Hallo, Gast |
Du musst dich registrieren bevor du auf unserer Seite Beiträge schreiben kannst.
|
Benutzer Online |
Momentan sind 116 Benutzer online » 0 Mitglieder » 116 Gäste
|
Aktive Themen |
Wo kauft ihr ein?
Forum: Allgemein
Letzter Beitrag: marco91
27.05.2025, 14:49
» Antworten: 1
» Ansichten: 141
|
Streamingzimmer einrichte...
Forum: Allgemein
Letzter Beitrag: marco91
27.05.2025, 14:30
» Antworten: 1
» Ansichten: 111
|
Werbebriefe?
Forum: Allgemein
Letzter Beitrag: fritz500
12.05.2025, 17:56
» Antworten: 1
» Ansichten: 192
|
Auto privat verkaufen?
Forum: Allgemein
Letzter Beitrag: fritz500
12.05.2025, 16:21
» Antworten: 1
» Ansichten: 173
|
Vape welche Sorte?
Forum: Allgemein
Letzter Beitrag: conradme
05.05.2025, 20:52
» Antworten: 1
» Ansichten: 206
|
Was tun in Hamburg?
Forum: Allgemein
Letzter Beitrag: conradme
05.05.2025, 19:32
» Antworten: 1
» Ansichten: 202
|
Automatisierung in der In...
Forum: Allgemein
Letzter Beitrag: maxmeyers
25.03.2025, 13:20
» Antworten: 1
» Ansichten: 610
|
Kurzwaren im Internet?
Forum: Allgemein
Letzter Beitrag: fritz500
25.03.2025, 08:54
» Antworten: 1
» Ansichten: 526
|
Mittel gegen schwitzen?
Forum: Allgemein
Letzter Beitrag: fritz500
25.03.2025, 08:00
» Antworten: 1
» Ansichten: 535
|
Sportbootführerschein onl...
Forum: Allgemein
Letzter Beitrag: marco91
24.03.2025, 22:16
» Antworten: 1
» Ansichten: 512
|
|
|
How does an hourglass measure time? |
Geschrieben von: bop03mo - 06.04.2022, 02:41 - Forum: Allgemein
- Keine Antworten
|
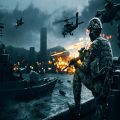 |
How does an hourglass measure time?
The sand timer hourglass is sometimes referred to as a sand clock or a sandglass. Like other timepieces, it needs to be carefully calibrated. The hourglass maker must test the instrument and fine tune it to measure the correct length of time.
There are many factors that contribute to the ability of an hourglass to accurately measure time. The type and quality of sand is key. It must have a rate of flow that does not fluctuate. Sand that is too coarse will wear away the glass, eventually making the neck too large. Most important is the ratio of the neck (the hole, or tube) width to the diameter of the sand particles.
Here are the other factors that affect the accuracy of an hourglass:
The amount or volume of sand used
The size and angle of the glass bulbs
The quality of the sand or granular material. It must be fine, dry and consistently formed so it can flow smoothly. (Some substances used in the past were fine grain sand, powdered eggshells, and powdered marble.)
The width of the neck
A tight seal so no moisture can get into the chambers. Moisture can add weight to the sand or clog up the neck.
A flat and level surface on which to rest the hourglass
Like a foam roller, a massage ball can also be used to help release tension in our achy muscles after long hours spent in the office or after a workout. One of the differences being that it can get to those hard to reach areas such as the upper back, buttocks and feet. “Knots” or “trigger points” can be massive sources of pain in our bodies and using self-massage techniques can be very satisfying. Before diving in, there are a few important things to know which will help you achieve the best results.
Why a massage ball
Massage balls are affordable and small and therefore they can easily fit into a suitcase or handbag to use wherever you go. They also promote self-sufficiency so there is no need to rely on anyone else. Notwithstanding, it does not always give the same results as a traditional massage delivered by an experienced therapist
Find the right ball
There are many different types of massage balls ranging from very smooth and firm like a lacrosse ball to small and soft like a squash ball. Other balls include a tennis ball and the trusty spikey massage ball. To each his own but if you’re new to using a massage ball, perhaps start with a spikey ball or a tennis ball.
Where and when
Since they are so conveniently easy to use, you can use them almost anywhere for example against a wall, the back of a chair, on the floor or use your hands. Some office workers keep them at their desks as a reminder to use them during the day to help with releasing built-up muscle tension from poor posture or stress.
How
Start with only a few knots at a time, the most painful area being first. The idea is to trap the knot in the muscle with the ball and apply gently to medium pressure until the painful sensation has faded. Once you have the correct spot (and you will know when), hold it there and try to relax until only about 80% of the ache remains. When pressing too firmly, the sensation can be too painful for you to relax which defeats the purpose of using the massage ball in the first place, it could also potentially irritate the area. You are looking for a “good pain”.Roll the ball around to look for more tender spots or just enjoy gently going back and forth over the tight muscle. If you feel the muscle needs it, you can repeat it twice a day. After releasing the knot, follow it up with gentle stretches to the same muscle. It’s okay to lightly exercise the muscle afterward but avoid fatiguing it for 24 hours.
“The Crown Jewels for Collectors” — that’s what Paul Hollister wrote about fine glass paperweights. He was one of the foremost scholars of 17th to 19th century glass studies, glass paperweights, and contemporary studio art glass. Paperweights are considered the most collectable of 19th century glass items, and also the most challenging of the glass arts to make. Fine glass paperweights are, indeed, rare treasures.
Most antique paperweights of quality were made by one of three French factories, as a sideline, for just 10-15 years in the mid-1800s. It’s estimated that only about 25,000-30,000 remain today, with many tightly held in museum collections. Fine contemporary paperweights are made by a limited number of studio artists and are sold either by the artist, or by a small group of specialty dealers.
History
The mid-to-late 1800s were sentimental and romantic times, heralded by an emerging middle class, resulting from the matured Industrial Revolution. Letter writing became a fad, and paperweights were sold in stationery stores as an attractive accessory to desk-sets of pens, inkwells, blotters, and fine stationery. The first glass paperweight was made in 1845 by Venetian glassmakers in response to the letter-writing fad. They could have been made 300 years earlier because the techniques were known, but paper was then a rare commodity and there was no need for a paperweight. They are the perfect example of form following function.
American made paperweights followed from 1851 into the late1880s, by the Boston and Sandwich Glass Company, and the New England Glass Company — and more rarely by makers including Dorflinger, Mount Washington, Gillinder, and Whithall Tatum companies. Their glassmakers were mainly European immigrants already skilled in the craft, which explains why American weights are somewhat imitative of the European. What American weights may have lacked in quality, they more than made up for in creativity and ingenuity, which makes them even more charming to their collectors.
What does iCloud Keychain do?
When you enter a new password in Safari, you’ve probably seen iCloud Keychain ask if you would like it to save it for use across all your devices. So long as you are running iOS 7.0.3 or later or OS X Mavericks 10.9 or later, iCloud Keychain will store the following items securely in iCloud. Once secured in iCloud Keychain, you will be able to access all these items securely from any Apple system logged into your Apple ID.
ADVERTISEMENT
Safari website usernames and passwords
Credit card information
Wi-Fi network information
Ensure Mail, Contacts, Calendar and Messages are synced across all your devices
Protect, access and deploy your LinkedIn, Twitter and other Internet account logins and passwords.
How does iCloud Keychain work?
iCloud Keychain must be enabled on each device. Devices that are not enabled for the service will not be able to access the information it holds, so you’ll need to enter your passwords and other details manually.
How do I use iCloud Keychain in Safari?
When registering for a new website or service you will be asked to enter your information in the site’s registration fields. iCloud will populate these fields with things such as your name and telephone number. You will also be asked to create a password by entering your new password in the password field and the password confirmation field. When you tap your cursor in the first of these fields you will see a small item appear, tap this to use an iCloud supplied password. In practice, if you use your own password or one supplied by iCloud, it should be stored for later use by your iCloud Keychain.
How do I add credit card details to iCloud Keychain?
You can also add your credit card details to iCloud Keychain. You can choose to follow on-screen prompts to do so automatically as and when they appear, or enter these details manually as follows:
On a Mac: Open Safari’s AutoFill item in Preferences. Look for the Credit Cards item and tap Edit. In the next screen, you will be able to add and delete new cards. Tap Done.
On iOS: In Settings, open Safari>Autofill. Here you can choose to enable or disable Autofill of names and passwords, and as well as control what credit card information is held. Tap Saved Credit Cards, and you will be able to add or delete your stored credit card information. Tap Done.
The fabrication of the early spherical shells was limited to free forming of small hemispheres from thin acrylic sheets by compressed air. But even with all the limitations, the ocean engineering community saw the advantages acrylic offered to panoramic visibility.
Actual diving systems with the all-acrylic pressure hulls which demonstrated this potential were HIKINO, KUMUKAHI, and NUCOTE.
HIKINO was conceived in 1962 by the late Dr. William McLean and engineered by D.K. Moore of NOTS, China Lake. The two-person vehicle had the shape of a catamaran with the acrylic sphere suspended between the two hulls. The acrylic sphere itself was assembled from two free-formed hemispheres mated at the equator to a metallic joint ring.
The vehicle successfully demonstrated the design concept of panoramic visibility but because it was free formed from thin commercially available sheets, the design depth was only 20 feet. As a result of this severe limitation, it was subsequently used only as a concept demonstrator in a shallow swimming pool.
