 and 68°C, for heating of foil-wrapped muscles from beef round. The lower temperature produced the more tender, juicy meat. Beef roasts cooked in foil may have a steamed flavor (Blaker et al., 1959). Baity et al., (1969) reported that at a low oven temperature (93°C), beef loaves cooked more rapidly when foil was tightly sealed than when the loaves were not wrapped or loosely wrapped. At a higher temperature (232°C), cooking times increased with foil wraps. Quality attributes of the loaves were not discussed.
Polyester cooking films and bags are also available for use in the heating of meat. Results of studies of the quality of meat prepared in these films and bags suggest that the quality is comparable to that of meat heated in foil. Beef top round roasts heated in bags to 80°C in ovens at 177 and 205°C took less time but had greater cooking losses than the roasts heated similarly but without bags (Shaffer et al., 1973).
|
|
|
Earring |
Geschrieben von: aop21sd - 29.03.2022, 02:19 - Forum: News
- Keine Antworten
|
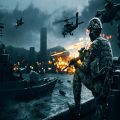 |
Earring
In the Orient, earrings historically were worn by both sexes; in the West (including ancient Israel and Egypt) as a general rule, they were considered to be exclusively female ornaments. Among the Greeks and Romans earrings were worn only by women, and the practice of men wearing them often is spoken of in classical literature as a distinctly Oriental (i.e., Middle Eastern) trait.
In the tombs of the Greek settlers on the Crimean Peninsula (4th century BC), earrings of marvelous complexity and beauty were found. Jewels of the same class, of exquisite beauty and workmanship, were found in the sepulchres of ancient Etruria. Earrings of comparatively simple forms, but set with pearls and other stones, were the mode in Rome.
In Europe, earrings tended to go out of fashion when the wig, coiffure, or headdress obscured the ears, as in the late 17th and 18th centuries. Use of these ornaments continued to be unfashionable in Europe and the Americas during the 19th century but were revived again in the 20th, especially with the introduction of clipping devices. Simplified painless methods of piercing the ears led to the renewed popularity of silver cup chain earring with rhinestone.
Party season may be looking very different this year, but that is no reason not to go all out on your look with a pair of statement earrings. Adding a little sparkle goes a long way: take Shrimps’s black beaded pair, or perhaps Anissa Kermiche’s statement pearl drops, both of which are guaranteed to confer polish on any outfit. From statement styles in gold and silver to crystal, black, coloured and pearl embellished pairs, here is British Vogue’s edit of the best shoulder-sweeping statement earrings to buy now.
Gold Statement Earrings
If you’re looking to invest in a pair of luxe statement earrings, gold is probably your go-to. Enjoying a resurgence in recent, more maximalist seasons, this go-big-or-go-home trend can transform a plain white T-shirt into an evening-appropriate style. Look to Laura Lombardi and Gucci for pointers.
While gold might be the preferred choice for some, layerd triangle earring pack an equally stylish punch. A firm favourite on the red carpet, with the A-list continually choosing diamond-encrusted platinum, white gold or silver statement earrings or ear cuffs to bring their gowns to life, Vogue editors are also partial to some gentle mixing of gold and silver, courtesy of Spinelli Kilcollin.
Earrings are an important part of every woman�s wardrobe, whether we are headed for a day at the beach, to the office, or to a wedding. Your earrings give a subtle hint about your personality.
You can change the entire look and feel of your wardrobe by adding the right earrings. You can bring out your softer feminine side, the sexy goddess, or present simple charm, sophistication, or elegance. For both men and women, today earrings are a definite fashion statement.
Earrings have been a part of human culture since 3000 BC. In past times, earrings actually established your position in society, because only royalty and very wealthy were able to afford expensive jewelry. Fine jewelry was worn by only the wealthy. The rest of the population also wore earrings to decorate their body, but they were replicas of high society jewelry.
There are many styles of earrings. There are quite literally thousands of choices. There is an earring style for every personality. Fine jewelry remains popular with precious stones such as sapphire and emeralds. Semi precious stones are also very popular. But even more popular are the costume jewelry earrings. These are affordable, look great, and are great for staying trendy and in style.
Earrings are one of the most popular forms of jewellery around, worn with pride by women and some men alike. But picking the right rose gold earring with rhinestone is about more than just your mood, your outfit, or the event you are going to; they also have to go with your face shape, skin colour, eyes and hair…your choice of what you put in your ears can transform or ruin your look. Earrings vary in length, size, type of fastening, the materials used, so I would suggest you get stuck in because there are plenty to choose from!
Ear studs have been a familiar, even ubiquitous, sight on people’s faces since the start of the 20th Century. The key feature of this type of jewellery is a precious or semi-precious stone, an enamel or metal design, fixed tightly to the earlobe. The shape can be chosen to suit your personal preference: geometric, conceptual, animals, stars…and if you have already exhausted all the styles on offer, why not trying mixing two studs from different pairs?
A fun set of long, shimmering drop earrings can magically transform any woman’s look, elongating the face, lending it femininity, grace and an aristocratic air. Earrings of this type can be long, short, slender or chunky – the main thing is to be sure to pick out the style that suits you best.
Chandelier earrings differ slightly from drop earrings, and not just in name. Narrow at the point of the earlobe, ballooning out below, it is unsurprisingly their similarity to multi-layered decorative chandeliers that gives them their title. Their large size, relative length and complex design – a sophisticated interweaving of multiple precious stones (or even feathers) – coupled with their striking look, cannot fail to draw attention to any girl’s face. The wow factor means they are usually considered to amount to a full set of evening jewellery in and of themselves, so you need to pick carefully if you want to wear them with other jewellery.
Hoop earrings, also known as Congo earrings, are probably the first earring invented by man. Earrings in this category vary but are all united by their signature shape. You can find all sorts of different looks, with different diameters, materials and styles, from cute miniature ringlets to gigantic hoops that go down to your shoulders for the real socialites. Creole earrings, which come in a half moon shape, are another variety of these earrings.
Cluster earrings are similar to stud earrings in the way they fasten to your ear; they differ on the exterior side in that they feature a number of precious stones in a single enchanting composition. The stones used can vary in shape, size and colour, and they can even include decorative pattern elements or dangling parts.
These earrings snuck onto the jewellery scene from the fashion world just a couple of years ago and represent the logical continuation of the ear cuff. The quirk of ear climbers is their long design, which makes it look like the earring is climbing up the earlobe, usually no higher than the helix (halfway up the ear). To give them their full name, they are called earclimber cirle and square stud earring.
This is the name for the type of earring which covers the bulk of the ear from the lobe to the top, running up the edge of the ear. They are often combined with earrings but they also come without any hanging attachment, simply worn on their own. Ear cuffs are a fashion accessory which reinvents itself from season to season, which means they come in all sorts of shapes and sizes, covering the whole ear, half the ear or as small rings fixed solely to the top.
Twenty years ago, a charm bracelet was the go-to jewel to express your personality and tell your life story in precious, miniature form. Indeed, charm bracelets have a rich and deep history, dating back as far as 400 BC. More recently, in the 19th century, they were widely popularized by Queen Victoria, during the mourning of her husband Prince Albert. And in the 20th century, they became a stalwart of every baby boomer’s jewelry box during the ’50s and ’60s.
My own jewelry box is populated by pieces passed down by my two grandmothers. I can still talk through their every trinket, listing its provenance and significance for two of the most important women in my life – from a tiny silver refrigerator to a miniature squirrel. Today, however, there is a new, more modern canvas for self-expression: a curation of single earrings, each judiciously selected to bear its own meaning.
