Hallo, Gast |
Du musst dich registrieren bevor du auf unserer Seite Beiträge schreiben kannst.
|
Benutzer Online |
Momentan sind 120 Benutzer online » 1 Mitglieder » 119 Gäste
|
Aktive Themen |
Wo kauft ihr ein?
Forum: Allgemein
Letzter Beitrag: marco91
27.05.2025, 14:49
» Antworten: 1
» Ansichten: 141
|
Streamingzimmer einrichte...
Forum: Allgemein
Letzter Beitrag: marco91
27.05.2025, 14:30
» Antworten: 1
» Ansichten: 111
|
Werbebriefe?
Forum: Allgemein
Letzter Beitrag: fritz500
12.05.2025, 17:56
» Antworten: 1
» Ansichten: 191
|
Auto privat verkaufen?
Forum: Allgemein
Letzter Beitrag: fritz500
12.05.2025, 16:21
» Antworten: 1
» Ansichten: 173
|
Vape welche Sorte?
Forum: Allgemein
Letzter Beitrag: conradme
05.05.2025, 20:52
» Antworten: 1
» Ansichten: 206
|
Was tun in Hamburg?
Forum: Allgemein
Letzter Beitrag: conradme
05.05.2025, 19:32
» Antworten: 1
» Ansichten: 200
|
Automatisierung in der In...
Forum: Allgemein
Letzter Beitrag: maxmeyers
25.03.2025, 13:20
» Antworten: 1
» Ansichten: 609
|
Kurzwaren im Internet?
Forum: Allgemein
Letzter Beitrag: fritz500
25.03.2025, 08:54
» Antworten: 1
» Ansichten: 526
|
Mittel gegen schwitzen?
Forum: Allgemein
Letzter Beitrag: fritz500
25.03.2025, 08:00
» Antworten: 1
» Ansichten: 535
|
Sportbootführerschein onl...
Forum: Allgemein
Letzter Beitrag: marco91
24.03.2025, 22:16
» Antworten: 1
» Ansichten: 509
|
|
|
More about Precision Machining |
Geschrieben von: bop02mo - 02.04.2022, 02:25 - Forum: News
- Keine Antworten
|
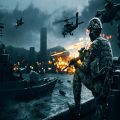 |
More about Precision Machining
Precision machining is what produces a huge number of both large and small objects that we use in daily life. Each intricate piece that makes up an object requires one level or another of a machinist's skills. Likewise, a tool or machine that has been worn down will often require machine tool calibration, welding, or grooving by a precision machinist. From the production of aircraft aluminum alloys to surgical bone drilling devices and custom automotive tools, precision machining reaches into every technology and industry, including oil and gas. In other words, if an object contains parts, it required precision machining.
Quality precision machining requires the ability to follow extremely specific blueprints made by CAD (computer-aided design) or CAM (computer-aided manufacturing) programs like AutoCAD and TurboCAD. The software can help produce the complex, 3-dimensional diagrams or outlines needed in order to manufacture a tool, machine, or object. These blueprints must be adhered to with great detail to ensure that a product retains its integrity. While most precision machining companies work with some form of CAD/CAM programs, they still work often with hand-drawn sketches in the initial phases of a design.
Precision machining is used on a number of materials including steel, bronze, graphite, glass, and plastics to name a few. Depending on the size of the project and the materials to be used, various precision machining tools will be used. Any combination of lathes, milling machines, drill presses, saws and grinders, and even high-speed robotics may be used.The aerospace industry may use high-velocity machining, while a woodwork tool-making industry might use photo-chemical etching and milling processes. The churning out of a run, or a specific quantity of any particular item, can number in the thousands, or be just a few. Precision machining often requires the programming of CNC devices which means they are computer numerically controlled. The CNC device allows for exact dimensions to be followed throughout the run of a product.
Cemented carbides have been widely applied in cutting tools and wear-resistant components due to their ultrahigh hardness and good wear resistance. However, the disadvantages of limited impact toughness and high cost have restricted their further application. Consequently, cemented carbides are usually joining with ductile steels to combine the advantages of both. Among various materials joining technologies, brazing have been an effective method to achieve high quality dissimilar cemented carbide joints. In this paper, the research status of cemented carbide brazing is reviewed. The materials utilized as brazing filler metal in cemented carbide brazing joints are summarized in detail. Researchers have done lots of works utilizing Cu based and Ag based brazing filler metals which are the most commonly used interlayers in brazed joints of cemented carbide and ductile steel. The effects of different filler metal on wettability, microstructure, phase constitution and mechanical properties of brazed cemented carbides joints are analysed. Besides, a series of newly developed brazing filler material such as nickel-based high temperature brazing filler metal, amorphous brazing filler metal and high entropy alloy brazing filler materials are also involved. These newly developed brazing filler metals have shown great potential in fabricating high quality joints. Finally, the current issues of cemented carbide brazing are reviewed and the develop trend is predicted.
Historically, hardened parts were often ground as many cutting tools could not stand up to the rigorous demands of materials with high hardness. Today, many companies are switching from grinding operations to hard turning, as the benefits are numerous.
Hard turning is typically defined as turning of materials harder than 45 Rockwell C (Rc) although, typically hard turning is considered 58 to 68 Rc. As with any machining application the cutting tool must be harder than the material being machined. With this definition, in theory, a carbide insert could machine 60 Rc material, since most carbide is over 85 Rc. However, the reality is carbide inserts would not be able to endure the heat generated in hard turning.
Cubic Boron Nitride (CBN) is the number one choice for hard turning applications. CBN is a man-made very hard material, second in hardness to Polycrystalline Diamond. CBN offers extreme hardness, toughness, chemical and thermal stability.
The sintered CBN blank is cut into desired shapes which are brazed onto cemented carbide blanks in the form of ISO standard geometries; these are final CBN, single or multiple corner inserts.
A common failure mode with CBN in hard turning applications is flaking of the CBN blank. The cause is often the braze. The CBN tip is relatively small so the brazing area is too, then, the braze softens due to heat and causes the CBN to move, causing the flaking. End-users often lose productivity by moving to a softer CBN grade, that runs slower and does not last as long. However, the root cause is often the braze between the CBN and the carbide insert softened and caused the premature flaking. Another common failure mode is the tip comes off while machine. This is an obvious symptom of the braze softening.
This is the reason Tungaloy has introduced its “CBN WavyJoint”. The WavyJoint is a connection surface between the CBN segment and the carbide insert that is an irregular curving surface, alternating in opposite directions, similar to that of waves. This increases the contact surface between the CBN and the carbide insert by 160%. This feature alone decreases the probability of braze softening significantly.
The CBN WavyJoint insert is available in Tungaloy’s new BXA20 grade.
BXA20 is a new substrate, with a lower CBN content, coupled with a new coating that has excellent adhesion strength, making this grade ideal for resisting both crater and flank wear.
The BXA20 coating is a multi-layered titanium aluminum nitride that is 2 times thicker than conventional grades, which enhances flank wear resistance.
The binder in BXA20 has special chemical composition in titanium carbo-nitride base that is well balanced between hardness and toughness. Because of this, BXA20 has very high fracture resistance. This gives BXA20 a wide range of applications from continuous to heavy interrupted cuts.
BXA20 can run at speeds of up to 180 m/min (590 SFM)
WavyJoint is available with an “H” (heavy) edge prep which strengthens the cutting edge, making this ideal for interrupted applications.
This insert is also available with the new HM chip breaker. This breaker enables smooth and reliable chip control, while reducing crater wear on the rake surface. The chip breaker also works to reduce any chatter.
The CBN Wavy inserts are available in CNG*, DNG*, TNG*, VNG* and WNG* geometries.
How precision machining is affecting the future state of medical devices
Precision machining is found in a variety of sectors, including electronics, aircraft, and healthcare. CNC machines are used to make a lot of medical components and devices. The medical equipment industry consists of various medical parts, such as implants for spine reconstruction, knee, and hip replacements, etc.
In an industry where mistakes lead to serious injuries or even death, the machining process of medical parts must be extremely precise. In addition to manufacturing complying with ISO 9001 quality management obligations, medical components and devices must comply with other higher standards.
Medical tools are built with care to ensure that each patient treated is handled with precision. Precision machining is used to manufacture surgical tools, lasers, and even robotics which are now being used in surgeries. CNC Machining provides the know-how, processes, and machinery needed to manufacture these incredibly small parts.
Among all machining techniques, CNC machining has shown to be the best suitable for developing precise medical equipment and instruments. Over time, advancements in CNC processing technology have humanised the manufacture of medical equipment.
CNC Machining in medical device manufacturing
Because of its strong compatibility with the health industry, machinists have begun to tap the potential of CNC medical machining in producing medical precision components. Here are some types of medical equipment that are manufactured using CNC machining:
Surgical tools
CNC machining can produce high-quality surgical tools needed by medical professionals during procedures, such as:
- Cutters.
- Surgical scissors.
- Biopsy tubes.
- Implant holders.
- Blade handles.
- Forceps.
Such CNC manufactured surgical equipment and instruments necessitate meticulousness and precision and additional safety criteria.
CNC machining is a finely detailed and precise process for crafting equipment such as medical instruments. Because certain tools need to be customised for individual patients, they typically are not made using mass production machines. Making custom items by hand can be time-consuming and expensive, but CNC machining allows companies to streamline the process without sacrificing quality and speed of delivery.
Micromachining
Micromachining deals with the manufacturing of remarkably small medical parts utilised in implantable devices and others. Micromachining can produce very small tools or parts, including:
- Drug delivery systems.
- Pacemaker components.
- Miniature screws for implants and devices.
- Catheters.
- Stents.
These machines are extremely sophisticated despite their small size, necessitating extreme accuracy and ability.
Implants
For medical professionals, proper durable and effective equipment is important to ensure that their patients are comfortable and get the best treatment possible. Machinists also require the same; therefore, it is beneficial to make repeated use of strong tools. One strong tool used by both groups is CNC machining. Those who engage in the medical profession commonly perform surgery on patients' bodies where implants are required. These implants can be manufactured through processes performed by machinists using 3D printing or other methods to produce higher-quality gadgets.
Essential medical equipment
CNC machines manufacture the essential equipment needed for today's world, such as heart rate monitors, x-ray machines, and MRI scanners, among a long list of other important items. All these devices are comprised of thousands of individual pieces that can be manufactured using a CNC machine.
The advantages of precision machining in the medical industry
Thanks to precision engineering, we can experience many medical breakthroughs today that would not be possible if not for the new and improved technology and products brought about by the developments and innovations of this field. Take a look at some ways precision machining affects your health and how it will continue to advance the state of medicine in the future.