KUMUKAHI was conceived in 1967 by T.A. Pryor, engineered by Will Forman, fabricated by Fortin Plastics, and delivered to Oceanic Institute in Hawaii in September 1969. The submersible was configured as a self-propelled diving bell with the batteries and a variable displacement tank contained in a pod suspended directly under the sphere.
|
|
|
How to Determine the Appropriate Mobile or Handheld Metal Analyzer for On-the-Spot Me |
Geschrieben von: bop03mo - 06.04.2022, 02:40 - Forum: Allgemein
- Keine Antworten
|
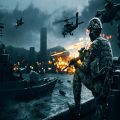 |
How to Determine the Appropriate Mobile or Handheld Metal Analyzer for On-the-Spot Metal Testing Tasks
For metal producers, processors, recyclers, contractors and others, continuous quality control plays a key role in establishing the identity and composition of various metals and alloys from initial melt to finished product or end use. Metals and alloys need to be accurately sorted, identified, and verified at each stage of the process to make certain they meet specific customer and/or industry requirements for physical and chemical composition.
For businesses that perform metal production, processing, recycling, or service contracting, an alloy mix-up at the shipping dock or on the factory floor risks an expensive, inconvenient batch rework or the possibility of a catastrophic loss of business. Fortunately, metal inspection has been made easy, accurate and affordable with the availability of portable, mobile optical emission spectroscopic (OES) metal analyzers and handheld X-ray fluorescence spectrometers.
When it comes to metals specifications, the news is full of reports of mistakes, mismeasurements and other related scandals by a host of industries. It’s increasingly clear that quality-conscious organizations can’t afford to hand off responsibility for metals verification. The inspection of the metal makeup of incoming and outgoing components is a critical quality control (QC) task for companies worldwide.
While the focus of this article is on steels, non-ferrous alloy users are confronted with similar situations and are required to perform similar testing tasks. Some steel products are easy to analyze. For many suppliers and end users, testing with a handheld X-ray fluorescence (XRF) or simple handheld optical emission spectrometry (OES) analyzer is adequate. Their size and relatively low initial costs have created great interest in these handheld analyzers, which produce fast results for on-the-spot alloy identification, grade sorting or verification.
In many cases, the presence or absence of an alloying element in a steel component is critical to its performance but impossible to detect by physically inspecting the item. Positive material identification (PMI) has become accepted practice for the process and equipment supply industries. The industry-standard approach for achieving efficient PMI is via elemental analysis of the materials.
Slag Analyzer presents a uniquely compact and reliable WDXRF platform configured with Thermo Scientific SmartGonio for analysis of slags and pig iron. This small but powerful instrument comes with factory installed calibration for slags using Jernkontoret standards. Its quick start-up, ease of use, and analytical flexibility provide unparalleled value for iron & steel laboratories.
? New: 500W equivalent analytical performance from 200W X-ray power
? 200W equivalent analytical performance from 50W X-ray power
? High precision, outstanding repeatability and stability to comply with slag analysis requirements
? Pre-calibrated turnkey solution for routine slag analysis
? Lowest cost of ownership thanks to low operating cost, highest reliability and minimal auxiliary equipment
? Optional Multichromators for faster analysis or better performance on selected elements
? Innovative UCCO technology combined with SmartGonio to achieve highest sensitivity
Oil Analysis Can Enhance Your Bottom Line
Oil analyzer offers many benefits. Through regular testing of lubricants, you can:
Enhance equipment life and reliability by ensuring proper lubrication and detecting issues such as excessive wear and contamination
Extend lubricant life by monitoring its condition and, when deemed necessary, treating or cleaning it, typically allowing for longer intervals between fluid changes
Reduce equipment downtime by spotting and correcting potential lubrication problems before they become serious issues
Seven Keys To Effective Oil Analysis
Follow these seven simple steps to help maximize the benefits of oil analysis:
Identify the equipment critical to your operational productivity. At the bare minimum, the lubricants in those components should be analyzed regularly. (Ideally, all lubricants in use at your facility should be tested regularly.)
Register the equipment with the lab. This will help the lab identify appropriate tests for your specific application. Registration also facilitates trending.
Use proper sampling procedures. Improper sampling may produce erroneous test results. Problems could be missed and go untreated, leading to costly problems later. Or conditions may be misdiagnosed, resulting in incorrect, unnecessary and money-wasting actions being taken to correct a nonexistent issue.
Provide complete and accurate information with each sample you submit to the lab. Missing or inaccurate information may lead to a misdiagnosis. Complete all fields on the submission form, including the specific lubricant in use, the component it services, the hours the oil has been in use, and more. Also ensure that the information is legible to help avoid misinterpretation.
Submit samples promptly to the laboratory for analysis. Although a delay inherently has virtually no effect on the sample itself, it does increase the potential for contamination. Also, the condition of the oil in use in the equipment will continue to change over time. The more time that passes between when the sample is taken and when it is analyzed, the less alike the sample will be to the fluid still flowing in the machine. Therefore, the results of the analysis will have less relevance.
Review and respond to test results appropriately. Promptly review the analysis documentation to determine what, if any, action is necessary.
Use oil analysis regularly, not just when you suspect a problem. As part of a preventive maintenance program, regular oil analysis establishes a baseline for monitoring the condition of your lubricants and the components in which they are used. Much like routine, periodic medical screenings, the regular collection of analysis data over time may help identify trends and spot potential complications in early stages, so that they can be corrected and not become big problems.
How do we measure static gel strength development?
Historically, the SGS of a cement slurry was determined by a method using a couette-type rotational viscometer. Today, more specialized instruments have been developed that allow the measurements to be done under conditions of high temperature and pressure.
API-10B6 was developed to establish the testing protocols to determine SGS by different mechanisms, including a rotating-type apparatus, an intermittent rotation-type apparatus and an ultrasonic-type apparatus (removed in the latest API adoption due to patents exclusivity).
Test method using rotating-type static gel strength apparatus
The apparatus contains a pressure chamber that can be heated and pressurized according to a simulated cement job schedule. The SGS is calculated from the torque required to rotate a paddle of known geometry at very low speed. The rotation speed of the paddle during the SGS measurement portion of the test is usually a continuous 0,2 r/min. The initial stirring to simulate placement in the well is typically conducted at 150 r/min.
Test method using intermittent rotation-type static gel strength apparatus
This apparatus works on the same principles/methods as the previous one with the sole difference that this it operates intermittently during the SGS testing phase at 0,01 r/min for 6s after a time interval adjustable between 1 min and 10 min. In general, an intermittent rotation every 3 min is used.
Test method using ultrasonic-type static gel strength apparatus
The instrument measures the static gel strength of API cement under high temperature and high-pressure conditions. The instrument is equipped with an internal processor board that sends and receives an ultrasonic pulse through the slurry, then performs post processing of the data to determine the static gel strength (SGS) versus time plot. Additionally, as an option, the instrument may be used to determine the compressive strength of the cement using the same algorithms and method found in a conventional Ultrasonic Cement Analyzer (UCA). This testing methodology was included in API10B6 original version but was later removed as it’s patent protected and exclusive to Chandler Ametek. The machine is known as Static Gel Strength Analyzer (SGSA).
Food security and why it matters
The global food security challenge is straightforward: by 2050, the world must feed 9 billion people. The demand for food will be 60% greater than it is today. The United Nations has set ending hunger, achieving food security and improved nutrition, and promoting sustainable agriculture as the second of its 17 Sustainable Development Goals (SDGs) for the year 2030.
To achieve these objectives requires addressing a host of issues, from gender parity and ageing demographics to skills development and global warming. Agriculture sectors have to become more productive by adopting efficient business models and forging public-private partnerships. And they need to become sustainable by addressing greenhouse gas emissions, water use and waste. The risks: malnutrition, hunger and even conflict.
Why is food security such a major global challenge?
The obvious reason is that everybody needs food. But the complexity of delivering sufficient food to a national population and to the whole world’s population shows why food security is such a priority for all countries, whether developing or developed.
In short, this is a global challenge because it’s not just about food and feeding people but also about practically all aspects of an economy and society.
|
|
|
High-Temperature Grease Guide |
Geschrieben von: bop03mo - 06.04.2022, 02:37 - Forum: Allgemein
- Keine Antworten
|
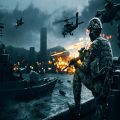 |
High-Temperature Grease Guide
There are many criteria to consider when selecting a high temperature grease for hot, grease-lubricated equipment.
The selection must include consideration of oil type and viscosity, oil viscosity index, thickener type, stability of the composition formed by the oil and the thickener), additive composition and properties, ambient temperature, operating temperature, atmospheric contamination, loading, speed, relubrication intervals, etc.
With the variety of details to resolve, the selection of greases that must accommodate extreme temperature conditions poses some of the more challenging lubrication engineering decisions.
Given the variety of options, the potential for incompatibility problems and high prices for a given high-temperature product, the lubrication engineer must be selective and discriminating when sourcing products to meet high-temperature requirements.
High-Temperature
‘High’ is relative when characterizing temperature conditions. Bearings running in a steel mill roll-out table application may be exposed to process temperatures of several hundreds of degrees, and may experience sustained temperatures of 250oF to 300oF (120oC to ±150oC).
Automotive assemblers hang painted metal parts on long conveyors and weave them through large drying ovens to dry painted metal surfaces. Operating temperatures for these gas-fired ovens are maintained around 400oF (205oC).
In these two cases, the selection criteria differ appreciably. In addition to heat resistance, the grease to be used in a hot steel mill application may require exceptional load-carrying capability, oxidation stability, mechanical stability, water wash resistance and good pumpability, and at a price suitable for large-volume consumption. With all of the important factors to consider, it is useful to have a grease selection strategy.