The premise is very much the same – start with one single, symbolic earring and build your story from there. Your first step could be as simple as selecting an amulet-inspired stud infused with talismanic symbolism. Case in point: the Latin translation of Foundrae’s ‘Per Aspera Ad Astra’ earring means ‘through challenges to the stars’, and the design features three glittering gold stars to represent energy and divine guidance. Ole Lynggaard Copenhagen, meanwhile, has drawn upon a gleaming snake – also a signature motif of the maison – to create a striking single earring that creeps up the ear lobe. Snakes are widely considered a symbol of protection, healing, and rebirth, offering the perfect choice to represent a new life chapter, reward resilience or celebrate a conquered challenge.
“I was one of the first brands to sell single earrings,” says New York-based designer Maria Tash. “In the early 1990s this was unusual, but it spoke to the freedom of not having to adhere to old jewelry traditions of matching sets and displays,” she explains. “Now, there are no more societal rules for symmetry and matching both ears; each piercing is its own autonomous vehicle for adornment.” Tash certainly gives her devotees plenty of choice; with single-earring options that sit upon nine different locations of the ear, customers can select single studs, huggies or hoops that blend harmoniously with the rest of your ear stack.
“If it speaks to you, it works,” says Sophie Bille Brahe, who has similarly gained a cult following for her effortlessly chic single earrings. The first single earring that Bille Brahe launched was her ‘Croissant de Lune’ – a row of graduating diamonds that ascend the lobe – but the Danish designer now offers a full range of diamond and pearl single-earring styles to select from. Her ‘Splash’ designs are perfect for symbolizing oceans crossed, for example, or provide a reminder to go with the flow while they seamlessly blend into your everyday jewelry arsenal.
“Single earrings are really popular with the stacking trend that we have been seeing for the past few seasons, as customers like to have the option to mix and match and buy just one earring if they have more piercings on one ear,” agrees Edwina Hilton, fine jewelry and watches buyer at NET-A-PORTER. Those seeking meaningful styles to stack up should look to Jacquie Aiche’s abalone shell and feather design, with feathers remaining a popular choice for remembering lost loved ones or acknowledging the presence of angels. Elsewhere, Yvonne Léon’s vibrant palm trees are the perfect reminder of exotic adventures, while Alison Lou’s wide selection of single earrings – which include alphabet studs and ‘Mama’ huggies as well as quirkier pretzel-, emoji- or baguette-inspired designs – offer wide artistic license. Everyone has their own interpretation of eccentric motifs, and no two ear stacks will tell the same story.
However, if selecting a smattering of small studs feels labor intensive, single-earring stories can be just as impactful with one principal protagonist. Cue Diane Kordas’s diamond Star collection, which is the ideal self-purchase to symbolize success, particularly the largest and unapologetically glamorous design – now one of her bestsellers. “Single earrings are a really fun way to be creative and let loose,” explains Kordas. “I like to mix all shapes and length – long, short, medium – as long as the scale of the earrings complement each other [it works],” says the New-York born, London-based designer. “It absolutely allows you to show your individuality,” she explains. The best bit about writing your life story in diamonds and gems? “These days, there are no rules,” she quips.
|
|
|
How Water Slides Work |
Geschrieben von: aop21sd - 29.03.2022, 02:10 - Forum: News
- Keine Antworten
|
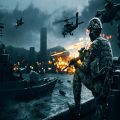 |
How Water Slides Work
In the amusement park industry, the is king. But during the hot summer months, these classic attractions get some tough competition from inflatable slide. In the past 30 years, the world of slides has exploded. They've transformed from simple poolside slopes to intricate attractions that dominate entire parks. According to the World Waterpark Association, there are more than 1,000 water parks in North America, and about 78 million people visited them in the summer of 2006.
Water parks boast slides with dozens of loops, incredible speeds and exhilarating drops. The inflatable dry slide on record is the 120-foot (37-meter) "Summit Plummet" in Walt Disney World's Blizzard Beach. If you'd rather ride down on a raft, you can take a plunge on the similarly record-breaking "Insane," an 11-story-tall water slide in Brazil [source: World Waterpark Association]. Whether you're on a mat, a raft or your bare skin, you're at the mercy of gravity as you make your way down -- and sometimes up -- the slippery slope.
A water slide is like a wet roller coaster with no seat and no safety harness, and it uses the same principles a roller coaster does to work. In this article, we'll peek behind the scenes to find out what's involved in operating a water slide, from pumping the water to cleaning it after the ride. We'll also see how the pieces of a water slide fit together and find out what keeps you from flying off into the air as you whip around corners.
At its most basic level, a water slide is a relatively tame roller coaster with no track and no car. If you've read , then you know that coaster cars are driven by .
At the beginning of the ride, the coaster car is pulled up the . As the coaster rises higher in the air, its potential energy, or energy of position, increases. Simply put, it has farther to fall. When the coaster is released at the top of the hill, gravity pulls it down the track, converting potential energy to kinetic energy, or energy of motion.
slides work on exactly the same principle. But instead of a lift hill, you have a stairway. Climbing the stairs builds up a certain amount of potential energy, which turns into kinetic energy as you head down the slide. A taller slide has more potential energy to work with than a shorter slide.
On the inflatable water slide, your body, sometimes combined with a mat or raft, takes the place of the roller-coaster car. Coaster cars have wheels that roll along the track. This reduces the friction between the car and the track, so the car can keep moving. Water slides have a constant stream of water flowing from the top to the bottom. The water lubricates the slide to reduce the friction between the slide and your body.
Apart from total height, the main difference between particular water slides is the way they put the potential energy to work. This is determined by the shape of the slide. We'll look at how a slide's shape affects how fast you fly and how far you move in the next section.
The slide applies a force working against . The balance of these two forces depends on the angle of the slide. When you are sliding along on a nearly level slope, gravity pulls you directly into the slide, and the slide pushes you upward. The upward force of the slide pushes nearly opposite the downward force of gravity, slowing your downward acceleration. When the slope drops sharply, gravity is still pulling you straight down, but the slanted slide is no longer pushing you straight up; it's pushing you at an angle between upward and forward. Since the slide isn't working directly against gravity, you accelerate downward more rapidly.
Speed slides and sled slides focus only on these up-and-down forces. On a speed slide, you plummet straight down a steep slope and launch into an exit flume, a long canal of that slows you down gradually. In a sled slide (also called a toboggan slide), you glide over a series of bumps and dips. In both of these slide designs, you move forward in a straight line.
A small slide, the sort you might find in somebody's backyard, has a very simple construction. It's a single piece of smooth fiberglass material, cast in the shape of a slide, supported by a metal frame.
Most panda inflatable dry slide have a similar structure, but on a much larger scale. Obviously, it's not feasible to use a single piece of fiberglass for a giant, curving slide. Water park slides are formed from dozens of fiberglass segments fastened together with heavy-duty bolts. Typically, the individual segments fit together like sections of a toy race track.
Each segment has one end with a raised lip and one end with a sunken step. When you fit two segments together, the lip of segment A rests on the step of segment B. This ensures that the segments hold together, with a smooth seam between them. Ideally, the slide feels like a single unit to the rider. Slides typically use completely enclosed tubes for the sharpest turns, to make sure everyone stays in.
These segments rest on a framework of steel girders. The girders may be positioned directly below the slide, or they may sit adjacent to the slide, supporting it with sturdy cantilevers.
Water parks generally buy new slides from an outside manufacturer. The manufacturer designs the slide and builds all of the individual pieces. The water park hires a local contractor to take these pieces and put the whole thing together according to the manufacturer's directions. It's just like building a toy race track or model train, but on a massive scale. The robot inflatable dry slide structure is only half of the ride, of course. Next, we'll take a look at how water lets you slip from the top to the bottom.
In order to zip down the slide, you need a constant stream of to reduce friction between you and the fiberglass surface. To maintain this stream, the water park has to get a supply of water to the top of the slide. Most water slides do this with a pump, housed in a building near the base of the slide. In the standard design, the pump motor turns a drive shaft, which is attached to a propeller. The spinning propeller drives water forward, in the same way an moves air particles.