Machining meets the most stringent tolerances
In the medical industry, accuracy is of the utmost importance. One aspect that contributes to surgical success is a tool that fits perfectly into a surgeon's hand. However, precision machining is not limited to surgical instruments. It helps construct robotic arms and other devices used in surgeries to perform complex operations which were unthinkable even ten years ago - such as breast augmentations or microsurgeries on embryos without harming the mother.
|
|
|
Specialty Mixing Equipment for the Plastics Industry |
Geschrieben von: bop02mo - 02.04.2022, 02:24 - Forum: News
- Keine Antworten
|
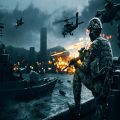 |
Specialty Mixing Equipment for the Plastics Industry
This article presents just a few examples of specialty mixing equipment used in plastics processing. Mixer selection is always formulation-dependent so partner with a reliable mixer supplier offering testing resources to validate a particular mixing strategy. For established processes, a careful re-evaluation of the mixing procedure will often reveal achievable steps for reducing not only cycle time and energy consumption but also waste/rejects, labor cost, cleaning and maintenance.
Polyvinyl alcohol solutions
Polyvinyl alcohol (PVOH, also referred to as PVA) is a versatile polymer that plays multiple roles in the manufacture of adhesives, sealants, cosmetics, paper, textiles and many other products.
Multi-Shaft Mixers are widely used in the preparation of PVOH solutions. Equipped with two or more independently-driven agitators working in tandem, Multi-Shaft Mixers deliver a robust combination of high shear agitation and laminar bulk flow within a wide viscosity range: from water-like consistency to several hundred thousand centipoise (cP).
The most economical design is the Dual-Shaft Mixer which features an anchor agitator and a high speed disperser. Turning at tip speeds around 5,000 ft/min, the saw-tooth disperser blade creates a vigorous vortex that quickly wets out dry PVOH powders or pellets as they are added into warm or room-temperature water (a defoamer may be pre-blended into the water). The sweeping action of the low-speed anchor agitator enhances the exchange of materials within the vessel, continuously “feeding” the disperser blade with fresh product.
For added versatility and shear capability, a rotor/stator assembly may be supplied in addition to the disperser blade and anchor agitator. This Triple-Shaft Mixer design is particularly ideal for applications where other raw materials are dispersed into the PVOH solution and a very tight particle size distribution is required in the finished product.
Plastisols
Formulated for a wide variety of coating, molding and screen printing applications, plastisols are dispersions of polyvinyl chloride (PVC) resin in a liquid plasticizer. Fillers, additives and colorants are also typical components of plastisols.
Multi-Shaft Mixers are well-proven equipment in the manufacture of plastisols. But formulations that undergo very high viscosity peaks (above 1 million cP) are better prepared in Planetary Dispersers and Double Planetary Mixers. These machines consist of two or more blades which rotate on their respective axes as they revolve around the mix vessel. Unlike the agitators in a Multi-Shaft Mixer which rotate from a fixed axis, the blades in a planetary-style mixer continually advance into the batch and are thus able to continuously contact fresh product.
Polymers and additives
Polymer additives such as lubricants, UV and heat stabilizers, colorants, preservatives, flame retardants and impact modifiers are commonly supplied as dry powders or pellets which are blended with virgin plastic feedstock prior to compounding. Thorough and accurate mixing is necessary to achieve a consistent finished product.
Innovations in concrete paving with new technology
The start of 2016 has seen major developments in the concrete paving sector - Mike Woof writes So far in 2016 there have been several major developments in the concrete paving equipment market. Many of the key players have introduced new models, broadening their ranges of machines on offer. US firms continue to dominate this niche area of the construction equipment market, with one European company being the only other major international player. At least two Chinese manufacturers have unveiled concrete
So far in 2016 there have been several major developments in the concrete paving equipment market. Many of the key players have introduced new models, broadening their ranges of machines on offer.
US firms continue to dominate this niche area of the construction equipment market, with one European company being the only other major international player.
At least two Chinese manufacturers have unveiled concrete pavers in the last few years. But these have not been proven on the international market and the designs may not suit global requirements, as well as having fewer capabilities and options than western models. The proven players from the US and Europe have all embraced 3D machine control technology for their machines, allowing these units to deliver high efficiency onsite but it is not clear if the Chinese machines are able to use these systems. For some time to come, the US and European firms will continue to lead this market.
GOMACO has a particularly strong presence in the concrete paving market and is looking to retain that position with the unveiling of two new slipformers, the GP3 and the latest version of its GT-3300.
The firm claims that the GP3 features a wide array of high performance capabilities, making it the most intelligent paver on the market. This paver can handle large road and runway jobs and offers a maximum paving width of 9.14m, achieved through the development of a novel dual-telescoping system. The firm has designed the frame widening system so that it is capable of multiple width changes, boosting its adaptability for a wide range of operations.
The description of the equipment and process may not reveal the significant role that the asphalt milling machine plays in road construction, but it is key.
The asphalt milling machine — also known as a cold planer, pavement planer, pavement recycler, or roto-mill — is a construction machine used to remove bituminous pavement or asphalt concrete from roadways. The result is a somewhat rough but even surface that can immediately be opened to traffic.
The milled surface is accomplished by bringing a rotating mandrel or “head” into contact with the pavement at an exact depth or slope. The mandrel has hundreds of hardened spikes or teeth on its surface, which bite and cut away at the roadway’s surface. The surface material that is removed is normally fed by conveyor into a dump truck or semi trailer, but can be left in place or windrowed to be removed or recycled later. A water spray system provides cooling for the mandrel, as well as dust management.
In the 1970’s, Galion Iron Works, based in Galion, Ohio, manufactured the first production road milling machines, which were called Galions. These first units resembled motorgraders in shape and size. The difference was there was a 30-in. wide (76 cm) milling head where the scraper blade would normally be. The cutter drum was set into action by a large hydraulic pump.
Asphalt milling is the process of grinding up asphalt that can then be recycled. The process came about because many streets were getting layered higher and higher as new surfaces were added, thus reducing the curb height and creating roadway drainage problems.
Early milling machines were simply a mining mandrel attached to a mobile undercarriage. They were designed to remove a layer of old concrete or asphalt so that a new layer could be applied to a better quality base than resurfacing over the old road surface.
From the start, the emphasis for milling machines was to place more power to the cutting drum, which is needed to remove more material. Thus, the cutter head itself and the cutting teeth designs became critical. The cutting teeth would dull fairly quickly and needed frequent replacement. The replacement process could cause enough downtime to greatly detract from the initial efficiency of the milling process itself. So manufacturers worked on designs for quicker replacement as well as increased durability of the cutting teeth. Different sized cutting drums were offered so that machines could mill at different widths.
Milling machines feature conveyor systems to collect the material during the milling process, thus reducing the labor of picking the material up from the roadway. Newer machines require two or more people to operate safely and efficiently. The operator stands on the deck of the machine and controls most of the machine’s functions, while a worker on the ground controls the depth of the cut and keeps an eye out for obstructions in the roadway such as manholes and/or water valves.
Today’s machines are bigger and more technologically advanced. They are designed to handle any asphalt aggregates in use today. Depending on the depth of the cut, some of the larger machines can cut close to 15,000 sq. yds. (13,000 sq m) a day, at 75 ft. (22.8 m) per minute.
In addition to faster speed, added precision to the milling process has become important. The innovation of controls and automation has brought greater precision for controlling slope, depth and speed.
There is no question that the technological advancements made in microelectronics have benefited road milling machines. Electronics designed to improve performance, include electronic sensors and a built-in cross slope. A pair of sensors can read a variety of references from 12 to 55 in. (30.5 to 140 cm) directly below the bottom of the sensor. Each sensor can be calibrated and adjusted from the ground level or at the operator’s console.
|
|
|
How to Wear a Polo Shirt With Style |
Geschrieben von: bop02mo - 02.04.2022, 02:22 - Forum: News
- Keine Antworten
|
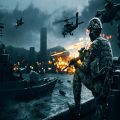 |
How to Wear a Polo Shirt With Style
The polo shirt is a true men’s style staple.
Yet despite its ubiquity in the male wardrobe, it’s not a garment that typically comes in for much affection or enthusiasm.
Perhaps this is because of the negative associations with which the polo shirt is laden. It is often thought of in terms of a uniform — either literally, as in the required get-up of a pizza delivery man or elementary school student, or metaphorically, as the go-to garb for corporate drones and preppy fraternity brothers. The polo is further seen as the default of the sartorially lazy — something a guy dons when an event requires a shirt with a collar, and he can’t be bothered to even button up an Oxford.
Yet the polo deserves a little more love than it typically gets. Falling between a t-shirt and a dress shirt, it’s the perfect garment for the many events in life that aren’t at all formal, but aren’t outright casual either. It’s a great shirt for summertime first dates, backyard BBQs, and when you’re not sure exactly where the plans for your day or evening will take you.
Even in terms of casual everyday wear, the cool, breathable polo shirt is just as easy and comfortable as a tee, but looks a notch more put together, so that swapping the former for the latter is a zero-effort way to upgrade your summer style.
And far from being blandly uniform, or only worn by one type of man, polos have been popular with widely varied groups, from Nantucket yachtsmen to West Coast skaters; there are different types of polos for different occasions, and they can be worn and styled in many different ways.
In other words, contrary to popular opinion, the polo shirt is quite versatile and can be sartorially interesting. Truly, the polo shirt is clutch.
Today we’ll take a look at how to elevate it beyond the realm of casual Fridays and suburban dad-dom — how to wear a polo with style.
In its early days, tennis had a touch of aristocratic flare and was played in a get-up known as “tennis whites” — flannel trousers, a dress shirt (with sleeves rolled up), and even a tie. Thick, heavy, hot, and cumbersome, these garments obviously didn’t lend themselves well to playing an active, outdoor sport.
Seven-time Grand Slam winner René Lacoste decided to do something about this issue, creating his own ideal tennis shirt. Made of a comfortable, breathable “jersey petit piqué” cotton, the white short-sleeved shirt eschewed buttons all the way down for a placket of three up top, and included a soft, unstarched collar that was still stiff enough to flip up to protect his neck from the sun. The flexible, lightweight shirt also had a longer tail in the back to keep it tucked into René’s trousers.
Lacoste debuted the shirt at the 1926 U.S. Open — which he won in both comfort and style. The following year, Lacoste, who was nicknamed “the Crocodile,” adhered the now famous reptilian logo to the breast of the shirt. And in 1933, the retired player began to manufacture his garment for the masses.