Selection Strategies
A reasonable starting point for selecting a high temperature grease is to consider the nature of the temperatures and the causes of product degradation. Greases could be divided by temperatures along the lines in Table 1.
There is general correlation between a grease’s useful temperature range and the expected price per pound. For instance, a fluorinated hydrocarbon-based (type of synthetic oil) grease may work effectively as high as 570oF (300oC) in space applications but may also cost hundreds of dollars per pound.
The grease’s long-term behavior is influenced by the causes of degradation, three of which are particularly important: mechanical (shear and stress) stability, oxidative stability and thermal stability. Oxidative and thermal stresses are interrelated. High-temperature applications will generally degrade the grease through thermal stress, in conjunction with oxidative failure occurring if the product is in contact with air. This is similar to what is to be expected with most industrial oil-lubricated applications.
Large production facilities have a variety of grease-lubricated equipment, ranging from steady-state applications to applications that vary significantly in speed and load, and operate in aggressive (wet or dusty) environments.
If machine designers address equipment lubrication needs based strictly on a dynamic loading requirement, they might have to specify a wide variety of greases to meet the many existing needs. In this approach, the added system complexity would likely increase the cost and the risk of failure due to misapplication and cross-contamination.
To maximize grease lubrication effectiveness, minimize cost and minimize risk of application-induced failure, lubricant manufacturers have made an effort to formulate greases that cover a variety of applications. These greases range from slow to high speeds, and from low to high loads, in an effort to provide a single product to meet a multitude of requirements. The result is general purpose grease.
What is General Purpose Grease?
A general purpose (GP) grease is designed to meet a broad range of requirements. It is grease manufactured to medium consistency with a medium viscosity base oil and medium wear, washout and oxidation resistance properties. Essentially, it is a product designed to fit the largest possible cross-section of grease lubricated components in an operation.
If the demand on the lubricated components in a plant could be rated on a curve according to speed, load and environment/application severity, the resulting curve would likely resemble a Pareto chart. The typical application in most plants does not severely challenge a GP grease. Some applications would be considered tough, and may or may not be suitable for a GP grease. A few extreme applications will require a grease with one or more special qualities.
The proportion of typical, tough and extreme applications might vary considerably. This distribution has no correlation to the criticality of the mission of the grease-lubricated machines. Many of the tough and most of the extreme applications will require a thorough technical review to determine what special lubricant properties might be required. Lubricant criteria are fairly narrow at the extremes of load and speed, and therefore may require products that do not suit the vast majority of lubricated components.
However, it is advisable to cover as many of the lubricated components as possible with as few products as possible. With this in mind, begin by examining the lubricated components for an average requirement and work selectively toward extremes in load and speed.
Equipment Properties to Consider
Given the wide range of characteristics that may exist in the greases at any given plant, it is best to first characterize the equipment and plant conditions, then select a general purpose grease to meet the conditions.
Equipment Condition Considerations
Keeping the objective in mind, a general purpose (GP) grease is used as a multi-application grease in a production process to reduce complexity and the potential for component failure due to misapplication. Consider the following operational characteristics when selecting the GP grease.
Size and Type
Ball screws, cables, linear bearings, plain bearings, rolling element bearings, slide-ways and seals are just a few of the many different component types that are grease lubricated. If sliding friction is the dominant contact type, then there may be a greater reliance on heavy viscosity oils, polymers and solid additives to support the load and provide lubricating film protection.
If rolling friction is the dominant contact type, then greases with lighter viscosity base oils and minimal use of polymers, solids and antiwear (AW) and extreme pressure (EP) additives can be effectively used.
Load
As the load increases, the grease’s base oil viscosity must also increase to support the load. If the majority of the components in the mill/plant environment are heavily loaded, it may make sense to use high-viscosity base oils for a general purpose product. This might be the case in a cement, steel or paper mill environment. It is not uncommon to find GP greases made from 460 cSt (40°C) and heavier oils in these types of environments.
Speed
As the speed increases or the load diminishes, the required base oil viscosity also diminishes. In operations with predominantly moderate to high-speed and lightly to moderately loaded applications, the grease’s oil viscosity would fall to an ISO 46 to 150 range. It is unusual to find highly loaded applications that also operate at high speeds that are lubricated with grease. This type of application would likely warrant special consideration and therefore fall outside this discussion.
Atmosphere
The three atmospheric factors that must be accounted for are temperature, moisture and airborne solid contaminants (particles). Although the influence of atmospheric factors can be significant, these factors are considered after the viscosity selection is complete.
Lubrication Intervals
The method of application combined with the application cycle dictates the rate of application. The rate of relubrication is the amount of lubricant fed into the component in a given time.
Greased components require a constant supply of lubricant at the load zone to sustain the hydrodynamic film much the same as oil lubricated components. The reserve grease contained in the cavity in the housing serves as an oil reservoir that components draw from for lubrication.
When grease is resupplied to the housing, the oil reservoir is replenished. The longer the duration between cycles, the greater the likelihood that the reservoir will deplete and the component will run to a semi-dry (mixed film) condition.
The oil in the load zone is squeezed and pushed away over time. If the relubrication volume is insufficient, or the cycle is sporadic (greater risk with manual lubrication), the likelihood that the oil film will dissipate leading to mixed film conditions increases. When these conditions are prevalent, the grease selection must be one that resists the squeezing action and tendency to dissipate. Greases formulated with heavier viscosity base oils and chemical and mechanical film forming additives can be helpful in these circumstances.
|
|
|
Air Force Research Lab orders 15 Silent Arrow unmanned cargo gliders |
Geschrieben von: bop03mo - 06.04.2022, 02:34 - Forum: Allgemein
- Keine Antworten
|
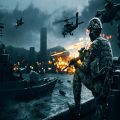 |
Air Force Research Lab orders 15 Silent Arrow unmanned cargo gliders
Looking for a new way to resupply ground troops, the US Air Force Research Laboratory (AFRL) has ordered 15 cargo glider drone/runway drone from Silent Arrow, a company of Yates Electrospace.
The AFRL ordered the “Silent Arrow Precision Guided Bundle”, a new glider variant that is a smaller version of the “Silent Arrow GD-2000” drone, which Silent Arrow built for the US Special Operations Command.
The smaller Precision Guided Bundle UAV will be able to be launched from aircraft side doors and cargo ramps. Aircraft capable of deploying the drones will include those as small as Cessna Caravan turboprops and as large as Boeing C-17 strategic airlifters, the company says.
The autonomous unmanned air vehicles (UAVs) will be built at the company’s Irvine site, then shipped north for operational evaluations in 2022 at Pendleton UAS Test Range in Oregon, Silent Arrow adds.
The Silent Arrow line of cargo gliders have spring-loaded wings that fold for storage and deploy for flight. The type is advertised as being cheaper than the US Army’s Joint Precision Airdrop System, a GPS-guided parachute system used for delivering cargo.
The un-powered Precision Guided Bundle has a 34.8nm (64.4km) glide range and is “deployable from high altitudes and airspeeds”, says Silent Arrow. It is about 1m (3.3ft) long and has 159kg (350lb) of cargo payload capacity. By comparison, the larger Silent Arrow GD-2000 can carry 740kg of cargo.
Silent Arrow says Precision Guided Bundles will also have swarming abilities, likely meaning the UAVs will be able to share sensor data and work together to find landing zones.
The details: The flight was a significant technical challenge, thanks to Mars’s bone-chilling temperatures (nights can drop down to -130 °F/-90 °C) and its incredibly thin atmosphere—just 1% the density of Earth’s. That meant Ingenuity had to be light, with rotor blades that were bigger and faster than would be needed to achieve liftoff on Earth (although the gravity on Mars, which is only about one-third of Earth’s, worked in its favor). The flight had originally been scheduled to take place on April 11 but was delayed by software issues.
Why it’s significant: Beyond being a significant milestone for Mars exploration, the flight will also pave the way for engineers to think about new ways to explore other planets. Future helicopter drones could help rovers or even astronauts by scoping out locations, exploring inaccessible areas, and capturing images. Ingenuity will also help inform the design of Dragonfly, a car-size drone that NASA is planning to send to Saturn’s moon Titan in 2027.
What’s next: In the next few weeks, Ingenuity will conduct four more flights, each lasting up to 90 seconds. Each one is designed to further push the limits of Ingenuity’s capabilities. Ingenuity is only designed to last for 30 Martian days, and is expected to stop functioning around May 4.
When you get a drone you might think that everything you need will come in the box, and on a basic level that is true. Most consumer drones come with everything you need to have a satisfying flying experience. However, the more you get into the hobby of flying drones, you begin to experiment with different things and start understanding some of the other gear you might need to get the most out of your drone.
Drone accessories are an often overlooked yet important aspect of the drone flight experience. Accessories like a carrying case, SD cards, extra batteries and propellers, and ND filters will help you get the most out of your drone both in performance and lifespan.
There are many accessories for your drone, but before you start loading up on gear, you should make sure that the accessories you choose fit your specific drone model. If not, you might purchase something that doesn’t work for your model, and then you’ll have to go through the hassle of returning it and getting a replacement.
This article will help you think through some of the most necessary and best drone accessories in 2021, as well as helping you make sure you get the right gear specific to your drone.
As I said, most drones do not absolutely require you to add any accessories. They are sufficient on their own out of the box. However, after flying drones for a while, I have often found myself thinking that I wish I had a certain accessory that would simply make things more convenient or efficient.