The pump draws water from a collection , typically the pool at the base of the slide, and pushes it up through a narrow pipe to the top of the slide. In this way, the water running down the slide is constantly recycled. In some parks, the water is cycled through several connected pools before it is pumped back up to the top of a slide.
Inflatable bouncers or moon bouncers have grown in popularity over the recent years as they are relatively cheap to acquire,1 provide a source of entertainment for children and are generally regarded as a safe environment by parents. There are multiple descriptors for inflatable bouncers, including inflatable play structure, bounce house, bouncer and bouncy castle. They are encountered at fairs, festivals and amusement parks as well as at private parties. Restaurants, inns and even hotels, try to attract families with the installation of leisure games for minors, such as playgrounds with various attractions so that the little ones can have fun while adults enjoy a relaxed after-dinner or family celebration. In this respect, the bouncers are an ideal complement for parties and ensure hours of fun at low cost.
However, as their demand has soared, so have accident rates.2,3 In recent years, there has been a significant increase in the number of children treated in the emergency department (ED) for injuries resulting from the use of these devices (in the United States an injury rate of 5.3/100 000 children has been described).1
The mechanisms of injuries were: first, a fall, both inside and outside of the bouncy castle; second, a collision between children due to the differences in sizes and ages.4–6 Also, less frequently yet more severe, were injuries resulting from faults in the anchoring system and wind gusts.7
The main risk factor was the lack of effective adult supervision, either by the parent or staff responsible for overseeing the attraction. Furthermore, overcrowding by children of different weights and sizes increased exponentially the chances of suffering an accident.8
We carried out a prospective study of injuries secondary to inflatable play structure accidents that attended the Paediatric Emergency Department at our Hospital Universitario Son Espases. This is the first prospective European study of its kind, which has been conducted in a single referral centre for Paediatric Orthopaedics during a 12-month period (between February 2015 and February 2016). Our hospital is a paediatric referral site for the entire province; patients not only come from the city but from all the municipalities of the province. The population of the province is 1 169 591 inhabitants, with a population proportion corresponding to the age range of 0 to 14 years of 15% (Fig. 1).
The increase of inflatable play-related injuries may be explained by the growth of the inflatables industry,8 as well as by the lack of prevention measures and initiatives for reducing injury risks.
The aim of this study is to describe the epidemiology, type and chronology of the lesions and ultimately, we would like to outline some safety guidelines for inflatable attractions and alert civil society to the dangers of such facilities, still considered safe by the general public.
Only paediatric patients aged 0 to 14 years, who had experienced trauma in an inflatable play structure, were chosen for the study.
The patients’ parents were informed at arrival to the ED about the study, and they consented to and signed the protocol for data collection.
Demographic data gathered included: age; gender; mechanism of injury (fall inside the inflatable play structure, fall outside the bounce house, collision with another participant, castle displacement); risk factors (lack of responsible supervision, users of different ages); type of injury; medical attention required; and complementary tests.
Adult supervision is defined as the need for vigilance at all times. There must be at least two people supervising the attraction.
The shifts should be respected, either by age, or by height, so that children of different constitution do not use attraction at the same time. The simultaneous use by a large number of people at the same time should be avoided, because it increases the danger of falls and injuries, especially if children of different age ranges and weight are mixed.
|
|
|
What is a Seamless Steel Pipe? |
Geschrieben von: aop21sd - 29.03.2022, 02:09 - Forum: News
- Keine Antworten
|
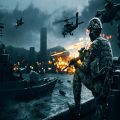 |
What is a Seamless Steel Pipe?
Seamless steel pipes are perforated from whole round steel, and steel pipes without welds on the surface are called seamless steel pipes. According to the production method, seamless steel pipes can be divided into hot-rolled seamless steel pipes, cold-rolled seamless steel pipes, cold-drawn seamless steel pipes, extruded seamless steel pipes, and top pipes. According to the cross-sectional shape, seamless steel pipes are divided into two types: round and special-shaped. Special-shaped pipes include square, oval, triangular, hexagonal, melon seed, star, and finned pipes. The maximum diameter is 900mm and the minimum diameter is 4mm. According to different purposes, there are thick-walled seamless steel pipes and thin-walled seamless steel pipes. Seamless steel pipes are mainly used as petroleum geological drilling pipes, cracking pipes for petrochemical industry, boiler pipes, bearing pipes, and high-precision structural steel pipes for automobiles, tractors, and aviation.
API seamless pipe have a hollow section and are used in large quantities as pipelines for transporting fluids, such as pipelines for transporting oil, natural gas, gas, water and certain solid materials. Compared with solid steel such as round steel, steel pipe is lighter in flexural and torsional strength and is an economical section steel. Widely used in the manufacture of structural parts and mechanical parts, such as oil drill pipes, automobile transmission shafts, bicycle frames, and steel scaffolding used in construction. Steel pipes are used to make ring parts, which can improve material utilization, simplify manufacturing procedures, and save materials and processing. Working hours.
A seamless steel pipe is a circular pipe having a hollow section and no seams around it. The ASTM seamless pipe is made of carbon steel, alloy steel, stainless steel ingot or solid tube blank, and then is made by hot rolling, cold rolling or cold drawing. Seamless pipes are considered superior to welded pipes as they are built using monolithic steel billets, with intrinsic mechanical strength, without seam welds.
What is a seamless steel pipe?
A seamless steel pipe is a circular pipe having a hollow section and no seams around it. The seamless steel pipe is made of carbon steel, alloy steel, stainless steel ingot or solid tube blank, and then is made by hot rolling, cold rolling or cold drawing. Seamless pipes are considered superior to welded pipes as they are built using monolithic steel billets, with intrinsic mechanical strength, without seam welds.
Characteristics of seamless steel pipe
Seamless steel pipe for the use of engineering and construction is very widely, it is a hollow steel strip no seams, it is mainly used to transport liquids pipelines, different look and general steel,one of those heavy type steel, it has a strong resistance to corrosion, resistant to general corrosion.
Will not rust, this performance makes seamless steel tubes extend the life, the most important is that it is very clean and no toxins.
Compared with other plastic seamless steel pipe having strong mechanical resistance, impact regardless of how high a temperature is not interested in the use of seamless steel pipe, it is mounted and the other pipe is the same, can replace other piped water and other liquids.
Since the industrial applications have become complex and evolved a lot, the piping products are also changing to stay in the race. Although there are many pipe processing techniques, the industry's most influential controversy between electrical resistance welded and spiral steel pipe.
As they are produced, some seamless pipe types harden, so heat treatment after production is not needed. Others need thermal therapy. Consult the seamless pipe form specification you are considering to learn if heat treatment would be needed.
As alternatives today, ERW and seamless steel piping remain primarily due to historical beliefs.
Generally, since a weld seam was used, the welded pipe was deemed inherently weaker. This supposed design weakness was absent from the seamless pipe and was deemed safer. Although it is true that welded pipe has a seam that makes it technically weaker, manufacturing processes and quality assurance regimes have all advanced to the degree that when its tolerances are not exceeded, welded pipe can work as expected. While the obvious benefit is apparent, a criticism of seamless piping is that, compared to the more reliable thickness of steel sheets intended for welding, the rolling and stretching process creates an inconsistent wall thickness.
These perceptions are still expressed by the industry standards that regulate the production and specification of ERW and seamless steel pipes. For example, for many high-pressure, high-temperature applications in the oil & gas, power generation and pharmaceutical industries, seamless piping is needed. Welded piping (which is typically cheaper to manufacture and is more commonly available) is defined in all industries as long as the parameters noted in the relevant specification do not exceed the temperature, pressure and other service variables.
There's no difference in efficiency between ERW and pile pipe in structural applications. Although the two can be interchangeably defined, since cheaper welded pipe works just as well, it does not make sense to specify for seamless.