The “tennis shirt” caught on with other kinds of sportsmen, particularly polo players. These athletes had developed their own “polo shirt” — the Oxford button-down (the buttons on the collar were designed to keep it from flapping in your face as you galloped about the field) — decades prior. But Lacoste’s short-sleeve garment proved even more suitable to the game, and was so widely adopted that even tennis players began to refer to it as a “polo shirt.”
Wear Pajamas To Work Day
After spending a hectic day getting your taxes filed in time for the April 15th deadline, it’s time to enjoy the day after by celebrating Wear Pajamas To Work Day. This holiday is celebrated on April 16th and encourages everyone to go to work while wearing their favorite pair of pajamas. Of course, if a person does that they’re going to want to make sure their boss is okay with the idea. Fortunately, there are plenty of bosses who are okay with this holiday and allow their employees to be a little more relaxed while they’re working.
The History Of Wear Pajamas To Work Day
This holiday has been around for quite a few years and can be traced all the way back to 2004. This is when Pajamagram launched an advertising campaign that encouraged people to wear their pajamas to work. It was intended to be a one-off campaign, but people liked the idea so much they have celebrated it ever since.
Facts About Pajamas
While we were researching this holiday, we came across some interesting facts about pajamas. Although most people give little thought to their pajamas—unless they’re scratchy or need to be washed—pajamas are actually an interesting item of clothing that’s worth a closer examination.
- It’s believed that pajamas go back to the Ottoman Empire and were first invented in India.
- Pajamas could’ve also originated during that time in Turkey or Iran.
- In Southern Asia, pajamas are often called “Night Suits.” This is also their name in parts of Africa.
- The largest footed PJ party in the world was held on March 11, 2012, in Texas. 309 adults attended.
- During the 1920s, some people would wear their pajamas to the beach.
- Prior to the 1950s, flapjacks on pajamas were common to make it easier for the user to use the bathroom.
- Pajamas originally began as only loose pants tied at the waist.
- During the 17th century, pajamas were introduced to England as lounging attire. They quickly fell out of fashion.
- At the beginning of the 20th century, pajamas were reintroduced as women’s sleepwear.
Celebrating Wear Pajamas To Work Day
Celebrating Wear Pajamas To Work Day is as easy as wearing your PJs to work—with your bosses’ blessings of course. It’s also a good day to use the hashtag #WearPJToWorkDay on your social media accounts to encourage other people to celebrate this day as well. After all, there are few things better than being able to go to work wearing your pajamas and not get stared at for doing so. It’s just a shame that all of us can’t wear our pajamas to work every day of the year.
Hooded sweatshirts, often referred to as "hoodies" now hold a permanent place in fashion. The hoodie was a piece of clothing that started out primarily as workout wear. Now you can find hoodies made by famous clothing designers and ranging in price as high as the hundreds of dollars for some designs. Why has the hoodie become so popular? Let's take a look at who wears them the most.
The hoodie is definitely geared toward the younger generation. The urban clothing industry is definitely in the lead for the creation and marketing of hoodies. The trend can be traced back to rappers who wore them as a way of looking sinister. Now the trend has taken off and any urban clothing enthusiast would have at least one hoodie in their wardrobe. Famous hoodie brands include Christian Audigier, LRG, and BAPE (Bathing Ape). These clothing designers know what the young crowd want - unique designs that give the individual a sense of personal style.
Hoodies are no longer just popular for males. Clothing designers have created hoodies that fit the frame of young women as well. They do not fit large and bulky the way most men prefer their hoodies. Women'hoodies are made to fit a woman's frame to still accentuate her figure. The urban look of the hoodie compliments both men and women when wearing a cool pair of jeans and some fly kicks.
The hoodie is not limited just to the urban clothing scene. Surfers and skateboarders are big fans of the hoodie as well. It is not uncommon to see both surfers and skateboarders sporting their favorite brand of hoodies on the beach or at the skate park. Popular brands for these hoodies include Element, Billabong, and Hurley. Not only are hoodies creating a fashion statement, but they are practical for a surfer who is attempting to stay warm after catching some early morning waves.
T-shirts come in different styles, colors, and sizes, to suit the unique tastes of global citizens. But something we rarely think about is the history of t-shirts–how did the t-shirt originally come into being?
T-shirts were originally worn by veteran men as undergarment beneath their uniforms, but have since evolved to become a tool for branding and self-expression.
Here’s the history of t-shirts, and how they’ve evolved throughout the years.
The Beginning of the T-shirt: The Earlier Years
T-shirts were first introduced in United States sometime around the time of the Spanish World War. They were given to members of the U.S. Navy to be worn as undergarment beneath their uniforms.
Previously called a union suit, the first form of t-shirt was from New York. A union suit was a one-piece garment in white color with buttons in front. Nowadays, we’d probably call it a onesie, despite the fact that it’s used as an undergarment and is tighter and more close fitting than it’s modern counterpart.
Why sweatpants are the best. No contest.
Some days are made for sweatpants. You know the ones – maybe you feel a little bloated, or after a long week of wearing suits to the office, you just want to unwind. And it’s also nice to have something you can move in when you’re wrangling the kids, running errands or just going for a walk with the dog. These days, sweatpants don’t have to scream, “Hello world, I’ve given up,” as they can look as stylish as anything else in your closet.
They’re not ugly any more. We promise.
Back in the day, your average pair of sweatpants were best reserved for occasions like “I have the flu” and “the baby was throwing up all night.” Baggy, shapeless and unattractive, they were just plain ugly. Sweatpants have undergone a major style transformation though, and you can now find ones with feminine cuts and waistlines you’ll want to show off instead of hide. And they come in every color you can imagine – not just heather gray.
They’re just so comfortable.
Finding a way to feel comfortable while looking good is a must for surviving the roller coaster ride of life. When you need a hip yet laidback outfit, try some slim-fitting sweatpants in black paired with your favorite sneakers and a cute v-neck tee. The soft, stretchy fabric is completely forgiving, but the cut will compliment your curves without offending your style sensibilities. Just tie your hair in a loose bun, reach for some sunglasses, grab a cute bag and you’ll be ready for anything.
|
|
|
What Are the Best Uses for Palm Stones? |
Geschrieben von: bop02mo - 02.04.2022, 02:20 - Forum: News
- Keine Antworten
|
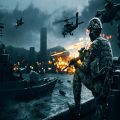 |
What Are the Best Uses for Palm Stones?
You can use palm stones for many purposes, including relaxation, energy boost, protection, and meditation. Holding a palm stone in your hand creates a strong connection between the stone's energy and your energy field or aura. Due to their oval or round shape, you can easily carry them in your purse or pocket to have them with you throughout your day. There are many ways to use palm stones; we've rounded up a list with the most common and effective ones. You can choose to integrate into your life the ones that fit your lifestyle. We also recommend a few palm stones for each category to make it easy to find the best stones for your needs.
Simple and Effective Ways to Use Your Palm Stones
1. Relaxation - these round-shaped stones are excellent natural tools for relaxation. Just holding an oval stone with calming vibe can bring you moments of stillness and tranquility. We recommend the following palm stones for relaxation:
Amethyst palm stone
Selenite palm stone
Montana Agate palm stone
2. Protection - certain stones have a protective vibe and can protect you from negative influences. By carrying palm stones with powerful protective energy or keeping them nearby makes it possible to be protected by negative energies, including harmful EMFs. We recommend the following palm stones for protection:
Black Tourmaline palm stone
Red Tourmaline palm stone
Black Opal palm stone
3. Yoga, Prayer and Meditation - one of the best ways to enjoy a palm stone's vibe is to use it during your daily spiritual practice. There are various stones with high vibrations that can help us enter deep states of meditation. Palm stones can be also efficient during your yoga session or for prayers, as the energy of the crystals will facilitate the resonance with positive universal energies. We recommend the following palm stones for yoga, prayer, and meditation:
Lazulite palm stone
Blue Aragonite palm stone
Silver Sheen Obsidian
4. Healing - energy healers, crystal therapists, Reiki masters often use palm stones during their healing sessions. You can also experience the healing benefits of palm stones by placing them on your body, on the area you want to heal. Another simple way is to make healing crystal patches.
The best palm stones for healing sessions:
Polychrome Jasper palm stone
Serpentine palm stone
Amazonite palm stone
5. Regeneration - when you get too embroiled in your daily activities, symptoms like tension in the neck and shoulders, anxiety, fatigue, and sleeping problems are signs of needing to relax and recharge your batteries. Schedule 10-15 minutes of relaxation during your daily programs to recharge and give yourself a quick energy boost. Using palm stones will make your relaxation more efficient.
Palm stones for relaxation:
Fossilized Palm Root palm stone
Honey Calcite palm stone
Nuummite palm stones
6. Quality Sleep - undisturbed quality sleep is essential for your health and overall well-being. A simple way to improve your sleep quality is to fall asleep holding a palm stone, as the calming energy of the stone will induce a state of relaxation. You can also place palm stones under your pillow.
Here are some best palm stones that help with sleep issues:
Chevron Amethyst palm stone
Kambaba Jasper palm stone
Clear Quartz palm stone
7. Forgiveness, Love, and Self-Love - palm stones with a gentle, soft, soothing energy can help you achieve emotional balance and transform our negative emotions into compassion, self-love, or forgiveness. Tap into the following palm stones’ energies by keeping them nearby:
Rose Quartz palm stone
Mangano Calcite palm stone
Sea Green Calcite palm stone
8. Work and Study - whenever you deal with a fog of mental exhaustion, it’s a sign that you need a refreshing break. Using palm stones will help you get back faster into a state of excellent focus and concentration. A few minutes of connection with these stones will help you return to work recharged and regenerated. Here are some of our recommended palm stones for mental focus and concentration:
Sunstone palm stone
Green Fluorite palm stone
Blue Apatite palm stone
9. Home decor - you can also display your favorite palm stones in your home or workspace to create a safe and energetically pure ambiance. These stones with a beautiful oval shape make excellent home decor elements. The following colorful palm stones will fascinate with their beautiful appearance no matter where you display them:
Coral palm stones
Chrysophrase palm stones
Labradorite palm stones
The Many Benefits of Using Candle Holders
Candles are a great way to add warmth to your home or to set up a romantic mood at an event. Lighting a candle also creates a peaceful and soothing atmosphere that helps relax and calm your mind, body, and soul. In the past, candles were used as the primary light source but in modern times they are commonly used either as decorative accessories or for their positive and calmative features.