That is why I have compiled the following list of accessories that are extremely helpful for anyone who flies drones.
1. Carrying Case or Bag
Many of the high-end drones come with a flimsy carrying case just big enough to fit your drone and controller. They often do not fit everything else you might want or need to carry with you when you’re out flying.
Since the included bag isn’t really stellar, getting a quality case or bag for your drone is a great idea. There are many drone backpacks on the market, so you’ll have to shop around to find the one that will fit all your gear and suit your taste as well as fits your budget.
2. Extra Batteries
Once you start flying your drone, you’re going to want to fly it for longer without having to wait until your batteries charge. That’s why you’ll want to pick up a few extra batteries.
Since most batteries don’t last more than about 20-30 minutes at a time, a few extra drone batteries are a great investment to add to the drone accessories you are thinking about purchasing.
3. Charging Hub
While we’re talking about extra batteries, you may want to get a hub to charge your extra batteries. That way when you are ready to fly, all the batteries are ready at the same time.
4. Battery Bag
If you purchase extra batteries and want to transport them, it would be a good idea to get a battery bag. There are added concerns when transporting loose LiPo batteries, so a battery bag that is fireproof will help you transport them with confidence that you’re not going to start a fire.
5. High Capacity SD Cards
Most of us fly drones to capture incredible aerial views with high-definition cameras. We want to be able to share those views with others. If you’re going to be taking photos and videos with your drone, and want the best possible image files, you’re definitely going to need some high-capacity SD cards.
Artificial Intelligence (AI), which is also being hailed as a part of Industrial Revolution 4.0, has established its presence across myriad fields in recent years. AI has become somewhat of an umbrella term for a host of scientific and technological evolutions across various applications, computer sciences, and use cases.
Known predominantly as a series of technologies that promote intelligent execution of tasks in machines, AI is rapidly establishing itself as a reality in the current technological landscape, as well as a robust solution for future evolutions. The success of the AI field is characterized by the ever-increasing availability of computing power and data, backed by advancements in electronics miniaturization and machine learning (ML), among others.
While AI already has a significant presence across various commercial sectors such as retail and banking, its scope for defense and security is becoming more prominent in recent years. Artificial intelligence can be used for a plethora of defense applications including novel weaponry development, command and control of military operations, logistics and maintenance optimization, and force training and sustainment.
The integration of AI is also bringing more autonomy to military applications, particularly in unmanned machines and unmanned robot. These range from aerial autonomous vehicles to unmanned ground vehicles that can function with the help of environmental sensors and AI with little to no human intervention.
AUTONOMY IN LAND DEFENSE VEHICLES
The first truly autonomous vehicle came into being in 1984, developed by the ALV and Navlab projects from Carnegie Mellon University. Various research and development efforts have been undertaken since then, giving rise to a number of advanced Unmanned Ground Vehicles (UGV) prototypes. Advancements in technology have expanded the use of robotic autonomous vehicles across many fields in addition to UGVs, including Unmanned Under Water Vehicles (UUV), and Unmanned Aerial Vehicles (UAVs). UGVs are vehicles that operate on the ground, without the need for human presence onboard. They are the land counterparts of marine and aerial unmanned vehicles. All of these vehicles play integral roles in enhancing performance, efficiency, and safety across various applications, including military and civilian.
|
|
|
Understanding the effect of API changes in pharmaceutical processing |
Geschrieben von: bop03mo - 06.04.2022, 02:32 - Forum: Allgemein
- Keine Antworten
|
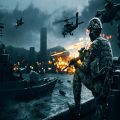 |
Understanding the effect of API changes in pharmaceutical processing
There is, of course, the natural curiosity of the scientist to understand what they are working with, and how the molecule’s journey influences its performance. The regulators who control medicines for the benefit of the patients who take them also require an understanding of what is happening to the drug molecules and particles. These two interests combine in Quality by Design (QbD) initiatives, where scientists and regulators come together to provide a thorough understanding of the manufacturing process of a dosage form, to ensure that it is effective and fit for purpose.
Over the past few years there have been significant scientific advances in understanding how a molecule joins, and is incorporated into, the crystal that is its home until it reaches the gastric intestinal (GI) tract. Despite the fact that the instant of nucleation remains a moment of magic or mystery, the growth of a crystal can be followed, understood and modelled and the process of isolating and drying formed crystals has been closely studied.
The milling process has opened itself to greater understanding in recent years, such that the mechanism and extent of crystal fracture can be followed, and the properties of the resultant particles predicted with greater accuracy. We can characterise the end material, with its single particles, agglomerates or aggregates by size, shape and surface area, and examine them in detail using microscopy techniques. At the end of the particles’ journey to the dosage form we can follow the disintegration of the dosage form and the dissolution of the particles in a range of model media. This data can be combined with other observations to develop models of how drugs will reach the bloodstream and eventually be eliminated.
Characterisation challenges
The use of chemical imaging to investigate the distribution of single components with a formulated sample have previously been reported2. However, due to limitations in the optical resolution of such systems, the individual particle sizes cannot be directly measured; pixels often contain more than one of the constituents. Pixels are instead colour coded to indicate the relative concentration of each constituent, thus enabling identification of ‘domains’ (areas of high component concentration). The relationship between domain size and particle size can be affected by multiple factors such as homogeneity, aggregation and morphology.
The challenge of characterising the primary particle characteristics of single components within multi-component systems has recently been addressed through the application of image-based particle characterisation with integrated Raman capability. This approach enables the characterisation of particles in terms of both size and shape. Utilising the Raman probe, the components within a blended sample can be sub-classified in terms of their chemistry, thus enabling the actual particle size distribution of individual components to be determined rather than the domain size.
Examples of this approach have recently been reported; Gamble3 demonstrated the process-induced attrition of a formulated API. It was demonstrated that blending and cone milling process steps had little impact on the primary particle size of the API, whilst a powder feed system, associated to a roller compactor, was observed to significantly reduce particle size. Such attrition could impact the processability of the material, both positively and negatively. This work highlighted that the powder feeding step, a hitherto overlooked sub-process, has a significant impact on the API/blend properties, and therefore requires consideration when selecting sources of process variation.
In addition to size, changes to the particle shape were also investigated. The combination of the two datasets provides insight into the attrition mechanisms within the unit processes. For the milling process, minor shifts in both size and shape could suggest a surface abrasion mechanism where the elongated particles undergo ‘chipping’. For the powder feed system, however, more significant shifts in both size and shape were proposed to suggest a bulk fracture mechanism where the particles undergo more complete fracture.
The work not only demonstrates that the input API size was impacted by the process, but that by characterising the API particle characteristics one could understand the mechanism of the change. This improved understanding of the intermediate API/blend characteristics could be applied to subsequent processing steps, removing the requirement to rely on the input particle characterisation data.
Subsequent work4 utilised the measured API attrition to determine the location of attrition events within the feed system. These efforts applied the understanding of the process/API interaction in order to develop a better elucidation of the unit process and to investigate the impact of varying process conditions on the extent of attrition. The study demonstrated how changes in the feed screw speed could alter the extent of attrition; increased feed rates resulted in increased levels of attrition. This raises an interesting issue; for such unit processes the feed system is often utilised as part of the automated feedback control to maintain the intermediate product characteristics, but if by changing the feed system we alter the blend characteristics, the tool used to control process variation could be a significant source of said variation.
Active pharmaceutical ingredients (APIs) refer to vital chemicals that are responsible for making the drug work. Depending on type, biotech/biological API, synthetic chemical API, high-potency API, plant extracts API, and classical fermentation API are some of the products available in the active pharmaceutical ingredients (API) market.
Analysts at TMR emphasize that the global active pharmaceutical ingredients (API) market will show promising growth on the back of increase in number of abbreviated new drug applications (ANDA. This aside, the market will gain advantage of growing focus on government bodies toward biomedical innovation.
Key Findings of Active Pharmaceutical Ingredients (API) Market Report
The global active pharmaceutical ingredients (API) market was pegged at approximately US$ 169.1 Bn in 2018.
Analysts at TMR highlight that the market will develop at a promising CAGR of 5.4% during 2019–2027.
On regional front, Asia Pacific is one of the prominent regions for the market growth due to presence of major important players.
The nature of active pharmaceutical ingredients (API) market is highly fragmented.
Active Pharmaceutical Ingredients (API) Market: Key Driving Factors and Promising Avenues
The global active pharmaceutical ingredients (API) market is estimated to experience prominent expansion opportunities during the forecast period of 2019 to 2027.This growth is attributed to growth in abbreviated new drug applications (ANDA) in the recent few years.
Similarly, the market for active pharmaceutical ingredients (API) will gain promising avenues for development on the back of rising focus of government authorities toward biomedical innovation.
The rising number of patients living with various critical health conditions such as cardiovascular diseases, cancer, and diabetes is stimulating noteworthy demand avenues in the global the active pharmaceutical ingredients (API) market.
This aside, the market for active pharmaceutical ingredients (API) is expected to gain prominent sales opportunities in all worldwide location on the back of increasing older population and sedentary lifestyles of major populace all across the globe.
In recent years, the active pharmaceutical ingredients (API) market is experiencing remarkable growth in demand for cost-effective drug substitutes. Several vendors engaged in the pharmaceutical drug manufacturing do not have adequate in-house capacity to fulfill this stupendous growth in demand. This situation has resulted in increased number of active pharmaceutical ingredients (API) producers. This scenario shows that the active pharmaceutical ingredients (API) market will grow at rapid pace in the upcoming years.