Healthy welded and seamless steel pipe buying procedure
As piping products are listed for a project, an important note to be made is that the specification books (such as those supplied by ASTM, ASME, ANSI and API, among others) that engineers use to direct the specifications they write only list pipe grades exclusive of referencing whether they are generated through ERW or seamless pipe production. By both ways, not all grades can be made.
For example, if an engineer defines welded pipes with a wide outside diameter and wall thickness without understanding that it would be difficult to produce them, a potential mix-up could occur. Until a purchase order is placed, this mistake would possibly go unnoticed, at which point an industrial pipe supplier would tell the customer that the order could not be fulfilled as written. See us at International Pipe Suppliers for the supply.
The development of numerical simulations is potentially useful in predicting the most suitable manufacturing processes and ultimately improving product quality. Seamless pipes are manufactured by a rotary piercing process in which round billets (workpiece) are fed between two rolls and pierced by a stationary plug. During this process, the material undergoes severe deformation which renders it impractical to be modelled and analysed with conventional finite element methods. In this paper, three-dimensional numerical simulations of the piercing process are performed with an arbitrary Lagrangian–Eulerian (ALE) formulation in LS-DYNA software. Details about the material model as well as the elements’ formulations are elaborated here, and mesh sensitivity analysis was performed. The results of the numerical simulations are in good agreement with experimental data found in the literature and the validity of the analysis method is confirmed. The effects of varying workpiece velocity, process temperature, and wall thickness on the maximum stress levels of the product material/pipes are investigated by performing simulations of sixty scenarios. Three-dimensional surface plots are generated which can be utilized to predict the maximum stress value at any given combination of the three parameters.
Metal pipes are categorized into welded pipes and seamless pipes. Welded pipes are commonly manufactured by bending and welding metal sheets, while seamless pipes are produced using the rotary piercing process. It is well recognized that seamless pipe provides more benefits than welded pipe, such as (1) increased pressure ratings; (2) uniformity of geometry, material properties, and matter; and (3) structural strength and fatigue capacities under load. Offshore industry especially requires over 30–40 years of design life and robust design of the piping system, pipeline, and riser structures are requested by adopting reliable materials, manufacturing processes, installation, and operation. Many benefits of seamless pipe, i.e., uniformity of shape and fatigue and strength capacity, allow for higher safety during the operation period of offshore pipeline [1,2,3] and riser structures [4,5,6] from repeated environmental loadings [7,8].
In the rotary piercing process, a heated round billet is fed into a plug by the action of two skewed rolls which rotate in the same direction. The rolls are tilted and placed on opposite sides of the workpiece, providing both rotation and translation to the workpiece. As mentioned by Komori [9], the rolls can be barrel-shaped or cone-shaped. Since the invention of the piercing process over a century ago, numerous empirical and analytical studies have been conducted and one of the good reviews have been conducted by Komori and Mizuno [10]. Experimental studies on cone-shaped-type rotary piercing using lead and wax were performed and a comparison was drawn between two-roll and three-roll cone systems. It was shown that the three-roll cone systems are superior to that of two-roll systems by Khudeyer et al. [11]. The effects of varying the feed angle on the shear strain were studied experimentally using hot steel. Hayashi and Yamakawa [12] found that with larger cross angles, the decrease in the circumferential shear strain is more significant. Moon et al. [13] and Sutcliffe and Rayner [14] conducted experimental work on the rolling process using modelling clay (Plasticine) due to the similarities of its stress–strain behaviour with that of metals and because of its malleability and low cost.
Finite element analysis (FEA) of metal forming processes was further performed to gather the necessary information to design and control these processes properly. In addition, the number of experimental trials can be minimized through the exploitation of FEA, which would significantly reduce the product development lead time. Moreover, with the decrease of experimental work, the overall development cost of the product would be reduced. Nowadays, the advancement of powerful computer technology enables the numerical simulations to consider various physical phenomena during metal processing which include deformation, heat transfer, phase transformation, and ductile fracture [15,16,17].
A two-dimensional rigid-plastic finite element simulation of rotary piercing was performed by Mori et al. [18]. However, the accuracy of the results was low since generalized plane strain was assumed from the simulation. Three-dimensional rigid-plastic finite element analysis was performed by Komori [9]. The number of the elements was limited, and the mesh was relatively coarse because large amounts of computational time were required. Berazategui et al. [19] used the pseudo-concentrations technique to conduct three-dimensional rigid-viscoplastic finite element simulations and a new algorithm was proposed to describe the contact boundary conditions between the tools and the blank. The algorithm was validated with industrial tests of the barrel-type rotary piercing process. However, the numerical analysis of the process was found to be complicated and the computational cost was rather large. Thus, an alternative simplified method was highly required [10]. Shim et al. [20] used a rigid-thermo-viscoplastic finite element method and conducted simulations with AFDEX 3D software to predict the final shape in better detail. Intelligent re-meshing and tetrahedral elements were used which resulted in increased computational cost. The same method was then used to conduct numerical studies on the Mannesmann effect in the piercing process, as well as to compare between the Diescher’s guiding disk and Stiefel’s guiding shoe [21,22].
Lee et al. [23] presented a novel method for adaptive tetrahedral element generation for precision simulation of moving boundary problems such as bulk metal forming. The effects of using tetrahedral solid elements were investigated in a three-dimensional simulation of the forging process with an AFDEX 3D forging simulator. The predictions of both tetrahedral and standard hexahedral elements were in good agreement with experimental data provided that the remeshing technique is employed by Lee et al. [24]. Pater and Kazanacki [25] used Simufact Forming software to analyze the effects of the plug diameter, plug advance, and feed angle on the piercing process. The influence of different plug shapes was further investigated by Skripalenko et al. [26]. ProCAST and QForm commercial software were used for the numerical simulation of piercing aluminium alloy. Jung et al. [27] conducted 3D numerical simulations on the elongation rolling process to study how the rolling speed (rpm) and distance of guide shoes influenced the outer diameter and thickness of the pipe. MSC-SuperForm software was used and an automatic re-meshing method of hexagonal elements was implemented. Xiong et al. [28] used the reproducing kernel particle method for the steady and non-steady analysis of bulk-forming processes and validated the numerical predictions with experimental measurements. Topa and Shah [29] performed 3D numerical simulations for a forging process with a complex tool geometry using the smooth particle hydrodynamics (SPH) method. The results were in fair agreement with experimental data, but the method had a poor visual representation of the final geometry. Hah and Youn [30] presented an effective Eulerian approach for bulk metal forming based on representing boundaries as non-uniform rational B-spline (NURBS) and the effectiveness of the proposed approach was demonstrated by comparing with other numerical methods. However, this approach had the drawback of a blurred boundary condition imposition.
The tools are assumed to be rigid parts as their deformation is insignificant and out of the scope in the current study. They are modelled with shell elements to minimize computational cost. Material model 24 (Piecewise Linear Plasticity) was used to model the Plasticine material behaviour. In this model, the stress–strain curve of the material can be imported to the keyword file to define the relationship between stress and strain. Multiple curves at different strain rates can be used to take into consideration the strain rates’ effects via the stress yield scaling method. Large deformation will cause an increase in the temperature and thermal softening. However, due to the high velocity of the process, it was assumed that changes to temperature were minimal and there was insufficient time for heat transfer to occur between the workpiece and the tools. Thus, the process is simplified to an isothermal system.
|
|
|
What Do We Know So Far on Hair Straightening? |
Geschrieben von: aop21sd - 29.03.2022, 02:07 - Forum: News
- Keine Antworten
|
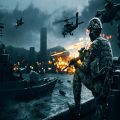 |
What Do We Know So Far on Hair Straightening?