Whether you plan to use candles to enhance and illuminate your space or to give a positive vibe to your living room, using candle holders is essential. As the name suggests, votive candle holders are used to hold the candles for various reasons. Candles can be quite dangerous and create a mess if placed without a base and are left unattended. There are many significant uses of glass candle holders that cannot be ignored. We have gathered some key points to help you understand the importance of using pillar candle holders. Read on to learn more about the benefits of using a candle holder stand to properly place the candle on your table instead of just placing a random plate under it.
1). Candle Holders Give Support to Your Candles
Candles come in a variety of shapes, sizes, and designs. Some have a small or thin base like taper candles while others have a broad bottom such as pillar candles. Glass candle holders provide support to the candles to help them stand upright and give an exclusive visual appeal. Fixing your candles in an appropriate candle holder gives them the needed support to keep them in place. For instance, taper candle holders can be used to help dinner candles stand tall to give your dining room table an elegant and sophisticated look. Similarly, votive candle holders are small cups to hold and support a votive candle that might otherwise collapse on its own. Although tea light candles are encased in a small container it is still important to use tealight candle holders to support them properly as they are small in size.
2). Safe and Secure Base for Your Candles
The need for candle holders was discovered a long time ago when people realized that candles can tip over and cause fires. The primary function of candle holders is to provide a secure and safe base for candles to avoid any mishaps. Placing a lighted candle without a sturdy base is like waiting for a disaster to happen. Even a slight push can cause the candle to fall over and the table cloth or curtains might catch fire. To prevent any unpleasant events, it is important to use glass candle holders beneath your open flames for extra safety and precaution. Tall candle holders keep your candles stable and you don’t need to worry about kids or clumsy guests accidentally nudging your candles and wreaking havoc on the dinner table. Our Wooden candle holders and metal candle holders are sturdy enough to safely place your candles anywhere to enhance your home décor. Make sure to place your candle holders on a flat and even surface to ensure everyone’s safety.
3). Candle Holders Prevent Hot Wax Spills
Another important benefit of candle holders is that they prevent hot wax from spilling all over the place and creating an unpleasant mess. Hot wax can cause skin burns and also spoil your tables and other furnishings. Metal candle holders can be used to accumulate all the dripping wax from a burning candle without allowing it to spill over. For instance, when you light up votive candles placed in votive candle holders, the wax from the candle will be collected in the votive candle holder and there will be no mess at the table, making clean up after the party much easier and efficient.
What Are Crystal Points?
If you’ve ever marveled at crystals, you’ve likely encountered varieties with sharply defined points. How do crystals get their points? A crystal point is a sharply-defined pinnacle on either one side, or both sides, of the crystal. All sizes of crystals can have crystal points — from the smallest to the largest.
Crystal points are technically referred to as “terminations” in the stone. Terminations occur as a result of mining, polishing or nature’s influence. Is there a purpose for crystal points and are they natural? The points on a crystal encapsulate the harnessed energy required to transmit healing into our environment and space. Crystal points essentially reveal which direction the crystal energy flows from. In addition, the points on a crystal foster our ability to focus and gain mental clarity. Simply put, crystal points direct energy inward or outward and enhance the healing properties of a crystal.
Are Crystal Points Natural?
It’s no secret that crystals with points are attractive and holistic, but are crystal points natural? The answer isn’t so clear cut. In fact, the points on a crystal can occur naturally, or from polishing.
Natural Crystals
In some cases, a sharp-pointed crystal appears after the mining process. Ultimately, when the crystal is mined, it can be exposed to chips and dings from the excavation process. When the crystal comes from the earth, it may have one point, or be misshapen. As a result, the crystal leans to one side, rather than gradually mounting into a single point. An off-center termination in a crystal results in a blocked flow of energy from the stone. To remedy this problem, the crystal is shaped into a pointed termination with six sides, which is called a Generator. However, not all misshapen crystals are polished into a Generator.
Angel Aura Quartz Properties
As you might imagine from its name, Angel Aura Quartz is a stone whose appearance can’t help but to stir up feelings of ethereal realms and otherworldly wisdom.
Despite having a sheer, shiny and clear outer appearance, it would seem as though every color imaginable dances inside of this stone, and it has led to many associations of magic and the divine over the years.
This is a stone whose feeling and imagery inspires peace and a clear mind. It can be pretty hypnotic to look at, and has been prized over the centuries for its appearance as much as its mysticism.
Of course, modern science has helped us to understand how Angel Aura Quartz is able to form with such delicate yet overpowering colors within, yet even that scientific understanding has done nothing to take away the mysticism and intrigue of this wondrous stone.
Faith healers and those of a spiritualistic mindset have always been drawn to this stone, but even collectors and those seeking personal growth can likewise find plenty of benefits to owning their own piece of Angel Aura Quartz.
There’s something radiant and beyond the norm about these stones, and the way in which they are formed in the natural world means that no two Angel Aura Quartz pieces could ever be identical.
It’s a Clear Quartz bonded with Silver and Platinum, or sometimes with gold and a variety of other trace metals.
It is formed in a high-pressure vacuum chamber, and the precious metals give the Angel Aura Quartz its new and dazzling color.
Angel Aura Quartz usually exhibits a silvery, rainbow, and light blue radiance that resembles the delicate wings of an angel! This crystal is also often called Pearl Aura, Opal Aura, and Rainbow Aura.
|
|
|
Application of industrial endoscope in Aeroengine bore detection |
Geschrieben von: bop02mo - 02.04.2022, 02:19 - Forum: News
- Keine Antworten
|
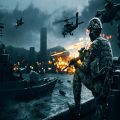 |
Application of industrial endoscope in Aeroengine bore detection
As a more convenient way of travel, civil aviation has been widely accepted and has become one of the most important means of transportation for modern people's business and travel. At the same time, aviation safety has always attracted people's attention. As the "heart" of the aircraft, aero engines are closely related to aviation safety. Nowadays, there are various non-destructive testing tools for testing and repairing it. The use of industrial endoscope for hole detection is one of the routine tasks. It does not need to disassemble and destroy the engine structure, and can perform efficient testing. Accident prevention plays an important role.
The working environment of civil aviation engines is very harsh, under high temperature and high pressure for a long time, the internal temperature is as high as 2000 ℃, so if the potential safety hazards are not eliminated in time, it may cause serious consequences. It is necessary to use videoscopes for regular non-destructive testing. So what aspects of the industrial videoscope can be used for inspection? Mainly in the following aspects:
1. Compressor inspection.
2. Detection of combustion chamber components.
3. Turbine blade inspection.
Check the compressor and turbine internal blades for flaws, cracks, incompleteness, etc., and check the internal damage of the combustion chamber. If necessary, it is necessary to accurately measure the size of the defect to formulate corresponding countermeasures.
Hole inspection through the endoscope can quickly and timely find the internal structural damage of the engine, continue to track and evaluate the expansion of the damage, avoid greater damage, effectively reduce the maintenance cost of the engine, and fully save the maintenance downtime. Of course, at the same time, engine hole inspection is also a complex task, and its accuracy is closely related to the operational level, work experience, theoretical knowledge and other qualities of the inspectors. Therefore, in general, hole inspection needs more experience. , Skilled inspection personnel perform operations to avoid missed inspections and false inspections; at the same time, professionals are also required to perform more accurate image analysis to avoid false inspections and misjudgments of the inspection results, thereby incurring unnecessary additional costs.
Visual Inspection Using Borescopes
In recent years, many facilities have obtained borescopes for processing personnel to use during visual inspection of endoscopes. Borescopes are tiny flexible endoscopes that can be used to look inside the small areas of medical instruments, and they are particularly well suited to inspect the interiors of ports and lumens. The utility of borescopes in visual inspection was initially established during an investigation of surgical site infections linked to contaminated instruments used in knee and shoulder surgery. When investigators used a borescope to look inside arthroscopic shavers, they found retained debris, including bone fragments and brush bristles.27 In a foundational study by Azizi et al.,28 visible residue or debris was detected inside 95% of 350 lumened surgical instruments.
Ofstead Studies Involving Borescope Examinations
After learning about the potential value of borescopes for identifying retained soil and debris, our team designed a study where the ports and channels of 20 colonoscopes and gastroscopes were carefully inspected three times during a seven-month period.7 Our goals were to determine whether damage and debris accumulated over time and whether more rigorous processing could completely eliminate contamination. This was the first time a medical borescope was used to prospectively monitor endoscope cleanliness and damage over time, so we had to develop our own protocol and reference materials.
First, we familiarized ourselves with the normal appearance of endoscope ports and lumens (Figure 1). During the baseline assessment, we inspected the inside of ports and channels and took photographs at specified points inside each endoscope. That way, we could compare the appearance of each component at baseline with how it looked at follow-up assessments. We were also able to compare each colonoscope or gastroscope with others in the fleet, which helped determine whether what we saw were normal features of the channels or ports or irregularities that required assessment by an endoscope maintenance technician.
A wireless electronic endoscope that transmits signals by Wi-Fi is developed for use in single-hole endoscopic surgery and future application to natural orifice surgery. The innovative electronic endoscope developed in this study has a disposable design, completely preventing patents from taking risks of cross infection. The main components of the endoscope are a disposable component of the front tip and the hand-held part of the rear tip. The front tip consists of a lens, metallic tube, and electronic joint whereas the rear tip consists of a power switch, image converter, wireless transceiver chip, and antenna.
Why it's done
An upper endoscopy is used to diagnose and, sometimes, treat conditions that affect the upper part of your digestive system, including the esophagus, stomach and beginning of the small intestine (duodenum).
Your doctor may recommend an endoscopy procedure to:
Investigate symptoms. An endoscopy may help your doctor determine what's causing digestive signs and symptoms, such as nausea, vomiting, abdominal pain, difficulty swallowing and gastrointestinal bleeding.
Diagnose. Your doctor may use an endoscopy to collect tissue samples (biopsy) to test for diseases and conditions, such as anemia, bleeding, inflammation, diarrhea or cancers of the digestive system.
Treat. Your doctor can pass special tools through the endoscope to treat problems in your digestive system, such as burning a bleeding vessel to stop bleeding, widening a narrow esophagus, clipping off a polyp or removing a foreign object.
An endoscopy is sometimes combined with other procedures, such as an ultrasound. An ultrasound probe may be attached to the endoscope to create specialized images of the wall of your esophagus or stomach. An endoscopic ultrasound may also help your doctor create images of hard-to-reach organs, such as your pancreas. Newer endoscopes use high-definition video to provide clearer images.