DEFINITION OF ACTIVE PHARMACEUTICAL INGREDIENT (API)
Any substance or mixture of substances intended to be used in the manufacture of a pharmaceutical dosage form and that, when used so, becomes an active ingredient of that pharmaceutical dosage form. Such substances are intended to furnish pharmacological activity or other direct effect in the diagnosis, cure, mitigation, treatment or prevention of disease or to affect the structure and function of the body (WHO Technical Report Series No.970,2012).
CLASSIFICATION OF ACTIVE PHARMACEUTICAL INGREDIENT (API)
API classification can be divided into:
i. Inorganic substances;
ii. Organic substances (isolated from materials of animal or human origin); and
iii. Organic substances (synthetic or semi-synthetic or isolated from herbal sources or micro-organisms).
SCOPE
i.The guideline encompasses the APIs of new products for registration and current / existing registered products. This is applicable to all pharmaceutical products (excluding traditional products, veterinary products, and health supplement products) both locally manufactured and imported.
ii. Biological active substances and immunological active substances are excluded from the scope of this guideline. Please refer to relevant guidelines available for Biologics.
iii. APIs used in products for export only (FEO) are exempted from the requirement for submission of the Drug Master File (DMF) and Certification of Suitability (CEP) in the product application.
iv. The API information required as in this guideline is only applicable for final APIs and not intermediate API
v. Separate registration of the APIs is not a requirement for the purpose of product registration. However, the required technical documentation pertaining to each API should be submitted with the new product registration application.
vi. Assessment of an API will be performed once submission of a new product registration application has been done.
vii. Assessment of an API will also be performed for a registered product prior to a product renewal application.
|
|
|
What to expect from aluminum clad wood windows |
Geschrieben von: bop03mo - 06.04.2022, 02:30 - Forum: Allgemein
- Keine Antworten
|
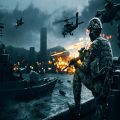 |
What to expect from aluminum clad wood windows
While comfort, benefits and popularity of modern uPVC windows are obvious and unquestionable in today’s market, there is definitely one thing uPVC windows can’t provide – they cannot replace the naturally warm appearance of real wood. So if you are among those homeowners who appreciate this particular feature and think it is one of the essential requirements, then you should consider installing aluminum-clad wood windows in your house.
Structure of an aluminum-clad wood window
Wood window with aluminum-clad consists of a wooden window sash and frame covered on the outside with strong and durable extruded aluminum material. This aluminum profile slides onto the wood and is independently secured in such a way that it allows both wood and aluminum to expand and contract without any interference.
Speaking about the wood material, it is necessary to mention that the most typical wood species used to make these window frames are solid hem and fir since those species are best known for a combination of strength and elegance.
The aluminum exterior is very robust and low maintenance, it will not require any paint job from you at all. It has a premium quality powder coating which makes it high resistance to weather influence and gives a better longevity.
As you probably can imagine, extruded aluminum profiles offer excellent structural stability and capability to withstand the harshest weather, successfully combating air and water infiltration.
Structural stability of these windows is achieved through pressure fitting assembly of all components which are then secured with screws, staples, mortise and tenon joints on the sash and rabbet joints on the frame.
An important detail is that aluminum-clad wood windows are constructed with a heavy-duty vinyl liner which has the purpose of preventing water accumulation diverting it from the wood to the exterior; also frames and sashes of these windows have drip edges.
Aluminum and wood surfaces have a seal barrier between them.
Operating windows such as casements and awnings are sealed with a heavy-duty compression foam which provides a higher level of energy efficiency.
Wood windows with extruded aluminum on the exterior have outstanding technical and performance properties as well as provide great flexibility in design opportunities.
Also, one of the most appealing characteristics of aluminum is that as a metal it offers a perfect foundation to apply premium baked-on polyester
a finish that can be factory painted in virtually any colour of your choice, thus ensuring your new windows will blend in perfectly well into the overall exterior design of your residence.
Wood window interiors can be painted or stained to match existing wood trims or any other interior accents.
For that reason, aluminum-clad wood windows are highly appreciated and recommended by designers and architects.
Aluminum-clad wood windows in general will cost you more than uPVC windows. You have to decide whether or not you are ready to go for this extra investment.
Aluminum clad wood windows have a longer lifespan than vinyl and offer better and more versatile design options, especially valuable in traditional-style homes. However, if you have a contemporary-style home you may be better off with custom uPVC windows.
Anyways, make sure to check if the company offers different product lines for various budgets.
Sunshine room related analysis
The sun room is also called the glass room, and its foreign name is winter garden. The sun room adopts a non-traditional building constructed with glass and metal frames to achieve the purpose of enjoying the sun and being close to nature. Sunshine House is a building respected by people in pursuit of nature and fashion at home and abroad. The Sunshine Room is a Shengli Industry that has been extensively researched in the Shanghai area of North China. It needs to be designed and built according to the needs of the site and personal preferences. The interior layout can be decorated according to personal preferences. The balcony or terrace sun room is in the whole room, so visual connection is very important. It needs to be considered to be consistent with the overall style of the building, and the overall tone should be as consistent as possible.
development stage:
In terms of materials and manufacturing methods, the aluminum clad wood sun room can be divided into five development stages: one is the sun room with pure wood structure, the other is the sun room with pure steel structure, the third is aluminum clad wood sun room with aluminum curtain wall structure, and the fourth is the steel-aluminum structure. Sun room.
1 After the discovery of the New World in Columbus and before the Industrial Revolution, many tropical plants, flowers and fruits entered Europe. The cold climate in Europe could not adapt to its production. European royal palaces and aristocrats like to enjoy this kind of things, so the royal craftsmen built some The greenhouse meets the needs of the nobles. Later, people discovered that these greenhouses are full of sunlight and green, so they can not only be used as greenhouses for cultivating tropical crops, but also can form a special space for leisure, entertainment, family gatherings and studios.
2 After the first industrial revolution, at the London World Expo in the 18th century, the United Kingdom built an exhibition hall covering an area of 80,000 square meters in order to showcase its industrial development. The protagonist is a glass building with a pure steel structure, which is the pinnacle of the early steel structure sun room. The mass production and application of steel at this stage further expanded the coverage of the early sun room. We can find the steel structure in the American feature film “The Sound of Music”, “Time Machine” and other films.
3 In the first half of the 19th century, due to the construction of skyscrapers, a new type of building material, aluminum, was widely used in building doors, windows and curtain walls because of its convenient molding, light weight, and high strength. At the same time, the modern daylighting roof and daylighting ceiling are also made of aluminum structure. And with the improvement of living standards, the sun room has become an indispensable living space for middle- and high-income families in developed countries. The sun room has become a way of life abroad. With the increase in the income level of the Chinese people and the massive construction of villas and duplex houses, the sun room has become an unstoppable development trend. At that stage, people built their own sunrooms according to their own wishes, liked wood structures close to nature, and industrialized steel structures. The aluminum structure has become the mainstream of the sun room at this stage because of the standardization of a large number of curtain wall materials.
4 The steel-aluminum structure of the sun room in foreign countries is mainly because some of the sun rooms are too large. Because of the high strength of the steel and the convenience of welding, the steel frame and aluminum welding rods are used. Build a large sun room. In China (especially in Shanghai), because the sun room is a new thing and the price is relatively high, in order to reduce the cost, a steel-aluminum composite (aluminum-clad steel sun room) is used, and steel as the main structure satisfies the strength problem. , And aluminum as a surface decoration makes the sun room more durable and more beautiful. It can be said that the aluminum clad wood sun room was a product in line with China’s national conditions at the beginning of this century. Its advantages are high strength and low cost. The disadvantage is that the construction period is long and there is no standardization. During the construction process, there are many uncontrollable factors, and the quality fluctuates greatly.
The sun room has a nice English name—winter garden, which literally means winter garden. It has two meanings: one is that it realizes the intimate contact between the room and the sun, even in the cold winter, you can also enjoy the warmth of the sun. Second, due to the unique thermal insulation effect of the sun room, the function of the greenhouse can be realized, even in the cold winter, it can also create a warm room environment for the family. The aluminum-wood composite sun room has an independent facade and top structure, which can be well integrated with any architectural style building. It has good sound insulation and heat preservation effect, and overcomes the defects of traditional sun room such as cold in winter and hot in summer, fog and ice. .
Classification of sun room:
The sun room is classified according to the roof material: glass roof sun room, broken bridge aluminum roof sun room, Degao tile roof sun room, color steel plate roof sun room.
The sun room is classified according to the facade material: Fenglu Broken Bridge aluminum doors and windows, Xingfa Broken Bridge aluminum doors and windows, aluminum clad wood doors and windows, and plastic steel doors and windows.
The sun room is classified by structure: steel structure sun room, aluminum structure sun room, steel and aluminum structure sun room, wood structure sun room.
Classified according to the location of the sun room: terrace sun room, garden sun room, closed door sun room, underground courtyard sun room, closed balcony sun room.
Sunrooms are classified according to their shapes: creative roof sunrooms, combined roof sunrooms, modeling roof sunrooms, and single inclined roof sunrooms.
European style sun room classification: Mediterranean style sun room, Byzantine sun room, Victorian sun room, Gothic sun room.