Hair represents a valued aspect of human individuality. The possibility of having an easy to handle hairstyle and changing it from time to time promoted an increasing search for chemical hair transformations, including hair straightening. Hair straightening is the process used to convert curly into straight hair. The desire for straight hair used to be associated with the standards of the “universal beauty.” Currently, the preference for this style is more for the ease of handling and the simpler daily care routine [1]. Straightening may be physical or chemical processes and temporary or permanent, regarding its duration.
We performed a literature search in the scientific database MEDLINE through PubMed until July 15, 2020, using the terms “straightening” AND “hair” (125 results), “straightening” AND “alopecia” (22 results), and “straightening” AND “human hair” (103 results). We limited the search to articles available in English and considered those mentioning alternatives to straighten the hair. After excluding duplicate titles, we had a total of 33 relevant articles.
Anatomically, the hair shaft has 3 layers: cuticle, cortex, and medulla [2, 3]. The outermost part is the cuticle, which is composed of keratin and consists of layers of scales overlapping 1 and other, just like tiles on a roof. The cuticle protects the underlying cortex and acts as a barrier [3-5]. The normal, undamaged cuticle has 6–8 layers according to the ethnicity, a smooth surface, allowing reflection of light and limiting friction between shafts [5]. The outer surface of the cuticle’s scale cells is coated by a thin membrane, the epicuticle, and each cuticle cell consists of 3 layers of protein: the A-layer, a resistant layer with high cystine content; the exocuticle, also rich in cystine; and the endocuticle, low in cystine content. The cortex accounts for most of the hair shaft and is responsible for the hair. The cortex is comprised of microfibrils, long filaments oriented parallel to the axis of the fiber. Each microfibril consists of keratin intermediate filaments, also known as microfibrils, and the matrix, constituted by keratin-associated proteins [4]. It is the thickest layer located around the medulla, which is the innermost part of the hair, has melanin granules which composition is related to the shades of hair color. It is also responsible for hair volume, the great tensile strength, and mechanical resistance of the shaft, as it contains the most part of keratin [3-5].
The primary component of the hair fiber is keratin. The remaining constituents are represented by other proteins, water, lipids, pigments, and trace elements. Because of its specific conformation and chemical bonds, keratin is responsible for hair stiffness, strength, and insolubility. Among the amino acids that make up keratin, cystine is one of the most important. Each cystine unit contains 2 cysteine amino acids from different portions of the peptide chains that are connected by 2 sulfur atoms, forming a strong bond named disulfide bridge [3-5]. Another important structural component of the hair shaft is the 18-methyl eicosanoic (18-MEA) acid. It forms a hydrophobic layer that retards water from wetting and penetrating and changing the hair shaft physical’s properties. Removal of the fatty acid layer decreases the brightness of the hair, making it more susceptible to static electricity and frizzing induced by humidity [4].
The spiral shape of the hair is determined by the asymmetric protein expression in the hair follicles [2]. As it is not possible yet to modify the shape of the follicle, the only way to change hair appearance is by modifying its physicochemical properties [6].
This method was developed in the late 19th century and became popular in the early 20th century by Madame C.J. Walker, who combined hot comb with pressing oil. It is a temporary straightening since it changes only weak hydrogen bonds, in a process named keratin hydrolysis. The initial technique was the application of a petrolatum ointment base in the hair, followed by straightening it using a heated metal combing device. Over time, the technique was improved. However, with the introduction of new methods, the hot comb went out of use [1, 5, 7, 8].
Physicochemical techniques combining mechanical and thermal straightening, as hairdryer and flat iron, are temporary solutions that last until the next washing. The hair needs to be wet, so hydrogen bridges break and there is the transitional opening of the helical structure of the shaft, relaxing it. The combined use of the dryer and the flat iron dehydrates the hair, keeping it straight [1].
High temperatures, between 235 and 250°C in the dry hair and 155–160°C in the wet hair, may denature hair shaft proteins [1, 9]. Usually, hairdryers are more harmful to the hair shaft than naturally drying it [9]. However, a study showed that the use of the dryer with continuous movement, at a minimum distance of 15 cm from the hair, could be less damaging than natural drying [10].
Hydroxides are potent alkalis, widely used for straightening very curly hairs [11]. The primary substances of this group and their characteristics are described in Table 1. Sodium hydroxide, also known as lye, is indicated for straightening extremely curly hair. No-lye relaxers, such as guanidine hydroxide, are indicated for straightening wavy to curly hair and for sensitive scalp. Although milder for the scalp, it leaves calcium mineral residues on the hair shaft, making it drier, brittle, and dull [4, 11-14].
STRAIGHTENING MY HAIR is typically a two-day affair. I wash all the product out the night before and load my hair with hydrating protectants. I let it air-dry, then I braid it before bed so that the next day, the curls are looser and easier to work through. Then, and only then, can I go in with a flat iron.
WIRED's Gear members have an array of curl types, needs, and hair-styling tricks, and we've all tried a lot of hair straighteners in our lifetimes. Some flat irons have left us with crispy ends and cramped hands, while others, like the ones listed here, gave us sleek hair. There's a dizzying number of options around, but hopefully our favorite titanium hair straightener can help narrow down your search.
Updated December 2021: We've added more of our favorite tourmaline hair straightener, including the Bio Ionic 3-in-1 tool, the L'ange iron that blows cool air, and two honorable mentions.
Special offer for Gear readers: Get a 1-year subscription to WIRED for $5 ($25 off). This includes unlimited access to WIRED.com and our print magazine (if you'd like). Subscriptions help fund the work we do every day.
Modern technologies have come up with ceramic hair straightener that are user-friendly. You no longer have to visit a salon if you want straight hair. However, using a hair straightener may not be easy for someone who has not used it before. Though flat irons are simple to use, one needs to be aware of the associated factors to ensure safety. If you are a beginner, here is a simple guide on how to use hair straightener at home.
Before you straighten hair at home, you need to prep your hair. Pollution, grease, various styling products, and dirt make your hair frizzy and unmanageable (1). Therefore, you need to wash your hair before straightening it.
Use a hydrating and nourishing shampoo to make your hair soft. Before you apply the flat iron on hair, make sure your hair is dry. Do not use a hair straightener on wet hair.
Choosing the right type of hair straightener is as important as preparing your hair for the straightening method. The market is flooded with plenty of straightening brands, and the abundance of options may end up confusing you. Here Checkout these Hair Straighteners as few options you can consider. Using a bad iron may end up damaging the hair severely.
Among many types of straighteners, flat irons are the best ones. They may be a little expensive compared to other types but are the best in terms of safety. When you are shopping for one, try to pick a straightener that comes with ceramic coating. This type of product is gentle for hair and provides hair with extra shine and health.
Personal image, as it relates to external beauty, has attracted much attention from the cosmetic industry, and capillary aesthetics is a leader in consumption in this area. There is a great diversity of products targeting both the treatment and beautification of hair. Among them, hair straighteners stand out with a high demand by costumers aiming at beauty, social acceptance and ease of daily hair maintenance. However, this kind of treatment affects the chemical structure of keratin and of the hair fibre, bringing up some safety concerns. Moreover, the development of hair is a dynamic and cyclic process, where the duration of growth cycles depends not only on where hair grows, but also on issues such as the individual's age, dietary habits and hormonal factors. Thus, although hair fibres are composed of dead epidermal cells, when they emerge from the scalp, there is a huge variation in natural wave and the response to hair cosmetics. Although it is possible to give the hair a cosmetically favourable appearance through the use of cosmetic products, for good results in any hair treatment, it is essential to understand the mechanisms of the process. Important information, such as the composition and structure of the hair fibres, and the composition of products and techniques available for hair straightening, must be taken into account so that the straightening process can be designed appropriately, avoiding undesirable side effects for hair fibre and for health. This review aims to address the morphology, chemical composition and molecular structure of hair fibres, as well as the products and techniques used for chemical hair relaxing, their potential risk to hair fibre and to health and the legal aspects of their use.