Many endoscopes allow your doctor to use technology called narrow band imaging, which uses special light to help better detect precancerous conditions, such as Barrett's esophagus.
Risks
An endoscopy is a very safe procedure. Rare complications include:
Bleeding. Your risk of bleeding complications after an endoscopy is increased if the procedure involves removing a piece of tissue for testing (biopsy) or treating a digestive system problem. In rare cases, such bleeding may require a blood transfusion.
Infection. Most endoscopies consist of an examination and biopsy, and risk of infection is low. The risk of infection increases when additional procedures are performed as part of your endoscopy. Most infections are minor and can be treated with antibiotics. Your doctor may give you preventive antibiotics before your procedure if you are at higher risk of infection.
Tearing of the gastrointestinal tract. A tear in your esophagus or another part of your upper digestive tract may require hospitalization, and sometimes surgery to repair it. The risk of this complication is very low — it occurs in an estimated 1 of every 2,500 to 11,000 diagnostic upper endoscopies. The risk increases if additional procedures, such as dilation to widen your esophagus, are performed.
You can reduce your risk of complications by carefully following your doctor's instructions for preparing for an endoscopy, such as fasting and stopping certain medications.
Signs and symptoms that could indicate a complication
Signs and symptoms to watch for after your endoscopy include:
Fever
Chest pain
Shortness of breath
Bloody, black or very dark colored stool
Difficulty swallowing
Severe or persistent abdominal pain
Vomiting, especially if your vomit is bloody or looks like coffee grounds
Call your doctor immediately or go to an emergency room if you experience any of these signs or symptoms.
How you prepare
Your doctor will give you specific instructions to prepare for your endoscopy. In some cases your doctor may ask that you:
Fast before the endoscopy. You will need to stop drinking and eating four to eight hours before your endoscopy to ensure your stomach is empty for the procedure.
Stop taking certain medications. You will need to stop taking certain blood-thinning medications in the days before your endoscopy. Blood thinners may increase your risk of bleeding if certain procedures are performed during the endoscopy. If you have chronic conditions, such as diabetes, heart disease or high blood pressure, your doctor will give you specific instructions regarding your medications.
We observed recordings of pictures obtained from patients with diseases of the larynx by using a new type of rhino-larynx electronic endoscope, PENTAXVNL-1530 connected to a video processor, PENTAX EPM-3300 (Asahi Optical Co., Ltd.). The electronic endoscope differs from the fiberoptic endoscope in that it contains a small light-sensitive charge coupled device (CCD) chip that is attached to the tip of the endoscope. This electronic endoscope has the smallest CCD camera of 5.1 mm in diameter, in the tip portion, and can be passed through the nasal passage into the laryngeal cavity. The dynamic image provided by this system is superior to that obtained by a flexible laryngofiberscope in resolution of the detail.The system with this electronic endoscope was introduced and some clinical cases were presented.
|
|
|
Why is Micro Switch called a micro switch |
Geschrieben von: bop02mo - 02.04.2022, 02:17 - Forum: News
- Keine Antworten
|
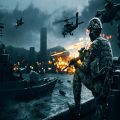 |
Why is Micro Switch called a micro switch
Probably because the first producer was the American company called Micro Switch. And as these products were very popular, the name micro switch became a generic trademark for all producers.
The company Micro Switch was acquired by Honeywell in 1950. And Honeywell registered the trademark Micro Switch. Other manufacturers used the name Snap-Action Switch or Basic Switch.
But the question still remains why the founder of the company, Mr. Schulte, decided to name his company Micro Switch?
Because they switched micro-amps? Probably not since in 1937 the micro-amps did not even exist. Because of their miniature dimensions?
Probably yes, at that time they could be considered tiny.
And what exactly is that micro switch?
It is an electric switch (patented in 1932) that is actuated by very little physical force. Switching happens at specific positions of the actuator (not like other switches). Relatively small movement at the actuator button produces a relatively large movement at the electrical contacts, which occurs at high speed (regardless of the speed of actuation). Typical durability is from 1 to 10 millions of cycles. This durability is a natural consequence of the design.
Micro switches are not operated by person; it is always some moving part of the equipment. Common applications are detection (e.g. jammed paper in photocopier, the presence of material or product). Other application can be a limit switch (for control of machine tools) or door switch (e.g. fridge).
And which one do we love the most?
We like the Marquardt micro switches. the most. Why? Because it is that Marquardt that produces electronic keys for Mercedes, Volkswagen and other premium cars and that Marquardt that produces switches for blue Bosch electric tools. That’s why.
Marquardt has a nice range of micro switches. Three basic sizes - miniature (Series 1005 and 1080, width about 28mm), subminiature (Series 1050, width about 20mm) and ultra subminiature (Series 1055, width 13mm).
Then we choose the right terminals and the right type of actuator:
Terminals:
- Straight PCB pins
- Angled PCB pins
- Soldering eyelets
- Quick connect (Faston)
- Cables
Actuator:
- Pin plunger
- Straight lever
- Roller lever
- Simulated roller
- Spring lever
What is important when using micro switches?
First of all, load size and type. Some types of load have much higher inrush current. E.g. relay has 5 times higher inrush current than nominal, motor 10 times, incandescent lamp 15 times and solenoid even 20 times. On the other hand, for switching small loads, do not use a micro switch for high currents. We recommend using micro switch with gold plated contacts.
For harsh environment (dust and moisture), please use micro switches with higher IP rating (up to IP67).
We recommend applying a contact protective circuit to extend contact durability, prevent noise, and suppress the generation of carbide or nitric acid due to arc. The use of a contact protective circuit may delay the response time of the load. Examples of such circuits:
-RC Circuit - in systems with power supply of 24-48V, it is effective to connect the RC circuit in parallel to the load. When the power supply voltage is 100-200V, then in parallel to the contacts (in this case when AC is switched, the load impedance must be lower than the R and C impedance)
-Varistor - the use is very similar to RC circuit, even with those conditions when in parallel to load or contacts. Varistor ensures that no high-voltage is imposed on the contacts.
-Diode - energy stored in the coil is changed into current by the diode connected in parallel to the load. Then the current flowing to the coil is consumed and Joule heat is generated by the resistance of the inductive load. The diode must withstand a peak inverse voltage 10 times higher than the circuit voltage and a forward current as high as or higher than the load current.
-Diode and Zener diode - this method will be effective if the reset time delay caused by the diode method is too long. Zener voltage for a Zener diode must be about 1.2 times higher than the power source.
Ensure that the operating body will work smoothly. The shape of it should be round or oblique - to prevent shocks to the actuator. And of course, operate the actuator of a hinge roller lever or simulated hinge lever type from the right (correct) direction.
Ensure that the stroke to the actuator is set not to exceed the total travel position. If not, the operating body may damage the actuator or the switch itself, and the stress applied to the moving spring inside the switch will increase and then, the durability of the switch may be deteriorated.
And some more details - not to tighten the screws too much - not to deform the body of a switch. Or when soldering, adjust the amount of solder so that the flux does not enter the switch, it can cause contact failure.
What are Limit Switches?
Limit switches are used to automatically detect or sense the presence of an object or to monitor and indicate whether the movement limits of that object have been exceeded. The original use for limit switches, as implied by their name, was to define the limit or endpoint over which an object could travel before being stopped. It was at this point that the switch was engaged to control the limit of travel.
How does a limit switch work?
A standard limit switch used in industrial applications is an electromechanical device that consists of a mechanical actuator linked to a series of electrical contacts. When an object (sometimes called the target) comes in physical contact with the actuator, the actuator plunger’s movement results in the electrical contacts within the switch to either close (for a normally open circuit) or open (for a normally closed circuit) their electrical connection. Limit switches use the mechanical movement of the actuator plunger to control or change the electrical switch's state. Similar devices, such as inductive or capacitive proximity sensors, or photoelectric sensors, can accomplish the same result without requiring contact with the object. Hence, limit switches are contact sensors in contrast to these other types of proximity sensing devices. Most limit switches are mechanical in their operation and contain heavy-duty contacts capable of switching higher currents than those of alternative proximity sensors.
Components of a limit switch
Limit switches consist of an actuator with operating head, the switch body mechanism, and a series of electrical terminals that are used to connect the switch to the electrical circuit that it is controlling. The operating head is the part of the limit switch that comes in contact with the target. The actuator contains is connected to the operating head, whose linear, perpendicular, or rotary motion is then translated by the actuator to close or open the switch. The switch body contains the switch contact mechanism whose state is controlled by the actuator. The electrical terminals are connected to the switch contacts and enable wires to be joined to the switch through terminal screws.
Industrial machinery that undergoes automatic operations usually requires control switches that activate according to the movements involved in a machine’s performance. For repeat usage, the accuracy of the electrical switches needs to be reliable and their response rate should be prompt. Due to the mechanical specifications and performance parameters of different machines, factors such as size, operational force, mounting method, and stroke rate are important characteristics in the installation and maintenance of limit switches. In addition, a limit switch’s electrical rating should be matched to the mechanical system loads that it will be controlling in order to avoid instrument failure.
Many of our footswitches are suitable for industrial use, we have been supplying to this sector for many years.
With over 70 years’ experience in developing, manufacturing and distributing industrial foot switches we have the experience and knowledge to produce footswitches which offer all the characteristics suited for industrial use.
Characteristics of our Industrial Footswitches
Our wide range of industrial foot switch models incorporates some of the desired features for products in this sector including;
Long life
Mechanical Stability
Ergonomic designs
As well as stock products for fast delivery, many of our industrial footswitches also have the folliowing features:
Customisable features – these include: customised cables, connectors, electronics, labels, colours, logos and bases.
Single or multi pedal – many of our switches have a multi pedal version
Optional guards – these offer additional user and switch protection and are spacious for use with safety shoes.
Two Types of Timer Switches
Manual Setting Timer Switch: This type is more common in my country (Malaysia). You can find two types, either analog or digital. This type of timer switch gives you the option to set “on-off” periods as many times as you want within the 24-hour period. You can use this type of timer switch to control not only lights but also other gadgets like water heaters and air-conditioners. I have two such timer switches installed in my home. One controls the light at the covered car porch (open-air garage with a roof). The other controls the sitting area (lounge) of my home. If you look at the photo of my timer switch, it is set “on” at 18.5 (6:30 p.m.) and “off” at 24 (12 midnight).