Various systems of the sun room: sloping roof skylight system, intelligent shading system, natural ventilation system, energy-saving Low-E glass, falling water system.
|
|
|
Wear in Injection Molds: To Float or Not to Float |
Geschrieben von: bop03mo - 06.04.2022, 02:28 - Forum: Allgemein
- Keine Antworten
|
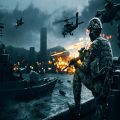 |
Wear in Injection Molds: To Float or Not to Float
One of the most difficult and challenging mold design issues is how to reduce or eliminate wear in injection molds. After all, the more wear that occurs, the higher the mold repair costs and/or the shorter the life of the mold. It’s a given that both the mold designer and the mold builder are committed to designing and building molds with the least wear, but it often seems to be an elusive target, especially with mold designs that have various actions taking place during the molding cycle.
The Wear Challenge
Mold designers and builders try to use the typical methods of minimizing wear—such as using differential metals; using low-wear coatings; specifying high metal hardness thus equating high hardness with low wear; designing shutoffs with high angles thus avoiding locking shutoff angles; and, many more concepts that their experience leads them to believe works best in specific applications. However, one design principle that is not well understood by mold designers and mold builders is wear caused by mold components that are under some load or stress during the molding cycle.
Mold designers and builders see the mold as it is built and especially during the mold assembly phase. Every attempt is made by them to assemble the mold components such that all inserts are fitted so the mold can be assembled by hand. In the better mold building shops, the use of hammers, pry bars and clamps is either strictly forbidden or the use is severely limited. Most molds then are assembled by hand with many of the mold components fitted with close tolerances but, by design, are not under a stress. On the bench then, the mold is in a Static condition.
The molder then sees the mold in a Dynamic condition. Components may be moved out of position due to a variety of molding conditions—such as being clamped up under tonnage; cams moving back and forth with the opening and closing of the mold; thermodynamic changes in the mold due to differential heating and cooling; and, stresses caused by injection pressures trying to move mold components out of position. Therefore, to the perceptive molder, a mold is alive or a dynamic device, not a static device during the molding process.
For years there has been a small group of molders and mold builders that recognize that molds are dynamic devices. They have recognized that this dynamic condition often has caused mold components to be forced out of a designed position. As forces are exerted on mold components, they move out of their desired position and may be forced against their mating components such that very high loads or stresses between these components occur. One of the more serious results of these stresses is high rates of mold wear. It is almost inevitable that increasing loads will increase the wear between these mold components.
Mold Alignment Approach
Molders who recognized that excessive wear was being caused by unanticipated stresses on the mold components began to use a variety of designs to address the problem. One of the most common was to utilize increasingly expensive mold alignment features—such as high cost straight line interlocks. The reasoning was that adding complex alignment features would not allow components to move regardless of the forces being exerted in the mold. Thus, instead of attacking the problem of movement, they continued to try to stop movement.
Wear Minimization Solution
The best solution to the problem of movement causing stress was very simple. If component A is forced against component B thus putting both components under stress, remove the stress. Removing the stress can be accomplished by a revolutionary principle and that is to incorporate designs that allow components to move in the mold.
Specifically, if component A moves due to stresses, allow component B to move with component A. If both move together, stress is reduced or eliminated—depending on the design concepts. Result: when stresses are eliminated, mold wear is substantially reduced.
Float Concept
This concept of allowing components to move or float flies in the face of the mold builder teachings. It is a concept that is foreign to their experience and teachings. The industry generally agrees that the one type of mold that has the most potential for wear is unscrewing molds (i.e., molds designed to make a part with an internal thread). Today, molders that have adopted this concept and incorporate this into their designs are building very successful molds and are seeing substantial savings in repair costs.
Molders that are having their molds built with copper alloys to take advantage of increased mold cooling discovered that copper alloys are easily damaged. When copper alloys are formulated to resist wear, thermal conductivity can be significantly reduced. Molders then were forced to choose between fast cycle times due to increased mold cooling or better wear resistance. Molders that are using copper alloys successfully in molds have learned that float mould components may be the most successful mold design concept to minimize wear. Floating mold components therefore allow the molder to have minimal wear and fast cycle times.
Key to Success
The key issues in floating mold components are to determine which components will be floated and how to actually design them to float. Molders that have successfully determined how to achieve this are seeing faster cycle times and lower mold repair costs.
30 holes egg tray mould use for paper pulp machinery
Egg tray moulds features:
1. Our mould is durable and easy for maintenance and replacement.
2. The price of our mold is reasonable comparable to its high quality.
3. We make lineation before drilling holes to ensure all holes distributed evenly. The holes size and spacing of holes of our suction molds are better for high efficiency. We use stainless steel mesh and use pre-forming technology when making them, this make the molds looks better and increase the efficiency, and the products produced are with better looking.
Our pulp molds have been mounted successfully on the international pulp molding machine, such as reciprocating pulp molding machine, rotary pulp molding machine. And we made many molds for pulp molding machines made by some famous company in the world.
In the process of producing plastic chemical barrel moulds, due to the influence of raw materials, molds, equipment and processes, the surface of the plastic chemical barrel moulds will appear to be blooming. At this time, we need to conduct on-site inspections. The plastic chemical barrel mould manufacturers introduce the process as follows:
Whether the material is wet: check whether there is obvious water and moisture phenomenon in the data. You can visually observe that there is no water and moisture phenomenon in the outer package. Open the material bag and touch the data to see if there is moisture. Difficult to dry.
2. Feeding link: Check the feeding link to ensure that the barrel mould and feeding process are clean to prevent foreign materials from mixing in and check the data particles for obvious bees.
3. Checking the drying equipment: Check the drying equipment to see if the heating temperature of the drying equipment is normal (there is a thermometer on the bottom of the barrel mould), whether the air blows in and out smoothly, and you can feel the wind out of the air outlet with your hand.
4. Is there a foaming phenomenon in the shot block? Exit the shot block to see if there is foaming in the block. There should be no foaming in the normal production materials. If there is foaming, there is gas. Continue to dry or lower the material. Tube temperature.
5. Check the nozzle heating ring and barrel mould: Check whether the nozzle heating ring and barrel mould are heated normally. The nozzle can be tested with a strip on it. The strip is normal if it melts. The temperature of the barrel mould can be viewed on the temperature screen, and the deviation from the set value cannot exceed 20 degrees.
6. Injection process: Check the key conditions that affect the silver pattern in the injection process. The loosening position should be as small as possible, the back pressure can be appropriately increased, and the injection speed can be increased and decreased in both directions.
7. Mold problem inspection: The inspection mold has no effects of oil leakage, air leakage, and water leakage.
Why Does Mold Grow on Plastic?
Many people believe that mold cannot grow on plastic or polymer materials. Mold generally can't break down plastic easily.
However, plastic contains many additives, such as plasticizers, cellulose, lubricants, stabilizers, and colorants to help provide desired features, and these additives ARE very easy for trash can mould to break down.
Once mold becomes established by breaking down the easily digested ingredients, the acids they produce as by-products of growth break down the resin into a more useable food source.
To learn more, read up on the ASTM G 21 test method that describes this process in greater detail.
What Does Mold Need to Grow on Plastic?
Mold is a broad term that covers a variety of species. Able to survive in the strangest of places, mold only has a few requirements to survive and thrive in any environment.
In addition to additives already embedded in the plastic itself, as mentioned above, food (dust, dirt, organic materials), moisture, and suitable temperature all provide enhanced conditions for mold growth to take hold.
While plastic might not be the preferred surface for sustaining mold growth, it can easily meet all the prerequisites if exposed to food, humidity, dirt, and dust.
These conditions vary widely between species. In fact, even the International Space Station (ISS) astronauts spend hours every week battling mold growth.
However, their fights have not gone unnoticed. Through their research, we have gained an indispensable look into the harsh environments of mold and its spores. The ISS scientists replicated the X-ray and UV exposure found around the space station and found spores surviving up to 100 gray worth of X-rays.
To put that in perspective, 5 gray is all that is needed to kill a person, while ? gray is enough to induce radiation sickness.
So, is mold the next Terminator T-1000? Well, not for us resourceful humans!
|
|
|
What are the advantages and disadvantages of aluminum tube Tubing? |
Geschrieben von: bop03mo - 06.04.2022, 02:26 - Forum: Allgemein
- Keine Antworten
|
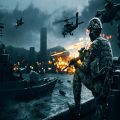 |
What are the advantages and disadvantages of aluminum tube Tubing?
Aluminium’s benefits make it a modern, efficient and effective material for building and construction .It’s hard to list off all of the advantages that aluminum tube has to offer. The tremendous diversity in aluminum tube alloys has allowed for faster production processes that are more efficient and save money. As the production of aluminum tube has advanced, making it cheaper and more adaptable, it has allowed for breakthroughs that would have seemed impossible just a few years previously.
Flexibility
Aluminium’s combination of properties mean that it can be easily shaped by any of the main industrial metalworking processes, including rolling, extrusion, forging and casting, guaranteeing virtually unlimited design potential.
Light-weight
Aluminium’s light weight makes it cheaper and easier to transport and handle on site.
Strength
The use of aluminium in buildings assists architects meet performance specifications while minimising expenditure on foundations. Alloyed aluminium can be as strong as steel at only a third of the weight.
Durability
Aluminium building products are made from alloys that are weather-proof, corrosion-resistant and immune to the harmful effects of UV rays, ensuring optimal performance over a very long lifetime.
Corrosive Resistance
Aluminium’s natural oxide coating provides an effective protective barrier against elements that wear other metals.
Insular
A layer of insulated aluminium cladding can be four times more effective than uninsulated timber cladding, 100mm of brick, or 200mm of stone masonry.
Recyclability
Aluminium is 100% recyclable and uses only 5% of the energy used to make the original product. Almost all aluminium used in construction is recycled.