Attempts at beautification, mainly in women, especially involve the skin and its annexes 1. Personal image, as it relates to external beauty, has been the target of investment in the beauty industry, and in this context, the branch of capillary aesthetics has attracted much attention from the cosmetic industry because it is considered a leader in consumption in this area 2. As hair is one of the few physical features that can be easily modified to create a totally different style, be it in length, colour, or shape 3, there is a great diversity of products targeted for both the treatment and the beautification of hair; among them, hair relaxers and straighteners stand out. Generally, the term ‘relaxer’ refers to products intended for the treatment of kinky hair, while ‘straightener’ refers to products used for the treatment of curly hair – in this work, the term ‘straightener’ is used when referring to both products. The reasons for the use of hair dryer include beauty, social acceptance and ease of daily hair maintenance 1. However, these cosmetics affect only the hair shaft. As the newly developing hair will not be affected by these alterations, the new emerging hair will grow with its natural, original shape, and therefore, hair straightening needs to be repeated every 4–6 weeks 3. Thus, the emphasis in this cosmetic treatment should be only on new growth, as repeated treatments can lead to hair breakage 3, and scalp and hair disorders 4, among others 1, 4-6. Moreover, although the hair fibres are composed of dead epidermal cells, when they emerge from the scalp, there is huge variation in natural wave and the response to hair cosmetics 5. Consequently, for obtaining good results, it is essential to understand the mechanism of the process and other important information such as the composition of natural hair fibres, the composition of products and techniques available for hair straightening. Thus, this review aims to address a comprehensive summary of the morphology, chemical composition and molecular structure of hair fibres, as well as the products and techniques used for chemical hair straightening, their potential risk to hair fibre and to health and legal aspects of their use.
|
|
|
Hibiscus syriacus Extract from an Established Cell Culture Stimulates Skin Wound Heal |
Geschrieben von: aop21sd - 29.03.2022, 02:06 - Forum: News
- Keine Antworten
|
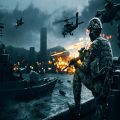 |
Hibiscus syriacus Extract from an Established Cell Culture Stimulates Skin Wound Healing
Higher plants are the source of a wide array of bioactive compounds that support skin integrity and health. Hibiscus syriacus, family Malvaceae, is a plant of Chinese origin known for its antipyretic, anthelmintic, and antifungal properties. The aim of this study was to assess the healing and hydration properties of H. syriacus ethanolic extract (HSEE). We established a cell culture from hibiscus extract and obtained an ethanol soluble extract from cultured cells. The properties of the extract were tested by gene expression and functional analyses on human fibroblast, keratinocytes, and skin explants. HSEE treatment increased the healing potential of fibroblasts and keratinocytes. Specifically, HSEE significantly stimulated fibronectin and collagen synthesis by 16 and 60%, respectively, while fibroblasts contractility was enhanced by 30%. These results were confirmed on skin explants, where HSEE accelerated the wound healing activity in terms of epithelium formation and fibronectin production. Moreover, HSEE increased the expression of genes involved in skin hydration and homeostasis. Specifically, aquaporin 3 and filaggrin genes were enhanced by 20 and 58%, respectively. Our data show that HSEE contains compounds capable of stimulating expression of biomarkers relevant to skin regeneration and hydration thereby counteracting molecular pathways leading to skin damage and aging.
Wound healing is a dynamic physiological process by which the skin regenerates itself upon injury. The restoration of tissue integrity is the result of the interaction between several distinct cellular elements (keratinocytes, fibroblasts, monocytes/macrophages, and endothelial cells) and extracellular matrix (ECM) components, such as fibronectin and collagen whose contraction encourages the edges of the wound to shrink together [1]. The supply of the ideal microenvironment at the wound surface is fundamental for reaching full skin wound's healing potential. Indeed, adverse factors, such as infection, mechanical stress, or toxic agents, can significantly affect the skin ability to heal. Additionally, the process of wound healing is altered in a dry skin and skin of aged individuals [2]. Skin dryness alters the ability of epithelial cells to migrate and cover the wound site and reduces the supply of white blood cells and nutrients, which are essentials to form new tissues and protect skin against infections [3].
Skin hydration depends on the humidity of the environment and the hygroscopic properties of the stratum corneum, the uppermost epidermal layer. The ability of the stratum corneum to retain water relies on the natural moisturizing factor (NMF), a set of substances including ions, small solutes, and free amino acids which are largely formed by the breakdown products of filaggrin protein [4].
Skin care products are often developed from plants. Higher plants are the source of a wide array of biochemicals that can support the health and integrity of the skin and are widely used in cosmetic formulations.
H. syriacus, family Malvaceae, is a plant of Chinese origin already known in Asia for its antipyretic, anthelmintic, and antifungal properties [5]. H. syriacus extract was previously shown to have antioxidant capacity [6] and antiproliferative effects on human lung cancer cells [7]. However, the leaves of hibiscus calyx extract genus are traditionally acclaimed as hair tonic in the Indian system of medicine. Accordingly, topical application of H. syriacus extract was found to stimulate hair growth thereby validating the ethnomedical use of this plants for hair loss treatment [8].
Remarkably, H. rosa-sinensis of the genus hibiscus extract powder was previously reported to efficiently act as wound healing agent by increasing cellular proliferation and collagen synthesis [9]. More recent in vitro and in vivo studies indicated Hibiscus syriacus L. flower absolute (HSF) as a highly effective agent for wound treatment because of its ability to promote keratinocyte proliferation and migration [10].
A chemical study performed on raw material from the epigeal part of the plant revealed the presence of flavonoids [dihydroquercetin, herbacetin, kaempferol, saponaretin, and saponarin] previously demonstrated to be able to reduce UVB-induced erythema and tumorigenesis [11]. Furthermore, H. syriacus extract was also found to be rich in anthocyanins, fatty acids, and several types of pigments [12].
Nowadays, cell suspension cultures from plants provide a viable alternative over whole plant cultivation for the production of secondary metabolites. They represent standardized, contaminant-free, and biosustainable sources of beneficial bioactive compounds for cosmetics on an industrial scale [12, 13].
We have established stem cell suspension cultures of H. syriacus and prepared a hydro/alcoholic extract rich in flavonoids and coumarins. Here, we present a study aimed at evaluating the wound healing and hydration properties of Hibiscus syriacus extract from cell suspension culture.
Since ancient times, Hibiscus. species (Malvaceae) have been used as a folk remedy for the treatment of skin diseases, as an antifertility agent, antiseptic, and carminative. Some compounds isolated from the species, such as flavonoids, phenolic acids, and polysaccharides, are considered responsible for these activities. This review aims to summarize the worldwide reported biological activities and phytoconstituents associated with this genus for the past 40 years.
Hibiscus. (Malvaceae) is a genus of herbs, shrubs, and trees; its 250 species are widely distributed in tropical and subtropical regions of the world. About 40 species occur in India. Many Hibiscus. species are valued as ornamental plants and are cultivated in gardens. Some species, such as Hibiscus cannabinus. L. and Hibiscus sabdariffa. L., are important sources of commercial fiber, whereas some species are useful as food, and yet others are medicinal (Anonymous, 1959). Many species belonging to this genus have been used since ancient times as folk remedies for various disorders. In Ayurveda, Hibiscus esculentus. L. fruits are considered tonic, astringent, and aphrodisiac. In Unani medicine, the fruits are considered emollient and useful for treating urinary disorders (Parrotta, 2001). The leaves and roots of Hibiscus manihot. L. are used as a poultice for boils, sprains, and sores, and the flowers are used to treat chronic bronchitis and toothache. The mucilage of the bark is considered to be an emmenagogue (Chopra et al., 1950). The seeds of Hibiscus abelmoschus. L. are valued for their diuretic, demulcent, and stomachic properties and are considered stimulant, antiseptic, cooling, tonic, carminative, and aphrodisiac. The bark, flowers, and fruits of Hibiscus bauiferus. J.G. Froster are used externally for the treatment of skin diseases such as eczema, scabies, psoriasis, and ringworm. In Ayurvedic medicine, the bark is the official source of the drug “parisha,” a reputed remedy for skin diseases (Parrota, 2001).