Factory-Preset Timer Switch: The other version is set such that when you switch it on, you can choose the time period for the “off” command. This timer switch can offer up to as many as six choices for the “on” duration. You can choose from 1 minute, 5, 10, 20, 30 and 60 minutes for the gadget to automatically switch off. I would say this is useful for those who are forgetful, or families with children, who more often than not, forget to switch off each time they leave the room. But then again, they may even forget or too lazy to push the “duration” button after switching on! Worse still, they may even press the wrong duration” button, either ending in total darkness or wasting electricity! So far, I have not seen this second version in my country.
|
|
|
The chemistry of cosmetics |
Geschrieben von: bop02mo - 02.04.2022, 02:15 - Forum: News
- Keine Antworten
|
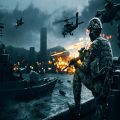 |
The chemistry of cosmetics
Cosmetics are not a modern invention. Humans have used various substances to alter their appearance or accentuate their features for at least 10,000 years, and possibly a lot longer.
Women in Ancient Egypt used kohl, a substance containing powdered galena (lead sulphide—PbS) to darken their eyelids, and Cleopatra is said to have bathed in milk to whiten and soften her skin. By 3000 B.C men and women in China had begun to stain their fingernails with colours according to their social class, while Greek women used poisonous lead carbonate (PbCO3) to achieve a pale complexion. Clays were ground into pastes for cosmetic use in traditional African societies and indigenous Australians still use a wide range of crushed rocks and minerals to create body paint for ceremonies and initiations.
Today, cosmetics are big business. According to the 2011 Household Expenditure Survey, conducted every five years by the Australian Bureau of Statistics, Australians spend around $4.5 billion on toiletries and cosmetic products every year. Cosmetic advertising, previously directed mainly at women, is now targeting a wider audience than ever.
What is a cosmetic?
In Australia, a cosmetic is defined under the Industrial Chemical (Notification and Assessment) Act 1989 as ‘a substance or preparation intended for placement in contact with any external part of the human body' (this includes the mouth and teeth). We use cosmetics to cleanse, perfume, protect and change the appearance of our bodies or to alter its odours. In contrast, products that claim to ‘modify a bodily process or prevent, diagnose, cure or alleviate any disease, ailment or defect’ are called therapeutics. This distinction means that shampoos and deodorants are placed in the cosmetics category, whilst anti-dandruff shampoos and antiperspirants are considered to be therapeutics.
Regulation and safety
In Australia, the importation, manufacture and use of chemicals—including those used in cosmetics—are regulated by the Australian Government’s National Industrial Chemicals Notification and Assessment Scheme (NICNAS). NICNAS works to ensure that chemicals used in consumer products do not cause significant harm to users or to the environment.
In the case of cosmetics, every ingredient contained within the product must be scientifically assessed and approved by NICNAS before being manufactured or imported into Australia and before they can be used in consumer products. Where appropriate, NICNAS sets limits on the level at which a chemical can be used in a product and also conducts reviews on chemicals when new evidence arises.
Introduction
Tianeptine is a tricyclic anti-depressant that is also known to have opioid receptor activity. We present two fatal cases of tianeptine intoxication in Texas in which tianeptine was used recreationally. The first case involved a 28-year-old white male found alone on the floor of his locked residence. He had a history of drug abuse but no other toxicological findings. The second case involved a 30-year-old white male found on the floor of the bathroom in his home. Drug paraphernalia and bags labeled as tianeptine powder were found at both scenes. In response to the first case, our laboratory developed a method for quantitation of tianeptine by LC–MS-MS. This method was then validated according to SWGTOX guidelines for specificity, calibration model, limit of detection, limit of quantitation, accuracy, precision, ion suppression, and carryover. This method was successfully used to determine tianeptine concentrations in postmortem blood in two cases.
Microneedles Could Enable Painless Injections and Blood Draws
Barely visible needles, or “microneedles,” are poised to usher in an era of pain-free injections and blood testing. Whether attached to a syringe or a patch, microneedles prevent pain by avoiding contact with nerve endings. Typically 50 to 2,000 microns in length (about the depth of a sheet of paper) and one to 100 microns wide (about the width of human hair), they penetrate the dead, top layer of skin to reach into the second layer—the epidermis—consisting of viable cells and a liquid known as interstitial fluid. But most do not reach or only barely touch the underlying dermis, where the nerve endings lie, along with blood and lymph vessels and connective tissue.
Many microneedle syringe and patch applications are already available for administering vaccines, and many more are in clinical trials for use in treating diabetes, cancer and neuropathic pain. Because these devices insert drugs directly into the epidermis or dermis, they deliver medicines much more efficiently than familiar transdermal patches, which rely on diffusion through the skin. This year researchers debuted a novel technique for treating skin disorders such as psoriasis, warts and certain types of cancer: mixing star-shaped microneedles into a therapeutic cream or gel. The needles' temporary, gentle perforation of the skin enhances passage of the therapeutic agent.
Many microneedle products are moving toward commercialization for rapid, painless draws of blood or interstitial fluid and for use in diagnostic testing or health monitoring. Tiny holes made by the needles induce a local change in pressure in the epidermis or dermis that forces interstitial fluid or blood into a collection device. If the needles are coupled to biosensors, the devices can, within minutes, directly measure biological markers indicative of health or disease status, such as glucose, cholesterol, alcohol, drug by-products or immune cells.
Here's the big caveat: many of those exciting supplement studies were observational—they didn't test a particular supplement against a placebo (inactive pill) in a controlled setting. The results of more stringent randomized controlled trials haven't yielded the same good news.
"Often the enthusiasm for these vitamins and supplements outpaces the evidence. And when the rigorous evidence is available from randomized controlled trials, often the results are at odds with the findings of the observational studies," explains Dr. JoAnn Manson, chief of preventive medicine at Brigham and Women's Hospital, professor of medicine at Harvard Medical School, and principal investigator of a large randomized trial known as VITAL (Vitamin D and Omega-3 Trial).
Because observational studies may not fully control for dietary factors, exercise habits, and other variables, they can't prove whether the treatment is responsible for the health benefits. "People who take supplements tend to be more health conscious, exercise more, eat healthier diets, and have a whole host of lifestyle factors that can be difficult to control for fully in the statistical models," Dr. Manson says.
Some supplements that were found to have health benefits in observational studies turned out, with more rigorous testing, to be not only ineffective but also risky. Vitamin E, which was initially thought to protect the heart, was later discovered to increase the risk for bleeding strokes. Folic acid and other B vitamins were once believed to prevent heart disease and strokes—until later studies not only didn't confirm that benefit but actually raised concerns that high doses of these nutrients might increase cancer risk.
How to get your nutrients
We need a variety of nutrients each day to stay healthy, including calcium and vitamin D to protect our bones, folic acid to produce and maintain new cells, and vitamin A to preserve a healthy immune system and vision.
Yet the source of these nutrients is important. "Usually it is best to try to get these vitamins and minerals and nutrients from food as opposed to supplements," Dr. Manson says.
Fruits, vegetables, fish, and other healthy foods contain nutrients and other substances not found in a pill, which work together to keep us healthy. We can't get the same synergistic effect from a supplement. Taking certain vitamins or minerals in higher-than-recommended doses may even interfere with nutrient absorption or cause side effects.
Suspicious and shady sellers peddle sex enhancement medicines at makeshift stalls on the street or through online sources, exploiting the insecurities and anxieties of consumers. They may make exaggerated claims that their products are “all natural” and can "prolong your sexual stamina" or miraculously cure medical conditions such as erectile dysfunction or impotency. However, the risks from taking these products may lead to serious side effects, including death.
Why sexual enhancement products bought from dubious sources are dangerous and should be avoided:
They may be counterfeit. Sexual enhancement medicines such as sildenafil, tadalafil and vardenafil are prescription medicines which should only be obtained from doctors or from pharmacists with a doctor’s prescription. Such medicines sold by dubious sellers can be counterfeit or fake. These products may be contaminated, contain the wrong ingredient or wrong amount of the ingredient, or contain no active ingredient.
They are of poor quality and may contain undeclared prescription medicines. Products from dubious sources are often produced under poor manufacturing conditions with no quality control by unscrupulous persons who have little regard for human health. They usually contain undeclared western medicinal ingredients or toxic ingredients in varying proportions (e.g. there could be an overdose), or contain ingredients not stated on the packaging.
They are not guaranteed to work. The claims made regarding the effects of illegal products should be viewed with caution, as they are not backed by scientific evidence or clinical studies.
Medical conditions require proper diagnosis and treatment. There are many causes for erectile dysfunction, including chronic illnesses, psychological factors and poor lifestyle. A medically trained professional can help to diagnose the root cause and work with you on appropriate treatments. In addition, medicines used in the treatment of erectile dysfunction are prescription-only medicines and should only be used under strict medical supervision as they may not be suitable for individuals with certain medical conditions and can cause serious side effects.
|
|
|
ALL YOU NEED TO KNOW ABOUT PRECISION INVESTMENT CASTING |
Geschrieben von: bop02mo - 02.04.2022, 02:14 - Forum: News
- Keine Antworten
|
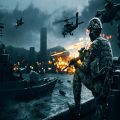 |
ALL YOU NEED TO KNOW ABOUT PRECISION INVESTMENT CASTING
Precision Investment Casting, also referred to as lost wax casting, is a process in which metals are casted into different shapes using wax and ceramics to act as the mould for the casting. This is one of the oldest known techniques for metal casting and has stood the test of time over centuries.
It finds usage in various industries like firearms industry, energy industry, gas and oil and even food industry. While many debate upon the strength and durability of this form of casting, doubting mainly that this method might provide weaker metal shapes as compared to forging or metal fabrication, these doubts have been laid to rest since aerospace, defence and medical fields have trusted equipment that are made from Precision Investment Casting.
WHAT IS THE PROCESS FOR PRECISION INVESTMENT CASTING?
As mentioned earlier, the process for Precision Investment Casting requires wax and ceramics to be the mould for the main metal. This is done in a very simple yet precise way (hence the name) and the steps are:
? Pattern Formation –Manufacturing of the wax pattern is the very first step involved in investment casting. Here it should be mentioned that wax is preferred over plastic, because wax melts easily and can be reused for another casting which is again a beneficial point from costing aspect. Special aluminium moulds are made to cast the pattern and this requires some trial and error, because factors like shrinking of the wax, the ceramic or even the metal should be incorporated.
The hard facts on marine hardware and components
While it may seem like a proportionally small detail for an overall marine fabrication project, finding the best hardware can significantly prolong the lifespan of an end product and tailor it to a specific customer’s needs. The technology for marine hardware is always changing, and it can be hard to keep up with the new products in the gap between trade shows. We caught up with a few of the nation’s most successful manufacturers and distributors to find out what’s hot this summer, and what fabricators can do to stay in the loop on the latest hardware products available.