First of all, although aluminum tube does have a great strength-to-weight ratio, when we’re just talking strength alone, stainless steel is often stronger. So for structures where weight isn’t an issue, steel might be the way to go. In addition, another drawback is that certain alloys of aluminum tube do not have the same level of corrosion resistance as stainless steel. That’s why, for example, aluminum tube is not as popular a choice for electrical cables as it used to be. When deciding on an alloy, it’s very important to know exactly what the material will be exposed to so that you know that it will be able to withstand the elements for as long as necessary.
Advantages of Aluminum Extrusion:
Aluminum is a very commonly specified material for use in extrusions and shape profiles because it possesses mechanical characteristics that make it ideally suited for the shaping and forming metal from billet sections. The high malleability of aluminum means that the metal can be readily shaped into a variety of sections without expending significant energy on the tooling or forming process, and the melting point of aluminum is also generally on the order of half that of ordinary steel. Both of these facts mean that the aluminum extrusion process has a relatively low energy footprint translating into low tooling and manufacturing costs. Finally, aluminum also possesses a high strength to weight ratio, making it an excellent choice for industrial applications.
Types of Profiles
A wide variety of intricate aluminum extrusion profile types can be created at varying thicknesses. These profiles can feature a wide variety of intricate void spaces, as necessitated by the end use application. A wide range of internal voids are available in order to facilitate a wide variety of automation applications and also satisfy any performance weight requirements. The most common type of aluminum profile is the hollow beam profile which is simply a variation of the square profile. There are also other profile types such as the triangular, single radius, and L-shaped profile.
Aluminum is an amazing metal that has had a great impact on modern industry. Its versatility and adaptability mean that it can be used in numerous applications, more cost effective and with greater durability than many other materials. No matter what your product or job, there’s likely an aluminum alloy that’s right for you.
The downside to this tremendous diversity is that aluminum offers a wide range of options, sometimes making it difficult to know which grade is most suitable. For instance, aluminum bar is frequently bought in a variety of alloys and a number of distinct shapes, including flat, hexagon, round and square. That’s not to mention the many specialty, high-performance aluminum alloys that are becoming more affordable every year.
In a perfect world, a manufacturer could take the time to test and prototype a whole range of different materials to learn which type of aluminum works best for a particular application. This process can be time consuming, and even though aluminum is well known for its ease of use (particularly for prototyping) it may be necessary to act swiftly. That’s why working with a knowledgeable, responsive material supplier is a necessity.
WHAT ARE THE BENEFITS OF WORKING WITH ALUMINUM BAR?
As the most abundant metal found in the Earth’s crust, aluminum is a bountiful resource that offers a number of key benefits. Primary among them, aluminum exhibits an amazing strength-to-weight ratio that has made it a transformative material in architecture and engineering. It is also extremely durable and can withstand heavy forces. For instance, in automotive applications aluminum can absorb twice the crash energy of steel, allowing for vehicles to be simultaneously lighter and safer.
Another of the most prized properties of aluminum bar is its corrosion resistance. The metal naturally forms a protective oxide coating on its surface that makes it highly resistant to most types of corrosion. Some alloys are even able to endure in marine environments for extended periods of time. Furthermore, aluminum can be treated in a number of ways such as anodizing, painting or lacquering to increase its resistance even further.
Aluminum is also very formable, making it easy to work with and allowing the metal to be adapted to all kinds of applications. Aluminum bar can be bent and shaped in any number of ways. Other benefits include high ductility, thermal/electrical conductivity and reflexivity. Aluminum is also hygienic, making it extremely popular in industries such as food, beverage and medical.
Furthermore, aluminum is easy to recycle, meaning not only is it good for the environment but it is also cheaper to work with because there is much less waste material.
Different aluminum grades have different properties, so it’s important to know which alloy will work best for your particular application before getting started.
Aluminum Coil Classification
1000 Series Aluminum Coil
The 1000 series aluminum coil represents the 1000 series aluminum sheet, which is also called a pure aluminum sheet. Among all the series, the 1000 series belongs to the series with the most aluminum content. The purity can reach more than 99.00%. Because it does not contain other technical elements, the production process is relatively simple and the price is relatively cheap. It is currently the most commonly used series in conventional industries. Most of the products circulating in the market are the 1050 and 1060 series. The 1000 series aluminum plate determines the minimum aluminum content of this series according to the last two Arabic numerals. For example, the last two Arabic numerals of the 1050 series are 50. According to the international brand naming principle, the aluminum content must reach 99.5% or more to be a qualified product.
2000 Series Aluminum Coil
2000 series aluminum coils represent 2A16 (LY16), 2A06 (LY6); 2000 series aluminum plates are characterized by high hardness, of which the copper element content is the highest, about 3-5%. 2000 series aluminum plates are aviation aluminum materials, which are not often used in conventional industries.
3000 Series Aluminum Coil
The representative of 3000 series aluminum coil is mainly 3003, 3003, 3A21. It can also be called an anti-rust aluminum plate. The 3000 series aluminum plate is made of manganese as the main component. And China’s 3000 series aluminum plates are relatively outstanding in the market.
|
|
|
What is covered yarn? |
Geschrieben von: bop03mo - 06.04.2022, 02:24 - Forum: Allgemein
- Keine Antworten
|
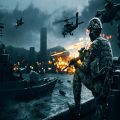 |
What is covered yarn?
Covered yarns – yarns that consist of at least two yarns. The yarn that is wrapped around gives the looks whereas the core (the fine wire) still provides the functionality (like conductivity).
What is spandex used for?
Spandex is used to make garments where a lot of permanent elasticity is required, e.g. in tights, sportswear, swimwear and corsetry. It is used in garments that are intended to cling to the body, while at the same time remaining comfortable. For this type of garment 15 – 40% spandex is used.
What is air covered yarns?
Air Covered Yarn is a regular intermingled yarn, the covering filament yarn and Spandex are drawn meanwhile from a special jet nozzle where the yarns are air-jetted at regular intervals by high compressed air. The Air-jet Covered Yarn needs sizing for warp knitting and can be used for weft knitting directly.
Where covered yarn is used?
DOUBLE-COVERED YARNS Flat or textured polyamide yarns can be used to create the double covering. Double-covered yarn is used for the high-end and top-quality clothing, lingerie and hosiery markets.
What is T400 yarn?
Lycra T400 fiber is a multi-component yarn in which different polymers are joined together within each filament. Since the crimp is not mechanically induced, Lycra T400 fiber gives greater, more durable stretch and recovery, as well as a softer, smoother hand than textured yarns.
What is nylon spandex fabric?
Nylon Spandex is classified as an elastomeric fiber or merely a fiber or material that can expand over 500% without breaking. Clothes made from Nylon Spandex are more comfortable, even though, they are tight. Nylon Spandex fabric is very much lighter compared to natural rubber that is easier on the skin.
What is nylon spandex?
What is spandex yarn?
Spandex yarn is a man-made elastic fiber developed. It is a manufactured texture material with elastic properties of the sort referred to nonexclusively as “Elastic Yarn”. Spandex yarn is ordinarily used in athletic or dynamic dress. This is known as lycra fetishism. Lycra is regularly one of the textures in tights.
What is air covered spandex yarn?
Air covered yarn is manufactured by creating a physical intermingle of INVIYA? yarn with other synthetic filament like Polyester or Nylon by the help of compressed air applied through a nozzle. INVIYA? is applied during a draw texturizing process of Polyester or Nylon to avoid the extra process of spandex application.
What is covering power in textiles?
Covering power is an expression of the degree to which a yarn imparts cover to a fabric. The waviness of a textured filament yarn. This characteristic may be expressed numerically by the crimp elongation.
How is spandex used in a knitting project?
It is generally used in alternate rows of knit yarn. Finally, the covered yarn can be used in every row – in every thread of the knit – for three dimensional stretch. Covered Spandex is also used. The covering involves wrapping the Spandex in the main yarn in the nylon hosiery, so that the Spandex becomes the yarn core.
Yarn is an extensive continuous length of fibers, which is used in sewing, knitting, textiles, crocheting, embroidery, weaving, and ropemaking. Recycling of cotton is known as recycled yarn, which minimizes unnecessary wastage, and is a more sustainable alternative to disposal. Cotton recycling can be done from textile leftovers and older or earlier used garments. Recycled yarns are used for making carpet, clothes, and furnishing items for car and buildings.
The global recycle yarn market has witnessed significant growth due to upsurge in demand for recycled yarn form home textile, industrial purposes, and apparel. In addition, innovations in production process fuel the growth of the market. However, volatile raw material prices and lack of availability restrain the market growth. Rise in demand for organic-based yarns is expected to provide significant growth potential for the market.
The global recycle yarn market is segmented based on type, application, and geography. On the basis of type, the market is categorized into recycled PET yarn, recycled cotton yarn, and recycled nylon yarn. Carpet, clothing, car, building, and other are the applications of recycle yarn. Geographically, the market is analyzed across North America, Europe, Asia-Pacific, and LAMEA.
The major players operating in the global market are focusing on key market strategies such as mergers, acquisitions, collaborations, and partnerships.
Key Benefits
This report provides a quantitative analysis of the current trends, estimations, and dynamics from 2016 to 2025 to identify the prevailing market opportunities.
Major countries in each region are mapped according to the individual market revenue.
The region-wise and country-wise recycle yarn market conditions are comprehensively analyzed.
This study evaluates the competitive landscape and the value chain analysis to understand the competitive environment across geographies.
This study evaluates the competitive landscape and the value chain analysis to understand the market scenario across geographies.