According to the literature, many Hibiscus. species have been investigated and found to contain many classes of secondary metabolites, including flavonoids, anthocyanins, terpenoids, steroids, polysaccharides, alkaloids, amino acids, lipids, sesquiterpene, quinones, and naphthalene groups. Some of these compounds have been shown to have antibacterial, anti-inflammatory, antihypertensive, antifertility, hypoglycemic, antifungal, and antioxidative activities (Kholkute et al., 1977a; Parmar & Ghosh, 1978; Gangrade et al., 1979; Jain et al., 1997; Faraji & Tarkhani, 1999; Lin et al., 2003; Sachdewa & Khemani, 2003).
This review describes the currently available chemical and biological data on the genus Hibiscus. and suggests that the flavonoids and phenolic acids are the main classes of substances of interest to a phytochemist and pharmacologist. A number of reports have been published to establish the biological potential of this genus (Table 1).
Canthin-6-one (2) and a fatty acid fraction that contained lauric, myristic, and palmitic acids isolated from stem bark of hibiscus flower extract powder showed antifungal activity against Trichophyton interdigitale. (Yokata et al., 1978). The seed oil of Hibiscus syriacus. has shown antimicrobial activity against Gram-negative and Gram-positive microorganisms. The oil was resistant against Salmonella typhi. but showed activity against Escherichia coli, Salmonella newport, Staphylococcus aureus, Staphylocoecus albus, Bacillus subtilis., and Bacillus anthracis.. The oil has shown significant fungicidal activity against tested plant pathogens, viz., Alternaria solani, Aspergillus niger, Colletotri-chum dematium., and Fusarium oxysporum. (Shah et al., 1988). The oil and the unsaponifiable matter from Hibiscus sabdariffa. were found to exert antibacterial activity against Escherichia coli, Staphylococcus typhimurium, Bacillus anthracis, Bacillus subtilis, Staphylococus aureus, Staphylococcus albus. and Klebsiella pneumoniae.. These compounds also exhibited antifungal activity against Aspergillus flavus, Trichophyton equingea, Helminthosporum rostatum, Crypto-coccus neoformans, Tricnoderm viridi, Colletotrichum falca-tum., and Alternaria solanacea.(Gangrade et al., 1979). The aqueous extract of the calyx of Hibiscus sabdariffa. and protocatechuic acid derived from roselle calyx inhibited effectively the growth of bacterial pathigens, viz., methicillin-resistant Staphylococcus aureus, Klebsiella pneumoniae, Pseudomonas aeruginosa., and Acinetobacter baumannii.. The antibacterial activity of protocatechuic acid was greater than the extract (Lin et al., 2005). The ethanol extract of aerial parts and roots of Hibiscus micranthus. L. showed antibacterial activity against Staphylococcus aureus. and antifungal activity against Fusarium moniliforme, Aspergillus flavus, Aspergillus niger., and Rihzoctonia bataticola.(Jain et al., 1997).
The trinorcandalene phytoalexins, hibiscanal (3) and o.-hibiscanone (4) isolated from stem stele of hibiscus sabdariffa extract. inoculated with fungal pathogen Verticillium dahliae. killed all propagules of Verticillium dahliae. in the concentration range of 1–18 μg/mL (Bell et al., 1998). The volatile oil from the leaves of Hibiscus cannabinus., composed of 58 components of which the major components were (E.)-phytol, (Z)-phytol, n.-nonanol, benzene acetaldehyde, (E.)-2-hexenal, and 5-methylfur-fural, showed antifungal activity against Colletotrichum fragariae, Colletotrichum gloeosporioides., and Colletrotri-chum accutatum. at 400 and 100 μg. Among the major components of the oil, only 5-methyl furfural, n.-nonanol, and benzene actaldehyde have shown antifungal activity (Kobaisy et al., 2001).
The use of Hibiscus. species as an antifertility agent has been a long-time rural folk practice in India (Chopra et al., 1950; Anonymous, 1959). Bhavamishra also mentioned this during the 18th century in Yonirogadhikar, in the 70th chapter of Bhavaprakash.. He stated that a woman could never get pregnant if she consumes during her menses a preparation made from the flowers of Hibiscus rosa-sinensis. L. and fermented rice broth, along with the old jaggery. An extensive study to screen the antifertility effect of Hibiscus rosa-sinenesis. has been done. The benzene extract of the flower of Hibiscus rosa-sinensis. at the dose of 73 mg/kg body weight, disturbed the estrous cycle in rats and reduced ovarian, uterine, and pituitary weight (Kholkute et al., 1976). The maximum antifertility activity of the total benzene extract of Hibiscus rosa-sinensis. was mediated via inhibition of implantation (Kholkute & Udupa, 1976a). The total ethanol extract of the flowers of Hibiscus rosa-sinensis. also showed similar activity but was less potent than the benzene extract (Kholkute & Udupa, 1976b). The antifertility activity of flowers of Hibiscus rosa-sinensis. was affected by seasonal variations. The benzene extract of the flowers collected in winter showed maximum potency, followed by those collected in the spring, rainy season, and summer, in decreasing order (Kholkute et al., 1977). The ether-soluble portion of the water-insoluble fraction of the benzene extract of Hibiscus rosa-sinensis. flowers have shown significant anti-implantation and abortifacient effects in female albino rats (Singh et al., 1982). The benzene extract of Hibiscus rosa-sinensis. flowers, when administered intraperitoneally at dose levels of 125-250 mg/kg body weight to adult mice, resulted in an irregular estrus cycle with prolonged estrus and metestrus. An increase in the atretic follicles and absence of corpora lutea indicated the antiovulatory effect of the extract. Estrogenic activity of the benzene extract in immature mice was also evident by early opening of the vagina, premature cornification of the vaginal epithelium, and an increase in uterine weight (Murthy et al., 1997). The aqueous extract of the leaves of Hibiscus rosa-sinensis. at a dose of 100 mg/kg body weight has shown anti-implantation activity. The extract showed a sharp increase in superoxide anion radical and a sharp fall in superoxide dismutase activity. It also showed antiestrogenic activity (Nivsarkar et al., 2005).
An aqueous extract from the leaves of Hibiscus macar-anthus. Hochst ex A.Rich, when given daily to 22-day-old female rats for 5, 10, 15, 20, and 25 days, have shown a decrease in the growth rate of animals. The ovarian and uterine weights were high during the pubertal period (36–41 days). During the same period, the ovarian and uterine protein, ovarian cholesterol, and serum cholesterol levels showed significant differences in treated rats when compared with controls. The ovarian and uterine protein levels as well as the serum cholesterol level were high in animals treated with 49 mg/kg per day of plant extract. A decrease in ovarian cholesterol level was observed in the same group thereby suggesting the presence of an estrogenic compound in plant extract (Telefo et al., 1998).
|
|
|
Are Casement Windows a Practical Choice for Your Home? |
Geschrieben von: aop21sd - 29.03.2022, 02:05 - Forum: News
- Keine Antworten
|
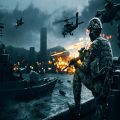 |
Are Casement Windows a Practical Choice for Your Home?
It’s just as important to choose the right windows for your home as it is to select suitable doors. Apart from how the window looks, it should also meet functional specifications, including how much ventilation and light you require, how it opens and if it comes with safety features. Generally, the most common types of windows are double-hung, sliding, and casement windows.