The development cycle
Manufacturers insist that input from marine fabricators, regardless of the size of the shop they run, is key to developing new and more technologically advanced hardware. However, the process for developing a new item can take upwards of three years.
What’s hot
Because of the lengthy testing period, some of the marine hardware just entering the market now are products that have been around for a year or more—but manufacturers say that should help fabricators feel confident that these “hot” new products are road-tested and trade-show approved.
Alan Butcher of Intermold says his company is seeing rising popularity in two of its more versatile products: a new Lever Lock Joiner that securely fastens the telescoping support poles of an awning without having to use screws, and a universal deck hinge that can adapt to a wide variety of boat decks.
“There’s a whole bunch of deck hinge combinations out there, which is one reason we made the universal deck hinge,” Butcher says. “It swivels, and it fits a lot of different deck combinations, so the customer doesn’t have to have the exact angle. In the past they’ve had to slip wedges under them to change the angle of a hinge, because every deck has a little bit different camber to it. So we added a universal hinge that will adjust to whatever deck you put it on, and many customers have found that to be to their advantage.”
Tom Koster also emphasizes the importance of being able to offer versatile hardware. He says that one of his most popular new products is a ball and socket fitting, which can help a fabricator to fit a frame around the curved edges and adapt to new kinds of boats.
“Boats used to be more or less a lot of right angles, or straight angles, but now boats are manufactured with compound curves,” Koster says. “So when you put a frame down, it isn’t a straight line, because the boat itself is curved, the fittings have to be flexible, and allow movement within the hinge itself.”
The newest product we found has only been in development for 18 months, and is just being placed on the market for the first time: YKK’s new adhesive snap fastener, called the Snad. Rod Helwig of YKK says that the Snad was developed as a response to fabricators’ concerns about traditional snap applications.
The Stainless Steel Handrail Bracket Round for round or flat handrail. Sleek in design, easy to install and is safe and sturdy upon completion. It benefits from our new interchangeable mounting mechanism which makes it easy to mount to various surfaces such as Wood/Sheet Rock, Steel or Glass.
Suitable for flat or round top rail (adapter included)
Satin/Brushed Finish Stainless Steel AISI 316 Marine Grade for outdoor and indoor areas
Suitable for round handrail of 1 1/2" to 1 3/4" diameter
Suitable for wood or steel handrail
Mountable into wood stud, steel stud, or concrete
What are metal products?
The steel industry, the business of processing iron ore into steel, which in its simplest form is an iron-carbon alloy, and in some cases, turning that metal into partially finished products or recycling scrap metal into steel. The steel industry grew out of the need for more durable and more easily produced metals. Technological advances in steelmaking during the last half of the 19th cent. played a key role in creating modern economies dependent on rails, automobiles, girders, bridges, and a variety of other steel products.
Austgen - Metal Fabrication
Iron working can be traced as far back as 3,500 BC in Armenia. The Bessemer process, created independently by Henry Bessemer in England and William Kelly in the United States during the 1850s, allowed the mass production of low-cost steel; the open-hearth process, first introduced in the United States in 1888, made it easier to use domestic iron ores. By the 1880s, the growing demand for steel rails made the United States the world's largest producer. The open-hearth process dominated the steel industry between 1910 and 1960 when it converted to the basic-oxygen process, which produces steel faster, and the electric-arc furnace process, which makes it easier to produce alloys such as stainless steel and to recycle scrap steel.
After World War II, the U.S. steel industry faced increased competition from Japanese and European producers, who rebuilt and modernised their industries. Later, many Third World countries, such as Brazil, built their own steel industries, and large U.S. steelmakers faced increased competition from smaller, nonunion mills ( mini-mills ) that recycle scrap steel. The U.S. produced about half of the world's steel in 1945; in 1999 it was the second-largest producer, with 12% of the world market, behind China and ahead of Japan and Russia.
Since the 1970s, growing competition and the increasing availability of alternative materials, such as plastic, slowed steel industry growth; employment in the U.S. steel industry dropped from 2.5 million in 1974 to less than a million in 1998. Global production stood at 773 million tons in 1997, down from 786 million tons in 1988. U.S. steel production has remained constant since the 1970s at about 100 million tons, but mini-mill companies now produce 50 % of that total. An increase in U.S. demand during the 1990s was largely met by imports, which now account for from about a fifth to a quarter of all steel used annually in the United States. The old-line U.S. steelmakers, losing market share and with a higher wage, health, and retirement costs, experienced a string of bankruptcies beginning in the late 1990s, leading to industry and union pressure for protective tariffs, which were imposed by President George W. Bush in 2002 on most steel from non-NAFTA industrialised nations. Later reduced, the tariffs were found in 2003 to be illegal under World Trade Organization rules, and President Bush reversed the tariffs.
The Metal Industry is primarily concerned with metallurgy and metalworking. At first, the metals are extracted from the metal-ores found in their natural state deep within the earth. Then these ores are purified through a detailed procedure to obtain the metals in their pure form, and these processes comprise metallurgy. Then the pure form of the metal so obtained is used to manufacture structures as well as different machines and parts of machines. The procedures which involve the manufacturing of machines and other useful items from the metals so obtained through the metallurgical processes, constitute metalworking.
The manufacturing of alloys is also carried out in the Metal Industry through the proportionate homogeneous mixing of two or more metallic elements (metals in the pure state). The alloys so formed are mainly manufactured in order to enhance the natural properties of the metals by combining them together. Steel is one of the most popular as well as useful alloys of iron, formed through the chemical combination of mainly iron and carbon. In addition, it may also contain other metals, as added to the combination in order to attain desired properties from the alloy.
Metals are commodities without which a modern industrialised economy could not exist. Iron and steel, in particular, are ubiquitous and are central to meeting basic needs such as housing and mobility. Basic metal production encompasses the activities of smelting or refining ferrous and precious as well as other non-ferrous metals from ore or scrap, using metallurgic techniques. It also comprises the production of metal alloys and super-alloys by adding certain chemical elements to pure metals. The output of smelting and refining, usually in ingot form, is used in rolling, drawing and extruding operations to make products such as plate, sheet, strip, bars, rods, wire, tubes, pipes and hollow profiles, and in molten form to make castings and other basic metal products.
|
|
|
How Does a Metering Pump Work? |
Geschrieben von: bop02mo - 02.04.2022, 02:10 - Forum: News
- Keine Antworten
|
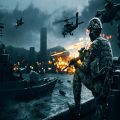 |
How Does a Metering Pump Work?
Metering pumps, also called dosing pumps, are pumps that are designed to dispense specific amounts of fluid and measured flow control. They use expanding and contracting chambers to move the liquids. Metering pumps also have a high level of accuracy over time and can pump a wide range of liquids including corrosives, acids, and bases, as well as slurries and viscous liquids. They are used in various industries like manufacturing, agriculture, and medicine. There are a variety of types of metering pumps that work in different ways. For the purposes of this post, we’ll look at diaphragm and peristaltic metering pumps.
How Diaphragm and Peristaltic Metering Pumps Work
Both types of metering pumps – diaphragm pumps and peristaltic – are very useful and will typically provide many years of reliable, efficient operation.
Diaphragm Metering Pumps
Diaphragm pumps are positive displacement pumps that move liquids using a reciprocating diaphragm. They are found to be very reliable because they don’t have internal parts that rub together, creating friction and leading to wear and tear. Additionally, because they don’t require seals or lubrication in the pump head, there isn’t a chance of oil vapor contamination or leakage of the media being pumped.
Simple diaphragm pumps have a diaphragm, two valves, a displacement chamber, and a driving mechanism. The diaphragm is a flexible membrane that vibrates to create suction to move fluid in and out of the pumping chamber. It is located between the side of the displacement chamber and an attached flange. The two valves are usually flapper valves or spring-loaded ball valves that are made of the same material as the diaphragm. They operate by admitting the liquid in and out of the chamber. The driving mechanism is what activates the diaphragm into operation. There are a number of different driving mechanisms that diaphragm pumps may use. The two most common are air operated and motor driven.
Air operated diaphragm metering pumps use compressed air to drive a double diaphragm (two diaphragms) alternatively. A shuttle valve alternates the air flow between the two diaphragms. The flow of the media that is being pumped is adjusted by how much air pressure is supplied to the pump.
Motor driven diaphragm metering pumps uses the rotary motion of a motor, which is converted to a reciprocating movement via a cam mechanism, to cause a displacement in the volume of the liquid, transferring it at a consistent rate.
Peristaltic Metering Pumps
Peristaltic metering pumps, like diaphragm metering pumps, are positive displacement pumps. However, they operate quite differently. Peristaltic pumps use rotating rollers to squeeze a flexible tube to move the liquid in a pressurized flow. As the tube is constricted and the low-pressure volume increases, it creates a vacuum that pulls the liquid into the tube. The liquid is then pushed through the tubing as the tubing is constricted at several points by the rollers. With each oscillating or rotating motion, the fluid flows through the tubing. Peristaltic metering pumps are designed as either circular (rotary) or linear.
Benefits of Metering Pumps
Metering pumps, whether diaphragm or peristaltic, provide many benefits to the industries where they are used. They are reliable for dispersing the exact amount of liquid that is needed accurately and consistently. Additionally, you will find the following advantages when using metering pumps:
They commonly move low amounts of liquid – Because metering pumps are so accurate and precise, they are often used to move low amounts of fluid. They are typically measured by their capability to pump gallons per minute, instead of gallons per hour, which is an industry standard.
They can pump various types of liquid – Metering pumps are able to move a variety of fluids, from thin to thick, and even hazardous or corrosive chemicals.
They can be used for many different applications – Metering pumps are used in many different industries including medicine, food processing, agriculture, and manufacturing.
They prevent contamination – Both diaphragm and peristaltic metering pumps are effective in preventing the media being pumped from contaminating the pump and the workspace.
While metering pumps work effectively for many applications and different liquids, it isn’t recommended that they be used for moving most types of gases.
Pressure and back pressure
High pressures are no problem in metering systems as long as there is something to counter them. ProMinent hydraulic diaphragm metering pumps therefore use a hydraulic fluid to create back pressure. The benefits this brings to the diaphragms become evident very quickly.