Air Covered Yarn is a regular intermingled yarn, the covering filament yarn and Spandex are drawn meanwhile from a special jet nozzle where the yarns are air-jetted at regular intervals by high compressed air.
The Air-jet Covered Yarn needs sizing for warp knitting and can be used for weft knitting directly. The production efficiency of Air-Covered Yarn is much higher than Conventional Covered Yarn (also known as SCY – Single Covered Yarn or DCY – Double Covered Yarn) and the price is also much lower, which would reduce much cost for downstream textile company.
Nylon was the first fabric made entirely in a laboratory. A synthetic material derived from petroleum, it first became available around World War II and was used for military products and as a silk replacement for items such as stockings. Now, you’re more likely to find it in activewear, swimwear and other technical performance garments because of its durability and useful stretch properties.
The production of nylon is similar to that of polyester, with similar environmental consequences. Like polyester, nylon is made from a non-renewable resource (oil) in an energy-intensive process. It sheds microplastic fibers that end up in waterways and oceans every time it is washed, and because it is not biodegradable, it will end up sitting in a landfill at the end of its product life cycle.
As an organization, Textile Exchange supports the apparel and textiles sector in switching to preferable materials that have a more positive impact on people and the environment compared to conventional. Recycled nylon is considered a preferred alternative to virgin nylon and bio-based nylons (produced with renewable raw materials) potentially offer a promising alternative.
Recycled nylon is usually made from pre-consumer fabric waste, although it also may come from post-consumer materials such as industrial fishing nets. Several "chain of custody" standards track recycled nylon through the supply chain, including the Recycled Claim Standard (RCS), Global Recycled Standard (GRS) and SCS Recycled Content.
Probably the best-known regenerated nylon product is Econyl, the first post-consumer recycled nylon to hit the market from Italian manufacturer Aquafil. Econyl is made of nylon waste from landfills and oceans in a closed-loop process and is infinitely recyclable. According to Aquafil, Econyl avoids about 50 percent of carbon dioxide emissions and uses about 50 percent less energy compared to nylon recycled yarn.
A high-performance yarn electrode material, cotton/graphene/polyaniline, is synthesized by coating primary fiber cores inside cotton yarns with graphene sheets and followed by further growing polyaniline nanowire array layers through in situ polymerization of aniline. The electron transportation is enhanced by the 3D graphene conductive network on cotton fibers, which further bridges the polyaniline nanowires. The polyaniline nanowires with small diameters ensure high electrochemically active surface area. The spaces within the polyaniline nanowire array layers and the hierarchical pores of the entire yarn electrode benefit the fast electrolyte ion diffusion. The unique 3D yarn electrode structure results in an excellent electrochemical performance.
|
|
|
5 Reasons You Shouldn’t Use Homemade Laundry Detergent |
Geschrieben von: bop03mo - 06.04.2022, 02:19 - Forum: Allgemein
- Keine Antworten
|
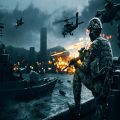 |
5 Reasons You Shouldn’t Use Homemade Laundry Detergent
My goal of this heading isn’t to give you an exact recipe, but to break down the common ingredients in homemade laundry soaps.
Most homemade laundry ‘detergents’ are made up of water softeners like baking soda, washing soda, and borax and a cleaning agent which is typically a grated bar of soap.
The goal of the water softener is to… you guessed it! Soften the water. You might have heard the terms hard water and soft water which has to do with the level of minerals like calcium and magnesium in the water.
The most common water softeners used in homemade laundry soap borax and washing soda, but they’re marketed as laundry BOOSTERS because they are meant to aid a detergent not replace one.
If you have really hard water, like I do in California, using a homemade laundry soap is even worse because the high levels of calcium and magnesium make it almost impossible for the soap to wash free from the textiles.
While the laundry boosters help some, its not an appropriate replacement for detergent.
DIY laundry ‘detergent’ can RUIN your clothing:
When you’re using homemade laundry soap you can ruin your clothing. I know this from personal experience, but lets take a little bit deeper look into why.
If you use soap on your hands in the kitchen or bathroom sink you’ve probably had to deal with soap build up or soap scum.
That’s happening to your clothes, and worse… your washing machine which we’ll address in the next heading.
Every time you wash your clothing soap build up buries itself inside of the textiles. This build up can create a water repelling effect which might be why your reusable towels aren’t super great at absorbing water, but can also leave an oily residue behind.
When soap accumulates in your clothing it will actually attract and trap dirt in your textiles. It quite literally makes your clothing DIRTY the exact opposite thing you want from a laundry detergent…
How Does Laundry Detergent Affect the Environment?
When we dump a capful of concentrated cleaning detergent into our laundry machine, we don’t really think much of it, especially not in an environmental sense. After all, as far as most of us are concerned, something as common and innocuous as laundry detergent couldn’t possibly be bad for the planet. Some brands even make a point to say so! Unfortunately, like so many man-made chemical inventions, detergent is far from completely harmless.
What are laundry detergents made from?
Detergents are hardly naturally occurring. Most of the most popular commercial brands are manufactured using synthetic chemical compounds. This makes them very different from soap, which is made from natural substances like lye and plant saponins. This makes sense, of course, as soap goes directly on the skin; laundry detergent does not.
Instead, laundry detergent is added to dirty laundry, where it does its job “lifting stains” and “preserving colors” before getting washed out, diluted, and sent down the drain with the wastewater from your washing machine. Unfortunately, the chemicals in these detergents can have a far-reaching environmental impact.
What are the environmental effects of detergents?
Detergents can contain several chemical compounds that have negative environmental effects. Phosphate-containing laundry or dish detergents can react adversely when they finally reach the water table. The nitrogen in these detergents reacts with phosphorus in the water, creating nutrients that stimulate the growth of algae in freshwater. According to Lenntech, a company from the Netherlands, this type of algae uses up the oxygen in the water in a process called eutrophication. Over time, this slowly depletes the oxygen in a body of water, ruining the ecosystem.
Other detergents contain surfactants, or surface-active agents, which are chemicals that reduce the surface tension of oil and water. For the detergent, these surfactants help dirt to “lift off” and stay out of clothing. The problem is, they also happen to be highly toxic to aquatic life. According to the U.S. Environmental Protection Agency (EPA), surfactants break down the mucus layer that coats fish, protecting them from parasites and bacteria.
They also reduce the surface tension of water, making it easier for waterways to absorb pollutants and pesticides. Heck, they don’t even break down well or dilute. Instead, surfactants only breakdown further into more toxic byproducts.
Hand Sanitizer Use Out and About
Germs are everywhere! They can get onto hands and items we touch during daily activities and make us sick. Cleaning hands at key times with soap and water or hand sanitizer that contains at least 60% alcohol is one of the most important steps you can take to avoid getting sick and spreading germs to those around you.
There are important differences between washing hands with soap and water and using hand sanitizer. Soap and water work to remove all types of germs from hands, while sanitizer acts by killing certain germs on the skin. Although alcohol-based hand sanitizers can quickly reduce the number of germs in many situations, they should be used in the right situations. Soap and water are more effective than hand sanitizers at removing certain kinds of germs like norovirus, Cryptosporidium, and Clostridioides difficile, as well as chemicals.
Hand sanitizers also may not remove harmful chemicals, such as pesticides and heavy metals like lead.
Handwashing reduces the amounts of all types of germs, pesticides, and metals on hands. Knowing when to clean your hands and which method to use will give you the best chance of preventing sickness.
What are the qualities of a good shampoo?
The characteristics of a good shampoo are fairly obvious. A shampoo should clean away the oil and dirt, rinse out easily, and leave your hair shiny, manageable, and flexible.
Research has shown that various chemicals lurking inside shampoo may induce serious health risks, like memory loss, eye and skin irritation, hair follicle damage that can lead to hair loss, and even cancer.
While the U.S. Food and Drug Administration classify personal care products, it does not regulate them. Therefore, there are no legal guidelines or boundaries for shampoo manufacturers to follow.
The descriptive “all-natural” has become a buzzword in the beauty world for environmental friendliness. What some shampoo makers leave out, however, is they still use the lathering agents, emulsifiers and synthetic fragrances that contain hundreds of harmful chemicals.
Additives to avoid:
* Propylene glycol, known as the main ingredient in antifreeze, is also found in makeup, toothpaste and in your shampoo. It can cause allergic reactions.
* Sodium lauryl sulfate and ammonium lauryl sulfate are common causes of eye irritation. They can also damage hair follicles. When absorbed into the body from continuous contact, they can bring on asthma attacks.
* Synthetic fragrances contain hundreds of chemicals, some of which have been known to cause headaches, dizziness, rash, hyper pigmentation, coughing and vomiting.
*The National Toxicology Program found that applying diethanolamine to a mouse’s skin induced liver and kidney cancer. DEA is readily absorbed through the skin and can also be toxic to the brain.
The spread of the coronavirus disease COVID-19 has spurred a surge in sales of cleaning and disinfection products. The Centers for Disease Control and Prevention (CDC) recommends regular cleaning of frequently touched surfaces, along with thorough hand washing—both standard practices for helping slow the spread of viruses and bacteria. But consumers will be disappointed if they go looking for a product that specifically promises to kill SARS-CoV-2, the virus that causes COVID-19.
Although there’s good evidence the novel coronavirus is one of the easiest types of viruses to kill, scientists are still determining its exact nature and how big a role surface transmission plays in its spread. As researchers rush to understand the new pathogen, the US EPA is working to provide the public with information about disinfectants that can help slow its spread. Such claims won’t be allowed in brick-and-mortar stores, though, until more testing can be done.
|
|
|
|