Casement windows are rising in popularity in Malaysian homes, and it’s easy to see why. They are stylish and works well in many modern abodes. For those who are not familiar with casement windows, let’s look at what casement windows are and how they work.
As its name suggests, a casement window features a window frame hinged to a sash which allows it to swing open inward or outward from the side. Thus, they come into two types of opening: inward opening and outward opening.
This type of window is typically a simple structure, flexible and offers good sealing performance, making it a favourable choice for those who want a more minimalist appearance for their home’s architectural style. If you are wondering whether it is a practical choice for your home, read on to learn more about the benefits of a casement window.
If you want a window that maximises natural light and let in more airflow, casement windows do a great job. Due to their minimalist design, they also offer a broader, clearer view of your outdoors, evoking a seamless indoor-outdoor environment.
Window Elements’ Optima 38 is designed with a dramatically wide and deep frame, which instantly creates a statement-making feature in your home. Ideal for bungalows and mansions as well as houses with classic or tropical themes, its elegant frame enhances the aesthetic appeal of your interior while ensuring your living spaces receive optimal views, air, and daylight. A selection of glass is also available, and you can opt for a lattice design or full glass.
More than just a good-looking element, a casement window contributes to the safety of your home as well. Thanks to advanced features and high-strength materials, today’s casement windows have earned a placed in a home’s security system. When designed in combination with innovative functions, casement windows are effective in securing the home from burglary attempts.
Designed with your ultimate home safety in mind, Window Elements’ exquisite aluminium casement windows are highly secure yet elegant at the same time. Take Window Elements’ ArxTech casement window system for example. One of the most flexible systems available in the market, ArxTech casement window is made from premium quality aluminium and comes with high tensile stainless steel security mesh. Featuring a clean-line design with square-edged inner frames adjacent to the outer frame, along with concealed hinges, this casement window provides expansive views from the inside when the window is opened. When closed, you can rest assured your house is well-protected.
Without doubt, casement windows are beautiful with their sleek edges, and streamlined design. From the outside, it gives your home’s facade a modern urban look, while from the inside, it blends in with any interior style with its minimalist appearance.
Made from premium aluminium that is lightweight and clean-cut, Window Elements’ Optima 29 casement window is perfect for complementing a modern minimalist home. Featuring a sleek design with square-edged inner frames adjacent to the outer frame, the window also incorporates concealed hinges and a water drainage channel. The mullion (the vertical bar between the windowpanes) is attached to the window panel, giving you the perfect view from inside out when opened. All these design elements contribute to a “less is more” outlook. In addition to Optima 29’s good looks, this casement window also offers good ventilation, high sealing performance, excellent sound insulation, heat preservation and impermeability.
Whether you seek a window that blends aesthetically with your home exterior and interior, or one that ensures your home is safe and sound, Window Elements’ premium range of aluminium casement windows is an excellent investment for your property. To answer the question in the title, casement windows are indeed a practical choice; in fact, they go beyond offering functional benefits, as they are incredibly stylish and secure at the same time.
uPVC casement doors can be opened both inwards and outward with the support of the hinges fastened on a frame. The casement doors are put in with sashes with many modern modifications that enable the casement hardware to work simply and provides long run performances. The casement doors made up of sturdy, high-quality uPVC material comes with a multi-locking feature to make sure total safety. Also, the casement doors are the most effective choice to direct the breeze within your home. These casement doors are available in enticing colours to suit the client needs. They’re suitable for places like Living rooms, Washrooms and Kitchens! The casement doors together with their sturdiness additionally offer 100 per cent opening, dustproof and soundproof properties. This article elaborates on Why uPVC Casement Doors are Popular.
Aluminum casement doors are doors that will be opened inwards /outwards with the assistance of hinges fastened on a frame. uPVC casement doors come back up with an updated modern twist and are designed with the highest quality casement hardware to create them pretty much simple to work and last for much longer and it will even be organized for opening within and out of doors. Also, the casement doors are perfect to enjoy the beautiful scenery of the outdoors.
The casement doors are made of sturdy materials that have wonderful thermal and acoustic properties of insulation. The simple and elegant style of these casement doors once it’s combined with the multi-locking points and ensures that they’ll offer total security. This type of door is best for providing ventilation for the house. Position these in such a simplest way that they’ll be ready to catch the breeze and direct it within your home. Offer your home an exquisite, enticing gift through the casement Door. Besides, a uPVC casement door will increase the worth of your home.
Casement Doors
UPVC casement door comes with a hundred and eighty degrees opening that brings additional ventilation to your home. Casement doors are the proper alternative for a Soundproof and energy protection system. casement doors reach up to 45dbs with DGU. The casement door suits the bedroom, lobby area, bathroom, room entrance etc. The thermal break casement door comes with 0.5 space glass and 0.5 space uPVC sheet or full space as glass. Moreover, the casement door has a high secured cylinder protection mechanism with a double access key. The casement door has an air adjustment mechanism to prevent energy leaks. The casement door comes in varied colours to grant attraction to your home. Besides, the casement door has five-chamber extrusion technology that helps to cut back the warmth and sound. UPVC casement door surprises you with the smooth operative, metallic handles and hardware.
The casement door comes with four 3D hinges wherever every hinge will bear 120 kilograms of weight so hinges will hold the shutter with high strength. Casement door comes with totally different styles like commercial casement door cum fixed window and sliding with casement etc. All the casement doors consist of imported hardware and the Espag mechanism.
Casement windows have an unusual construction, especially when they’re propped open. Unlike a lot of window styles that slide open to one side, or up and down, casement windows are hinged on a side and crank outward.
The outward prop style makes for an interesting design that some homeowners seem to love while others share not quite as much excitement for. The style is very popular in kitchens, especially over sinks, because of the outstanding ventilation, yet can be used in a number of different rooms.
Characteristics
Casement windows are very open in how they open and close. Instead of a sliding mechanism, the window is attached to a crank that drives the opening and shutting feature. The exterior hinges of the window enable complete, top to bottom ventilation.
The design is popular for kitchens where cooks like to get more ventilation than other sections of the house. The full ventilation can help remove strong odors or other smells from the kitchen, as well as help provide a nice breeze in certain times of the year.
Awning Windows
Casement style windows that are hinged at the top are known in the industry as awning windows. If you prefer this type of hinge it is important to regard them as awning casement windows so the service member can understand exactly what you want installed.
Hoppers
Windows that are casement style and hinged at the bottom are considered hoppers. A good way to picture them is like the name implies, something that is hopping inwardly to the interior of the home.
FCL Windows
A type of casement window that opens from the left-handed side of the frame. The hinges are also on the left, while the locking mechanism is on the right when looking at it from the exterior.
FCR Windows
A type of window that opens from the right-handed side of the frame. Everything is the exact opposite of an FCL opening window, so the locking mechanism is on the left and hinges on the right.
A lever, crank, or cam handle is used to open and shut these types of windows. The crank or cam handle can help support the outwardly positioned window pane when a breeze or gust picks up outside. The one major knock is you have to be careful with these when they’re positioned open, as strong winds can be hard on the hinges and even rip them off.
When the glass panes are installed they are usually set in a rabbeted frame then sealed with some type of beveled putty or glazing. The compound helps secure the glass as well as help with energy efficiency.
Casement windows are often combined in two or more window frames though some only prefer a singular window. The combination of frames may include window panes that open and ones that do not. When combined together they can provide a nearly full wall view of an exterior, as well as a friendly indoor breeze.
History
Casement windows have a long history. In Europe, the style was used before the sash window was introduced. The early designs were built with a metal frame and had leaded glass.
The initial designs were still hinged, yet opened inward to the interior of the building. During the Victorian era, the designs were improved as they began to open outward and also featured shutters. It wasn’t uncommon for builders to construct the casement from timber in its entirety.
Casement style windows continue to remain popular in Europe and are also built in America though not quite as common.
|
|
|
|