The industries in which ProMinent’s hydraulics technology is used:
- Oil/gas production (onshore/offshore)
- Refineries
- Chemical / petrochemical industry
- Pharmaceuticals & cosmetics
- Food production
- Packaging industry (bottling pumps)
[size=undefined]
What you can expect
The pumps run. They do this well and for a long time. Your hydraulic control is very precise and requires only minimal maintenance. The diaphragms are durable and provide consistently accurate metering. The technology also offers a very high standard of safety: there is a pressure relief valve in the hydraulic end as protection against overload. The multi-layer diaphragms are equipped with a diaphragm rupture warning system as standard. So you can be sure that the feed chemicals cannot mix with the hydraulic oil.[/size]
Pump Guide
The choice of pumps is huge: 80 industries, 100,000 products and infinite applications. To make it easy to find your ideal metering pump, ProMinent designed the Pump Guide. In just a few clicks you will find a selection of suitable models.
Here’s how it works
First enter the pump capacity and back pressure. The Pump Guide will then show you all the metering pumps that match your criteria. You can choose between list view and detail view. The database contains all solenoid metering pumps, motor-driven metering pumps, process metering pumps and peristaltic pumps from ProMinent. They are divided into more than 30 different product ranges.
Exactly the right pump
Narrow down your search by clicking on different selection criteria. Do you have a specific industry, operating mode, medium or viscosity in mind? Or maybe you need a pump for zones at risk of explosion? The Pump Guide will take you to the pump you need in just a few clicks.
Small-scale reverse osmosis plants that can produce less than 50 m 3 /d are vital for small communities in villages located in remote areas. The design parameters of such plants involve low flow rate and high-pressure feed. For such operating conditions, reciprocating pumps are more favorable than centrifugal pumps because the efficiency of centrifugal pumps in such conditions is reduced extensively. Recently, reciprocating pumps with energy recovery are presented by several pump companies for desalination applications. The concept of energy recovery in these pumps is quite similar to that used in pressure exchangers. In these pumps, the pressurized brine is directed to the back of the pumping pistons which reduces the pumping motor required power. This work presents a numerical simulation and experimental analysis for such pumps. The numerical simulation includes a computational fluid dynamics transient analysis for the used pump. The analysis is presented using both two-dimensional and three-dimensional models. The effects of the operational and design parameters on the performance of the pump and its volumetric efficiency are investigated. The results show that increasing the valve spring stiffness increases the volumetric efficiency. It also shows that increasing the outlet pressure and piston speed reduces the volumetric efficiency. The most striking result to emerge from the data is that reducing the valve spring stiffness below a specific value results in large reduction on the volumetric efficiency. Results of high-pressure reciprocating pump’s testing at different operating conditions are evaluated. The results of the presented numerical simulation were compared with the experimental results at several operating conditions, and the deviation was less than 10%.
What is a pneumatic diaphragm pump? An air operated double diaphragm pump is a pneumatic pump that uses a patented air valve that directs compressed air between two sides of the pump, back and forth. It can operate on regular compressed air, clean dry air, nitrogen, or even natural gas.
|
|
|
What is a Water Storage Tank and How Does It Work? |
Geschrieben von: bop01mo - 01.04.2022, 02:16 - Forum: Allgemein
- Keine Antworten
|
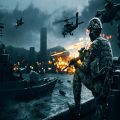 |
What is a Water Storage Tank and How Does It Work?
A water storage tank holds clean water from your reverse osmosis system or other filter systems until you're ready to use it. Pressurized storage tanks force water out on demand, while atmospheric tanks require a booster pump to supply pressure. Water storage tanks exist in a vast array of sizes, designs, and specifications, and can be used residentially, commercially, and for large-scale industrial or municipal enterprises.
What is a water storage tank?
A water storage tank collects water and stores it for later use and timely access. When you turn on your kitchen faucet, water is carried from the tank to your tap, providing you with fresh water on demand. Reverse osmosis systems work slowly, purifying water one drop at a time. A reverse osmosis storage tank ensures you can access this water whenever you need, without waiting for the system to painstakingly fill up your glass. Many wells are low-pressure and low-recovery and are tasked with providing pressurized water throughout a household or business. A well pressure tank ensures that when you turn your shower on or flush your toilet, you have immediate access to pressurized water. They also help extend the life of the well pump by protecting the pump from short-cycling.
Water storage tanks come in all shapes, sizes, and configurations, and are used for a variety of purposes across the water treatment industry. From a small, 5-gallon reverse osmosis tank stored neatly under your sink to a towering 120-gallon well pressure tank, water storage tanks are an integral part of many household water systems. Large, outdoor atmospheric tanks can store thousands of gallons of rainwater, well water, or be used for fire suppression. These tanks are usually equipped with UV inhibitors, preventing sunlight from facilitating algae and bacterial growth within the tank. Thermal expansion tanks prevent water heaters on closed water supplies from leaking and bursting.
How does a water storage tank work?
A water storage tank holds clean water from your reverse osmosis system until a demand for water is initiated in the house or business. Water is pumped into the tank from the water source, like a well or a reverse osmosis system. The tank accumulates water until it is full. When you need access to water, be it to fill your glass up with crystal clear water, run a bath, or irrigate a field, the storage tank provides you with instantaneous access to water.
Water storage tanks are generally either pressure tanks or atmospheric tanks. Point-of-use applications, like reverse osmosis storage tanks, usually implement pressure tanks. Outdoor applications or large scale municipal water storage operations usually use atmospheric tanks.
How do pressure tanks work?
Pressure tanks use compressed air to create water pressure within the tank. A pressure tank is constructed with an air chamber or bladder and comes with a pressure pre-charge. As the tank fills up with water, the weight of the water will begin to compress the air. As the air continues to compress, the pressure within the tank builds. When the tank reaches a certain internal pressure, it signals to the feed source to cease delivery. When you open a faucet in your kitchen, the air pressure bears down on the water as it is released from the tank, propelling pressurized water through your pipes and out of your kitchen sink. When water exits the tank, the air will start to expand again, reducing the tank pressure, and signaling to the water source to recommence delivery. If the pressure tank is being used to store well water, this means the tank will signal the well pump to turn back on. If the storage tank is collecting RO water, lowering pressure will signal the reverse osmosis system to restart production. These tanks are known as hydropneumatic tanks because they use the combined power of water and air to generate pressure within a tank.
Pressure tanks allow for pressurization without the aid of pumps. Since air will compress and water will not, the air within the tank will organically increase the pressure of the water as the tank fills up. There are also pressure tanks that do not rely on hydropneumatic pressure. These are known as constant pressure tanks. Constant pressure tanks provide city-like water pressure at all times, regardless of how many appliances are demanding water. A hydropneumatic tank can become overwhelmed if too much water is being drawn from it and sent to multiple sources concurrently (for example, if the shower is running at the same time as the dishwasher.) This results in a loss of pressure throughout the home. Constant pressure tanks use a sensor to monitor water pressure and keep the water in the tank at a stable, consistent pressure.
The optimal shape and dimensions for mixing tanks can be summarized in two words: It depends.
While the various components of a mixing system are often manufactured separately, determining the optimal specifications for any one of them requires an understanding of the entire system. The tank’s ideal shape and dimensions and the agitator’s ideal size and location are interdependent – and they all depend on the system’s specific purpose.
To find the optimal shape and dimensions for a mixing system, it is important to keep that purpose in mind, while considering the advantages and disadvantages covered in this article.
Determining the optimal height
To find the optimal height to diameter ratio for a mixing tank, it is important to keep in mind the tank’s specific purpose. Generally, both narrow and wide tanks have their advantages and disadvantages.
The narrower a tank is, the better its heat transfer will be – a factor that can be critical for certain mixing scenarios. Additionally, wider tanks require wider agitators – and because wider agitators need more torque, they require larger shafts and gears, which are more expensive.
On the other hand, a narrower tank will require a higher-speed agitator with a longer shaft, giving the tank a lower critical speed – a factor that can be a major problem for certain mixing purposes.
Considering cylinders
Cylindrical tanks are a common choice, not least of all because they are relatively inexpensive to manufacture.
In a cylindrical tank with a centrally positioned agitator, low-viscosity liquids can begin to swirl – a phenomenon that can prevent a solution from becoming homogeneous. In order to prevent swirling, it is common to install a baffle within this type of tank. But while baffles are an effective solution to the problem of swirling, they also complicate the clean-in-place (CIP) process, making it take more time.
Working principle of different filling machines
Automatic filling machines can use a number of different filling principles to get the product into the bottle. Each filling principle has its own unique benefits or advantages. While more than one type of liquid filler may work for a given project, each project will ultimately have an ideal filling machine, or filling principle, for the job to be completed.
Overflow Filling Machine
The principle behind the overflow filling machine is the ability to fill to a specific level on each and every bottle, even if small discrepancies exist in individual bottles. This filling machine offers obvious aesthetic value to products that are packaged in clear containers, such as bottled water and window cleaners. As with all of the filling machines discussed in this article, overflow fillers can be manufactured to meet almost any production demand, as tabletop, semi-automatic or fully automatic bottle fillers.
The overflow filler will almost always be the ideal filling machine for products that are packaged in clear containers. However, the machine will be limited by the viscosity of the product. Overflow fillers work well with thin to medium viscosity products and even products that foam. Special nozzles allow the overflow filler to fill each and every bottle to the same level, regardless of slight differences in the interior volume of the container. For products in clear containers, a level, consistent fill leads to good shelf appeal, adding aesthetic value to the filling process.
Growth of conveyor systems
Conveyors are growing in use and popularity. The conveyor market is estimated to reach $10.07 billion by 2025, at a CAGR of 4.5% over the forecast period 2020-2025. In the commercial and civil sector’s businesses are rapidly increasing the implementation of conveyors at places like airports, shopping centres, stadiums, and restaurants.
Conveyors are highly popular in the manufacturing and packaging industries as well as production plants and with the amount of demand for these products going up, the systems excel at allowing businesses to meet consumer demand and for that reason are more in need in a manufacturing process than ever.
Commonly purchased type of conveyors are line shaft roller conveyors, chain conveyors, and a conveyor belt system.
Industries that use conveyor systems
It’s easy to see why an increasing amount of companies and industries are using conveyor systems with the numerous benefits they provide. We’ve listed some of the major benefits below.
Benefits of using a conveyor system
Can safely transport materials from one level to another through elevated conveyors
Can be installed in most situations while usually being able to add value and increase the safety of the workplace due to automation, failsafe’s, and safeguards
Conveyors can move high quantities of items in various shapes, sizes, and weights
Have advanced safety features that prevent accidents and injuries while increasing throughput of the system
Variety of options to run the conveying systems, including the hydraulic, mechanical, and fully automated systems which are equipped to fit individual needs
|
|
|
|